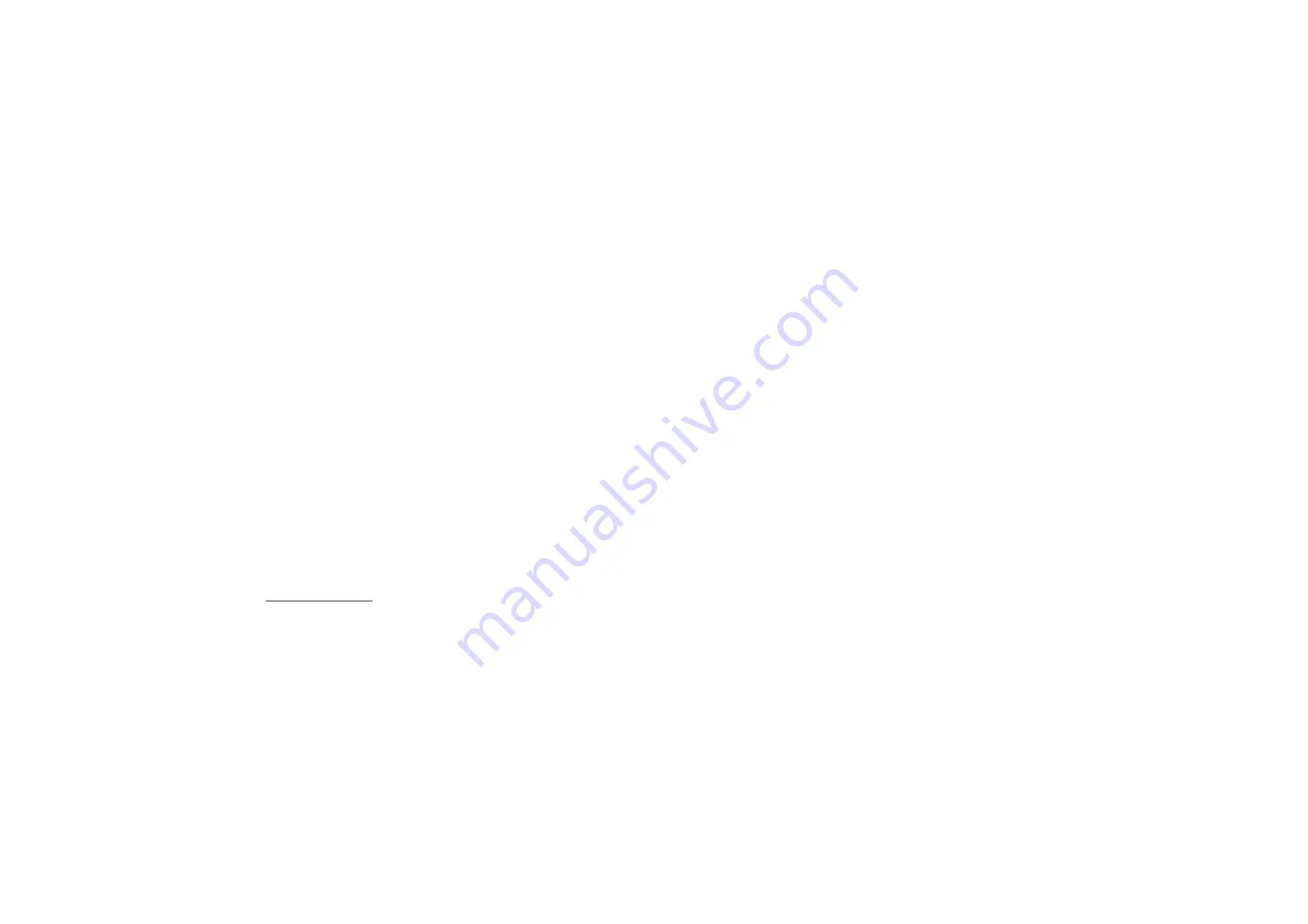
ZZ839/3
12
13
ZZ839/3
8.12
TIME CONTROL and SWITCH REMOVAL:
8.12.1 Ensure that the electrical is isolated.
8.12.2 Remove the appliance front door, release the 2 x securing screws and hinge down the fan chamber door.
Time Control
removal:
8.12.3 Disconnect conductors ‘
C1
’, ‘
C2
’, ‘
C3
’ and ‘
C5
’ from the Time control.
8.12.4 Release the 3 x fixing nuts, and withdraw the Time control.
8.12.5 Refitting or replacement is in reverse order.
8.12.6 Set Time Control to required ON and OFF times.
8.12.7 Set Time Control to correct time.
Switch removal:
8.12.8
Disconnect the conductors from the switch terminals.
8.12.9
Depress the retaining clips and press the switch out of the fascia panel.
8.12.10
Refitting or replacement is in reverse order.
WARNING: The fascia panel is held in place by push fit retainers which must be removed with caution to avoid
causing damage to the support pins. Removal of the fascia is not advised unless it is intended to be replaced.
