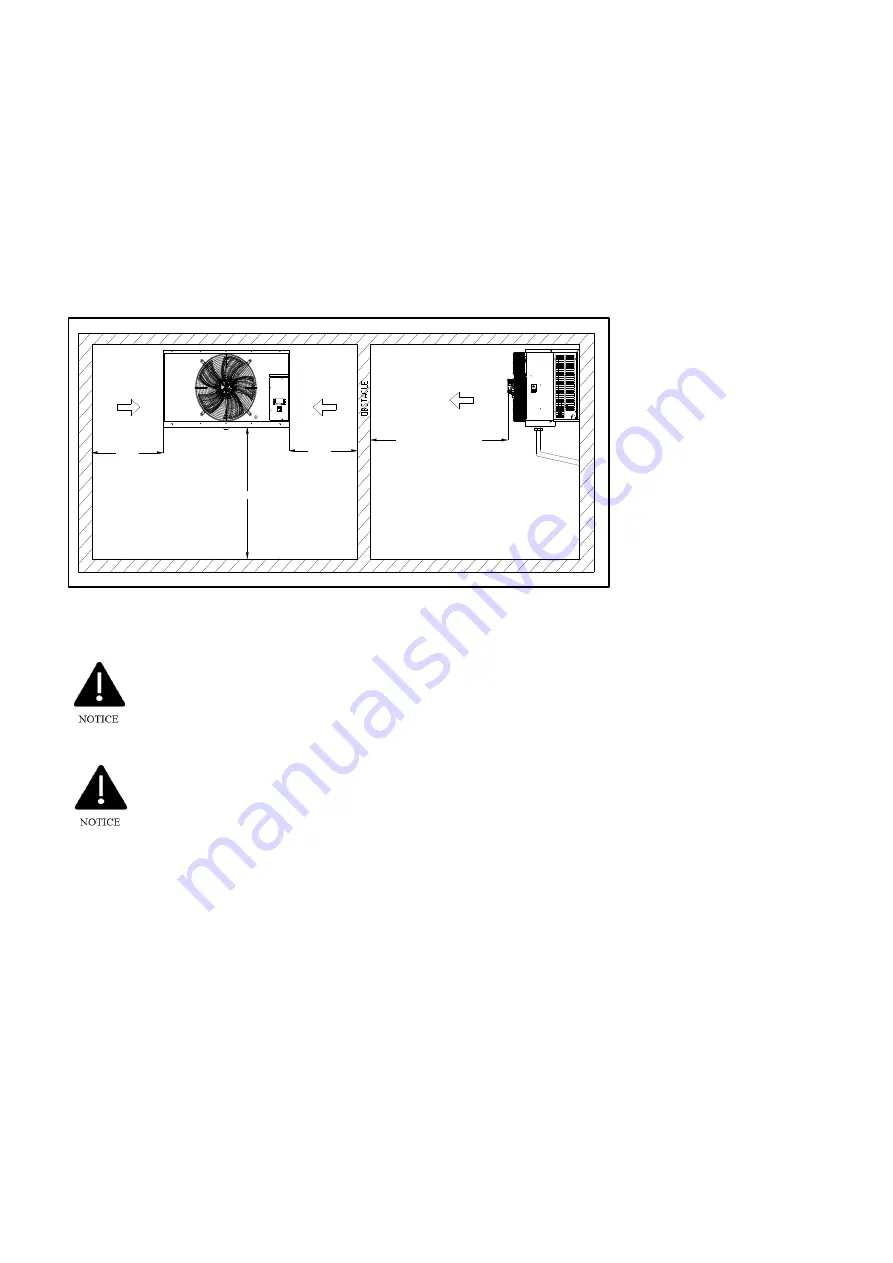
Issue: 01.06.2023
Page 5
Indoor
•
The indoor units can be mounted directly to a wall or to
the ceiling utilizing the fixing holes on the rear of the
unit or on the top of the unit. No additional brackets
are required.
•
A minimum 10mm rawl bolt type fixing is required with
a large steel washer to bear the indoor unit weight. It
is important to ensure that the wall/ceiling can
withstand the unit weight and that all fixings are
secure.
