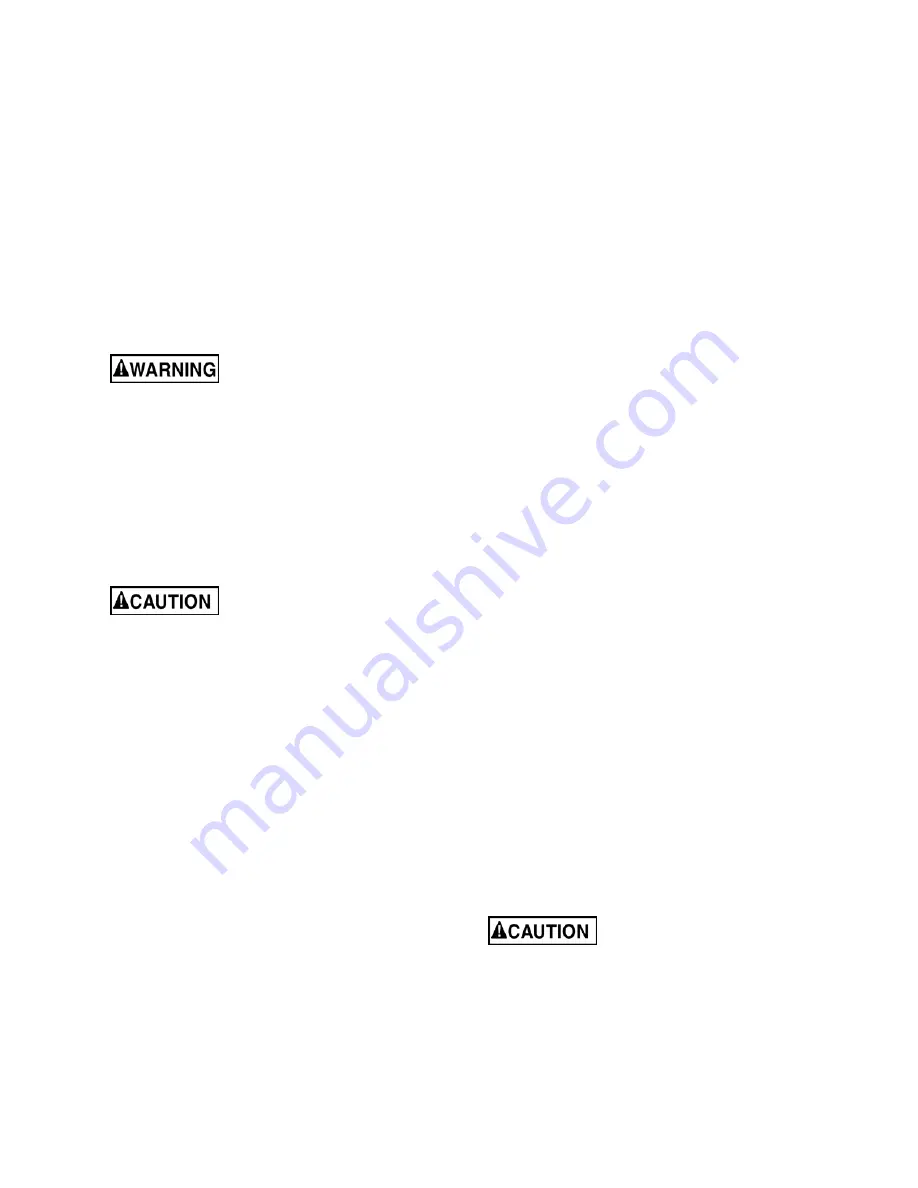
17
8.0
Operation
8.1
Clamping workpieces
To load/unload heavier workpieces, unlock arm
and rotate it out of the way. Lift the workpiece with
slings or other properly rated lifting equipment.
Both the box table and base surface are slotted to
accept a suitably sized T-slot clamp. Before
beginning any work on the drill press, anchor the
work piece, and box table if used, to be certain that
workpiece and/or box table will not move when tool
enters workpiece.