8.13
FAN DELAY CONTROL/LIMIT SWITCH REMOVAL:
8.13.1 Ensure that the electrical supply is isolated.
8.13.2 Remove appliance front door, release the 2 x securing screws and hinge down the fan chamber door.
8.13.3 Release the 2 screws securing the Limit Switch cover plate and withdraw the control from the
appliance by drawing the conductors through the grommet in the fan chamber floor.
8.13.4 Disconnect the required control/switch, noting the position of wiring for subsequent reconnection.
8.13.5 Release the 2 x securing screws , and withdraw the required control/switch
8.13.5 Refitting or replacement is in reverse order, ensuring that the Igniter earth lead (if fitted) is grounded by the Limit
Switch cover plate securing screw.
8.14
HEAT EXCHANGER ACCESS:
8.14.1 Ensure that the electrical supply is isolated.
8.14.2 Remove the appliance front door.
8.13.3 Release the 2 screws securing the heat exchanger access cover plate, and withdraw the cover plate and gasket.
8.13.4 Withdraw the ‘U’ baffle from the heat exchanger.
8.13.5 Reassembly is in reverse order.
NOTE: When reassembling, ensure that the ‘U’ baffle correctly locates within the heat exchanger, gaskets are soundly
sealed, and the heater is fully re-commissioned.
9.
DEFECT DIAGNOSIS
9.1
IMPORTANT: If an electrical defect occurs after installation of the appliance; preliminary earth continuity,
polarity, and resistance to earth checks should be carried out with a multimeter. On completion of any
maintenance/fault-finding task that has required the breaking and remaking of electrical connections, then
checks of continuity, polarity, and resistance to earth must be repeated.
9.2
WARNINGS:
9.2.1
When purging or checking gas supplies, ensure that the ventilation to the room or cupboard is adequate, and that
all naked lights are extinguished.
9.2.2
SYSTEM E-T models:
a.
When carrying out any electrical testing, a test meter MUST be used, since low resistance test devices can
cause damage to the Electronics module.
b.
Before commencing defect diagnosis, ensure that the Thermista-stat is set to maximum, the mains supply
is ‘ON’ and the time control (if fitted) is at an ‘ON’ position.
c.
Care is to be taken during the replacement and handling of electronic assemblies (i.e. electronic panel,
airflow sensor or Thermista-stat), it is not practical to rectify defects on these assemblies, except at the
manufacturer, and any attempt to do so may render the guarantee or factory replacement arrangement
invalid.
SYMPTOM
POSSIBLE CAUSE
REMEDY
a.
Pilot will not light.
i. No gas supply to heater.
Check for gas at inlet pressure test
point on multifunctional control.
ii. Gas supply pipe not purged.
Purge gas supply pipe in accordance
with BS 6891.
iii Pilot orifice restricted.
Clear pilot orifice or replace pilot injector.
iv Piezo system faulty.
Check igniter, lead, and electrode.
v. Excessive gas supply pressure.
Check that mains gas pressure is 20mbar,
and reduce if necessary.
b.
Pilot lights but goes
i. Connection between thermo-
Check connection is secure.
out on releasing START
couple and multifunctional
button during initial
control not secure.
light-up, or after
normal operation.
ii. Faulty Multifunctional
Replace Multifunctional control.
control.
iii. Faulty thermocouple.
Replace pilot assembly.
iv. Pilot orifice restricted.
Clear pilot orifice or replace pilot injector.
v. Air inlet/flue outlet fitted
Check that inlet/outlet arrangements conform
incorrectly.
to Fig. 3, and that seals are air tight.
c.
Main burner lights but
i. Loose electrical connection
Check connections.
fan fails to run after
on Fan Delay Control.
approximately 3 mins.
ii. Faulty Fan Assembly.
Replace, taking care to not damage impeller.
iii. Faulty Fan Delay Control.
Replace.
iv. Burner pressure setting incorrect.
Adjust.
d.
Main burner opera-
i. Gas rate or burner pressure
Check gas rate and burner pressure
ting intermittently
setting high.
setting.
with fan running.
ii. Temperature rise excessive.
Adjust fan speed or gas rate accordingly.
iii. Air filter or return air path
Check filter is clean and air path is clear.
restricted.
iv. Excessive number of outlets
Open additional outlets.
closed.
e.
Main burner opera-
i. Gas rate or burner pressure
Check gas rate and burner pressure
ting with intermittent
setting too low.
setting.
fan operation.
ii. Fan delay control faulty
Replace.
f.
Fan runs for excessive
i. Fan delay control faulty.
Replace.
period or operates
intermittently after
main burner shuts down.
g.
Noisy operation.
i. Gas pressure too high.
Check burner pressure setting.
ii. Noisy fan motor.
Replace fan assembly.
iii. Fan speed setting too high.
Adjust fan speed.
SYSTEM E-T models:
h.
Incorrect operation
Fault related to SYSTEM E-T
Consult diagnostic chart and follow
of fan or main burner.
Control system (refer to pages 14 -18) recommended procedure.