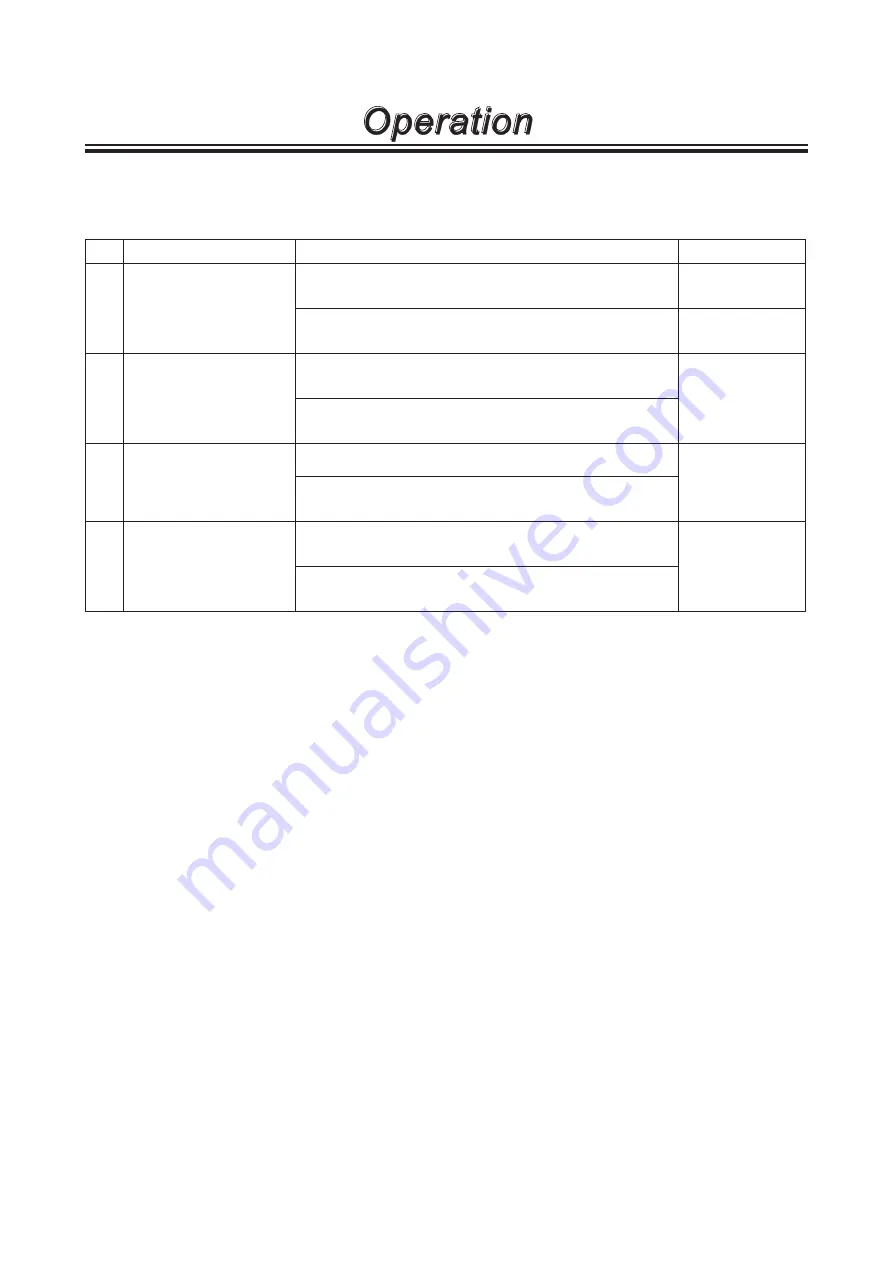
- 16 -
Operation
■ Daily inspection
See the following check items in operation. On detection of abnormality, stop operation immediately. Take
measures referring to the item "Trouble shooting".
No.
States
Points to be checked
How to check
1
Pumping
• If liquid is pumped.
Flow meter or
visual inspection
• If discharge pressure/ suction pressure is normal.
Check specifica-
tion.
2
Noise and vibration
• If abnormal noise or vibration occurs. They are signs
of abnormal operation.
Visual or audio
inspection
• Place a rubber plate beneath the pump base to reduce
noise or oscillation as necessary.
3
Air ingress from pump
head joints and a suc-
tion line
• If leakage occurs.
Visual inspection
• If pumped liquid includes air bubbles, check lines for
leakage and retighten as necessary.
4
High surface tempera-
ture of the pump and the
motor
• Pump surface temperature gets higher along with liq-
uid temperature.
Touch or use a
thermometer
• Motor surface temperature should be 40ºC higher than
ambient temperature, or below.
Summary of Contents for Hicera V Series
Page 7: ...5 Outline 1 Unpacking Inspection 6 2 Product outline 6 3 Model code 7 4 Specification 8...
Page 11: ...9 Installation 1 Before installation 10 2 Installation Piping Wiring 12...
Page 16: ...14 Operation 1 Operation 15...
Page 19: ...17 Maintenance 1 Disassembly Assembly 18 2 Troubleshooting 24 3 Dimensions 25 4 Wear parts 27...
Page 30: ...28...
Page 31: ...29...