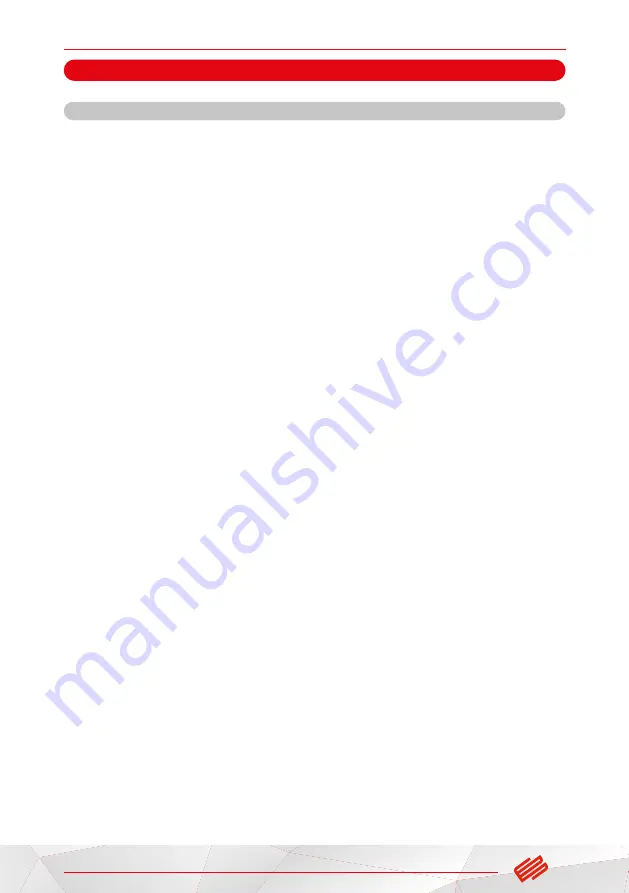
24
© JBG-HT (v.2.0)
INSTRUCTION MANUAL
– HEAT PUMP
4. SAFE TRANSPORTATION, INSTALLATION AND STORAGE
4.1. General Guidelines
1 ) Installation activities must be carried out only by qualified installers with appropriate authorizations
(heating installers, sanitary installers, refrigeration technicians (in case of interference with the refriger-
ation system). Otherwise, there may be a danger to health and life.
2 ) The staff is obliged to act in accordance with the applicable rules of occupational health and safety.
3 ) Electronic and electrical work may be performed only by authorized personnel.
4 ) Service work can only be carried out through the pump manufacturer’s service team or external
service on behalf of the manufacturer. Otherwise, you risk losing the warranty.
5 ) Note that the air for the heat pump is drawn from the rear of the unit, while it is blown out by the unit’s
fans. This implies the need to exercise every care in the correct positioning of the outdoor unit outside
the building.
6 ) Follow the distances shown in Table 9 to ensure sufficient airflow and allow for maintenance work.
7 ) Make sure there is enough space for the installation of heating cables.
8 ) The heat pump is suitable for both ground mounting. Installation on a flat roof is possible, but check the
current building and ceiling strength regulations. Adequate condensate drainage must be provided.
Do not install the product on wooden-framed buildings and lightweight roofs. Installation on a sloping
roof is not allowed.
9 ) The air temperature at the outlet is about 5°C lower than the ambient temperature. Therefore, under
certain weather conditions, this can cause ice formation. Therefore, do not choose a location where
the air outlet is near sidewalks, paving surfaces and drain pipes. Keep the heat pump at an appropriate
distance from the ground.
10 ) Do not expose the outdoor unit to polluted, dusty and corrosive air.
11 ) Maintain clearance from vents.
12 ) Maintain distance from trees. Leaves can contaminate the heat exchanger of the heat pump and cause
it to stop or be damaged.
13 ) Pay attention to noise emissions. Choose a place that is easily accessible from the point of view of
carrying out maintenance work.
14 ) Avoid sucking in the air blowing out of the heat pump outlet.
15 ) Ensure that water does not collect on the ground, water must penetrate into the ground without
obstruction.
16 ) Choose a place where large amounts of snow do not accumulate in winter. If this is not possible,
remove snow regularly from the air inlet/outlet grille and around the product.
17 ) Choose a location where high winds do not affect the heat pump, especially the air intake. If possible,
position the unit transverse to the main wind direction.
18 ) Safety area:
Due to the fact that the product contains R290 refrigerant. The installation site must be at least 1m
away from potential ignition sources: electrical switches, lighting switches and lighting.
Summary of Contents for ZHHS-01-10K-R290-V5-M
Page 2: ......