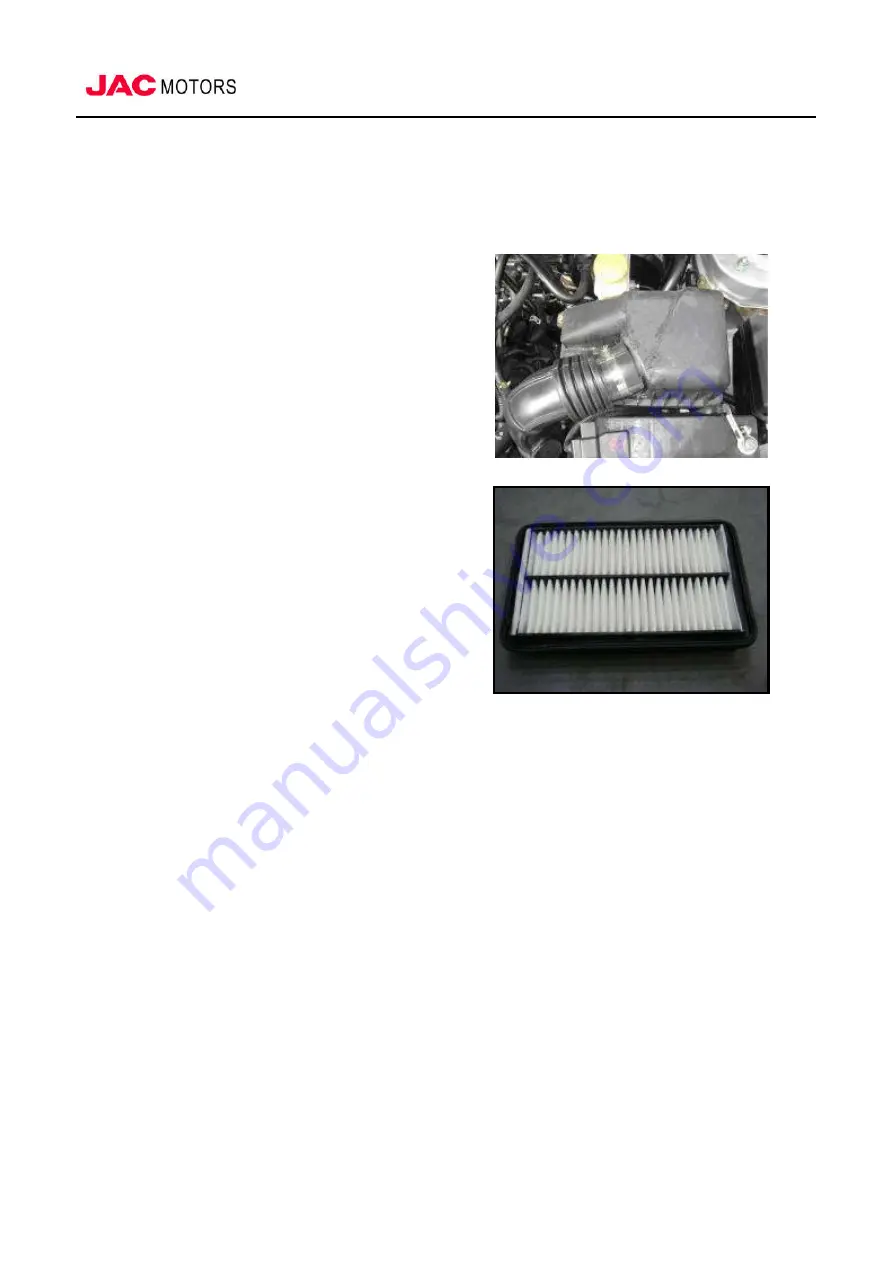
江淮汽车 部门:客户服务部
Mechanical Part of
Engine
Attention:
■
Properly mount every joint and tighten the clamp.
3.
Replacement of Air Filter element
1)
Dismantlement
①
Loosen the locking bolt on upper cover of air
filter and lift the upper cover.
②
Dismount air filter element.
2)
Check after Dismantlement
■
Periodically clean or replace the filter element with recommended period. See “Periodical
Maintenance”.
■
Blow the filter element from its back side with compressed air, till nothing is blown off.
3)
Installation
■
Install with steps contrary to dismantlement.
VI. Intake Manifold and Exhaust Manifold
Fig. 1.1.016
Fig.1.1.015