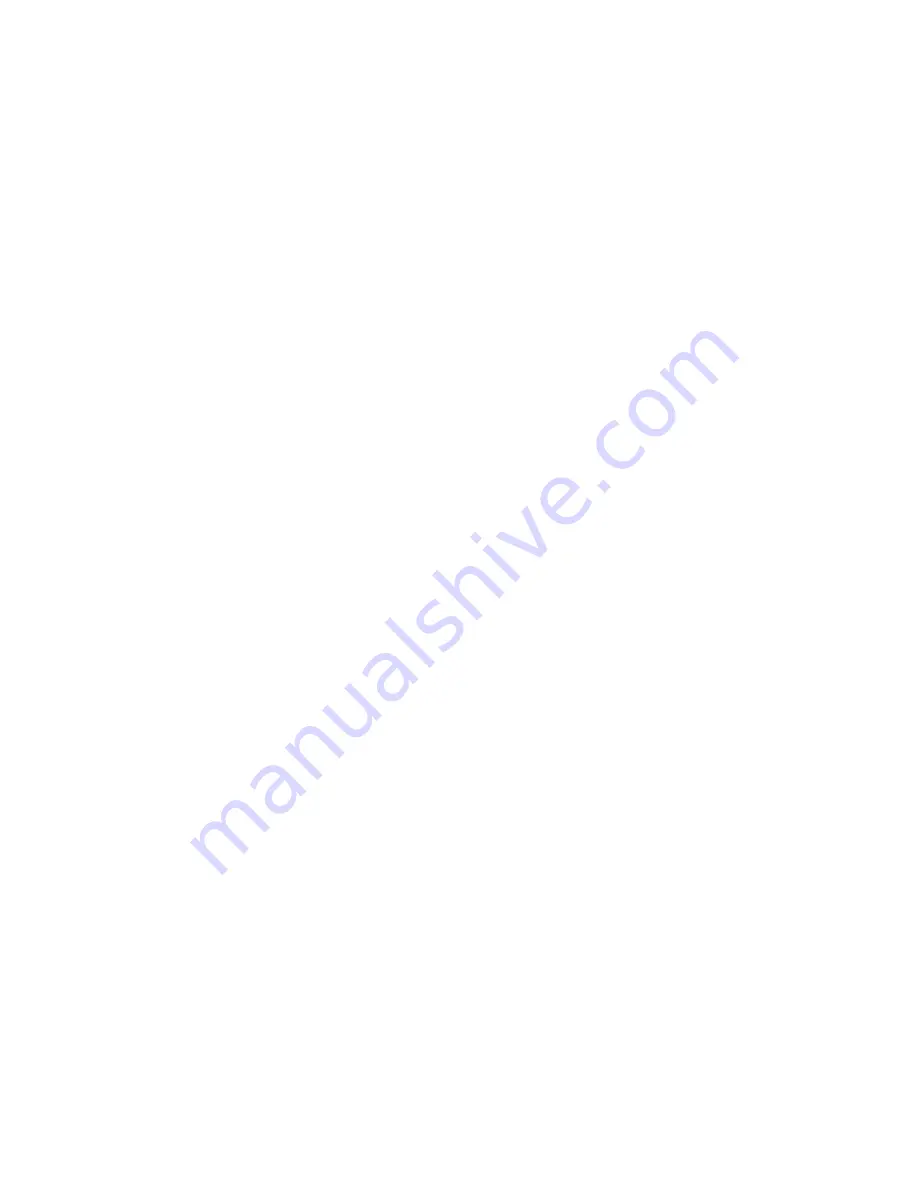
21
you have turned off power at this disconnect before
beginning such procedures.
Once your workpiece is clamped securely and
tooling is installed, you can reestablish power to
machine by turning cut-out panel back ON.
8.18
Coolant control
The flood coolant system is controlled by the
switch on front of drill head (Figure 10). If coolant
has been turned on but does not flow, check pump
rotation by observing pump shaft. It should be
rotating in the direction of arrow on pump casting. If
rotation is incorrect, see Section 6.4
Electrical
Connections,
for more information.
