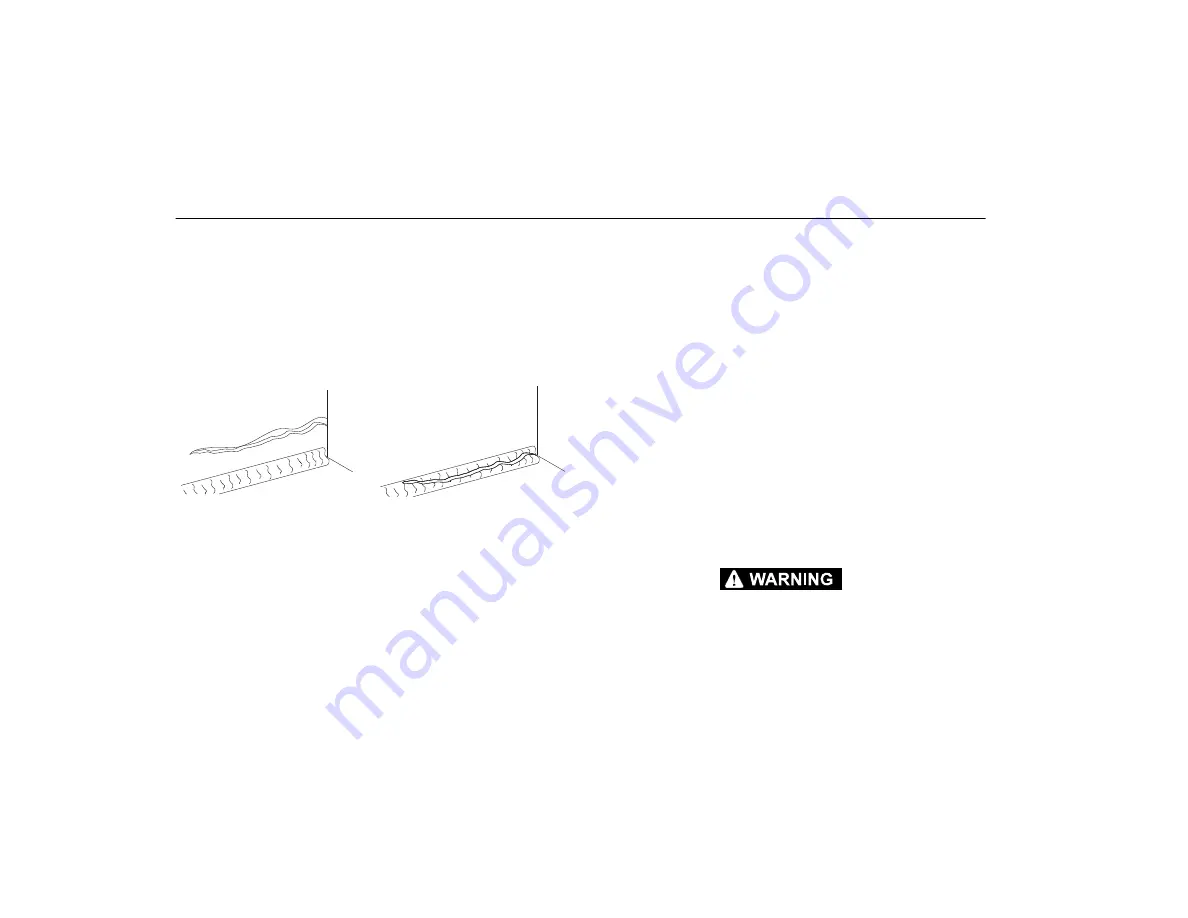
SECTION 2 - USER RESPONSIBILITIES, MACHINE PREPARATION, AND INSPECTION
2-8
3121734
Pre-Start Inspection
The Pre-Start Inspection should include each of the following:
1.
Cleanliness –
Check all surfaces for leakage (oil, fuel, or bat-
tery fluid) or foreign objects. Report any leakage to the
proper maintenance personnel.
2.
Structure
- Inspect the machine structure for dents, dam-
age, weld or parent metal cracks or other discrepancies.
3.
Decals and Placards
– Check all for cleanliness and legibil-
ity. Make sure none of the decals and placards are missing.
Make sure all illegible decals and placards are cleaned or
replaced.
4.
Operation and Safety Manuals
– Make sure a copy of the
Operation and Safety Manual, AEM Safety Manual (ANSI
markets only), and ANSI Manual of Responsibilities (ANSI
markets only) is enclosed in the weather resistant storage
container.
5.
Daily Walk-Around Inspection
– Perform as instructed.
6.
Battery –
Charge as required.
7.
Fuel
(Combustion Engine Powered Machines) – Add the
proper fuel as necessary.
8.
Engine Oil Supply
- Ensure the engine oil level is at the Full
mark on the dipstick and the filler cap is secure.
9.
Hydraulic Oil
– Check the hydraulic oil level. Ensure hydrau-
lic oil is added as required.
10.
Accessories/Attachments
- Refer to the Accessories section
in this manual or accessory installed upon the machine for
specific inspection, operation, and maintenance instruc-
tions.
11.
Function Check
– Once the “Walk-Around” Inspection is
complete, perform a functional check of all systems in an
area free of overhead and ground level obstructions. Refer to
Section 4 for more specific operating instructions.
IF THE MACHINE DOES NOT OPERATE PROPERLY, TURN OFF THE MACHINE IMMEDI-
ATELY! REPORT THE PROBLEM TO THE PROPER MAINTENANCE PERSONNEL. DO NOT
OPERATE THE MACHINE UNTIL IT IS DECLARED SAFE FOR OPERATION.
Parent Metal Crack
Weld Crack
To
order go
to
Discount-Equipment.com