If box table will not be used, simply remove the
nuts at the base, and move table off using proper
lifting equipment.
Failure to properly anchor
workpiece and box table could result in
damage to machine, damage to workpiece, and
severe injury to machine operator. Never work
on drill press without clamping the materials
using a T-slot system set-up.
8.2
Tool insertion
The Model J-1600R uses a No. 5 Morse taper in
the spindle to secure tooling. Any drill, milling
cutter, or tool holder with an MT-5 can be inserted
into the quill.
The first step in removing or
inserting any tooling is to
be absolutely certain
the machine cannot be accidentally started
during the insertion or removal operation.
The
only way to be certain of this fact is to disconnect
power to machine. The service box should have a
cut-out switch or lever on the outside of the box.
Position switch or lever in the OFF position before
inserting or removing tooling.
To insert tooling:
1. Verify that machine is disconnected from
power.
2. Be certain the spindle is clean, free from oil,
and ready to accept the shank of any tooling.
3. Check the shank of tooling to be certain the
tooling is free from dirt, nicks or burrs. If nicks
or burrs are discovered, file or stone the shank
until it is smooth.
4. Pull the tooling ejection handle
out
to be
certain the tooling can be inserted. See Figure
10.
5. Be certain quill is in full UP position.
6. Slide shank of tooling into spindle until it seats.
7. Use a soft-faced mallet (such as lead, plastic,
brass, etc.) to give the tooling a sharp tap on
its tip. This will secure the tooling in the taper.
8. Re-establish power to machine, and the drill is
ready to use.
To remove tooling:
9. Verify that machine is disconnected from
power.
10. Place a wood block under the tooling in
spindle, to prevent it being damaged should it
fall out during the removal process.
11. Use the feed levers to lower quill enough to
allow tooling ejection handle to be pushed fully
inward.
12. While using leather gloves to hold the tooling
and prevent it from falling loosely out of the
spindle taper, use the feed levers to give the
quill a sharp upward stroke against the top of
its travel and the tooling will be released from
the taper in the spindle.
13. Remove tooling and pull tooling ejection
handle
out
to allow new tooling to be inserted.
8.3
Tool positioning over workpiece
After workpiece has been clamped to base or
table, position the tooling over workpiece, using
any or all of the following methods:
1. Adjusting height of arm on support column.
2. Moving drill head along arm.
3. Rotating column upon which arm and head are
attached.
8.4
Unlocking arm and column
mechanisms
A motorized locking system is used to lock the
head to the arm, the arm to the column, and the
column to the base.
The buttons which control the locks are located in
center of drill head handwheel (see
Figure 10).
Press and hold UNLOCK (green) button until arrow
(Figure 11) points to “B”. Release button. Clamping
device is now disengaged. When locking, press
and hold LOCK (red) button until arrow points to
“A”. Clamping device is now re-engaged.
NOTE: When you push UNLOCK,
all
of the locks
are disengaged. When you push LOCK,
all
of the
locks are engaged.
Always be certain the locks
are engaged before using drill press. Pull on
arm handle and try to rotate handwheel at front
of head, before starting spindle. Failure to have
all locks secure may result in damage to
tooling, damage to workpiece, and possible
injury to operator.
Summary of Contents for J-1600R
Page 11: ...11 General Features and Terminology J 1600R cont Figure 4 Figure 5 ...
Page 16: ...16 7 0 Operating Controls Figure 10 Operating Controls ...
Page 27: ...27 Figure 20 Figure 21 Figure 22 ...
Page 30: ...30 13 2 1 Column and Base Exploded View ...
Page 34: ...34 13 4 1 Gearbox Assembly Upper Section Exploded View ...
Page 37: ...37 13 5 1 Gearbox Assembly Lower Section Exploded View ...
Page 42: ...42 13 6 1 Rear of Head Exploded View ...
Page 47: ...47 13 8 1 Hydraulic Clamping Mechanism Exploded View ...
Page 50: ...50 13 9 1 Hydraulic System Exploded View ...
Page 52: ...52 14 0 Electrical Connections for J 1600R ...