•
Position the indoor unit where the optimum airflow can
be achieved. Avoid locating in corners or in alcoves
which may restrict airflows.
•
Avoid mounting indoor directly over door openings. It is
recommended to locate the indoor opposite door
openings to reduce infiltration and the amount of
warm, humid air drawn into the cold room. Also, to
locate indoors so that the distance to the opposite wall
does not exceed the unit's rated air throw distance.
•
The installation location should allow sufficient space
for air flow and maintenance around the units. Refer
Figure 5
.
•
Twin systems, both evaporators need to be in the
same room/controlled space. It is not possible to put
evaporators in separate rooms.
Figure 5: Installation Clearance (Indoor Unit)
Field Piping
Line sizing should be done according to
section: Pipe Sizing. Correct line sizing will
minimize the pressure drop and maintain
sufficient gas velocity for proper oil return.
All applicable standards must be observed in
the installation of refrigerant piping.
The system should be installed to utilize a
pump down configuration.
To ensure satisfactory operation and performance, the
following points should be noted:
•
Pipework routes must be as simple and as short as
possible.
•
Use of incorrect pipe sizes can affect system
pressures/temperatures and gas velocity for proper oil
return.
•
Use only clean, dehydrated refrigeration grade
copper tube with long radius bends.
•
When brazing use brazing filler alloys containing
phosphorus such as BCuP-7 without flux for joining
copper tubes.
•
Run braze without over filling to ensure there is no
leakage into the tube.
•
To prevent oxidation, blow oxygen free nitrogen
through pipework when brazing.
•
Protect the casing of the unit when brazing connections.
•
To prevent condensation on pipe surface, install
insulation with a minimum wall thickness 1/2
”
on all
suction lines and on all pipes penetrating walls or
passing through hot areas.
•
Adequately support all pipe work at a maximum of 2-
meter intervals.
•
Pump down control is done by adding solenoid valve
along the liquid line. By closing a liquid line solenoid
valve, the refrigerant can be pumped into the
condenser and receiver, and the compressor operation
controlled by means of a low-pressure control. The
refrigerant can thus be isolated during periods when
the compressor is not in operation, and migration of
refrigerant to the compressor crankcase is prevented.
Therefore, there is no need for any interconnecting
wiring between the evaporator and condensing unit.
•
Avoid low points on pipework where oil can
accumulate.
•
Suction gas velocity must be more than 4m/s for
horizontal pipe and 8~12m/s for vertical pipe, to
ensure good oil return.
•
For the outdoor unit located above the indoor unit, the
use of U-trap and double suction risers is often
required. These suction risers must always be fitted with
a U-trap at the bottom and a P-trap at the top and
never be higher than 4m unless a second U-trap system
is fitted (
Figure 6
).
•
Liquid lines should be sized to ensure a full supply of
liquid refrigerant to the expansion device.
•
For the outdoor unit located below the indoor unit,
attention should be paid to the sizing of liquid lines on
vertical riser by limiting the maximum rise to 6m (
Figure
7
).
•
For the outdoor unit located below indoor unit: Inverted
P-trap is necessary when pump down is not used. To
prevent refrigerant from draining into the compressor
during off-cycle (
Figure 7
).
AIR
INLET
AIR
INLET
Min. 1.8m from floor
OBSTA
CLE
FLOOR
AIR
THROWN
Min. 1.5m from
any obstacle
0.5m
0.5m
WALL
Summary of Contents for CellarPlus 70-S1/S3
Page 26: ...Issue 01 06 2023 Page 23 Figure 30 Declaration of Conformity Outdoor ...
Page 27: ...Issue 01 06 2023 Page 24 Figure 31 Declaration of Incorporation Indoor ...
Page 28: ...Issue 01 06 2023 Page 25 Figure 32 Declaration of Incorporation Outdoor ...
Page 29: ...Issue 01 06 2023 Page 26 Figure 33 EU Declaration of Conformity Outdoor ...
Page 30: ...Issue 01 06 2023 Page 27 Figure 34 EU Declaration of Incorporation Indoor ...
Page 31: ...Issue 01 06 2023 Page 28 Figure 35 EU Declaration of Incorporation Outdoor ...