Open valve to coolant nozzle using handle at left of
head (see Figure 10).The proximity of nozzle can
be adjusted by loosening the two knobs and sliding
coolant pipe up or down as needed. Retighten
knobs.
8.19
Spindle motor controls
Power to spindle motor is controlled as follows:
1. The cutout box control lever must be in ON
position.
2. The Emergency Stop switch must be
disengaged (rotate clockwise), and the drill
press power switch pushed ON.
3. The feed levers must be used to move quill
slightly off its seat.
4. The arm/spindle control lever must be
engaged for selected rotation. See Section
8.24
Arm/spindle control lever
.
NOTE:
The limit switch will prevent spindle
rotation when quill is seated. Also, quill must
be off seat before control lever is used – a
safety interlock system prevents spindle
rotation unless quill is off seat before control
lever is used.
8.20
Turning off spindle drive
To turn power OFF on the spindle drive motor do
one of the following:
1. Push power switch OFF,
or...
2. Put arm/spindle control lever in neutral,
or...
3. Push STOP switch,
or...
4. When servicing tooling or other machine
components, put service disconnect lever in
OFF position.
Once STOP switch has been pushed (step 3
above), none of the other switches on the panel
can be used to control power to spindle drive motor
or coolant pump until STOP switch has been reset.
8.21
Resetting STOP switch
When pressed, the red emergency stop button
remains engaged. Turn switch clockwise in
direction of arrow to disengage. The switch is re-
set and the other spindle motor controls can be
used.
8.22
Using load ammeter
An ammeter on the control console is used to
monitor load on spindle drive motor. It is connected
into one of the three power lines which supply main
drive motor.
When drive motor is ON and up to speed, and
there is no tooling being used to drill, tap or bore a
hole, the ammeter should read approximately 2.5
amps. If it exceeds this value there is a problem
internally (such as lack of lubrication in the
gearboxes, bad bearings, etc.). You should turn off
machine and determine the cause of any excessive
free-running load.
Monitor the ammeter during machining operations.
The ammeter should stay below 9 amps of current
draw during machining. You should adjust spindle
speed, feed rate and coolant use to maintain full
load current draw below the 9 amp value.
If current draw exceeds 9 amps, a thermal
overload switch in the electrical control panel will
trip. If this occurs, a licensed electrician should
locate and re-set the thermal switch.
8.23
Tapping operations
1. Determine most efficient tapping speed
(spindle speed) by consulting appropriate
machinist's tables, your tap supplier, coolant
supplier and/or workpiece supplier. (Note that
the figures on the chart on front of drill head
are only approximations of appropriate tapping
speed.)
2. Be certain that power feed lever is in
disengaged
position (all the way to right).
3. Turn on spindle motor. Also, turn on coolant
pump if coolant is being used.
4. Move arm/spindle control lever to
Forward
.
5. Use the feed levers to move tap into its pilot
hole until tap makes its initial thread cut and is
engaged in work piece.
6. Allow tap to "self-feed" into pilot hole until it
has completed its tapping operation.
7. Move arm/spindle control lever to neutral
(center position) and allow spindle to stop
completely.
8. Move arm/spindle control lever to reverse, so
that tap unscrews itself from hole it has just
threaded.
Summary of Contents for J-1600R
Page 11: ...11 General Features and Terminology J 1600R cont Figure 4 Figure 5 ...
Page 16: ...16 7 0 Operating Controls Figure 10 Operating Controls ...
Page 27: ...27 Figure 20 Figure 21 Figure 22 ...
Page 30: ...30 13 2 1 Column and Base Exploded View ...
Page 34: ...34 13 4 1 Gearbox Assembly Upper Section Exploded View ...
Page 37: ...37 13 5 1 Gearbox Assembly Lower Section Exploded View ...
Page 42: ...42 13 6 1 Rear of Head Exploded View ...
Page 47: ...47 13 8 1 Hydraulic Clamping Mechanism Exploded View ...
Page 50: ...50 13 9 1 Hydraulic System Exploded View ...
Page 52: ...52 14 0 Electrical Connections for J 1600R ...