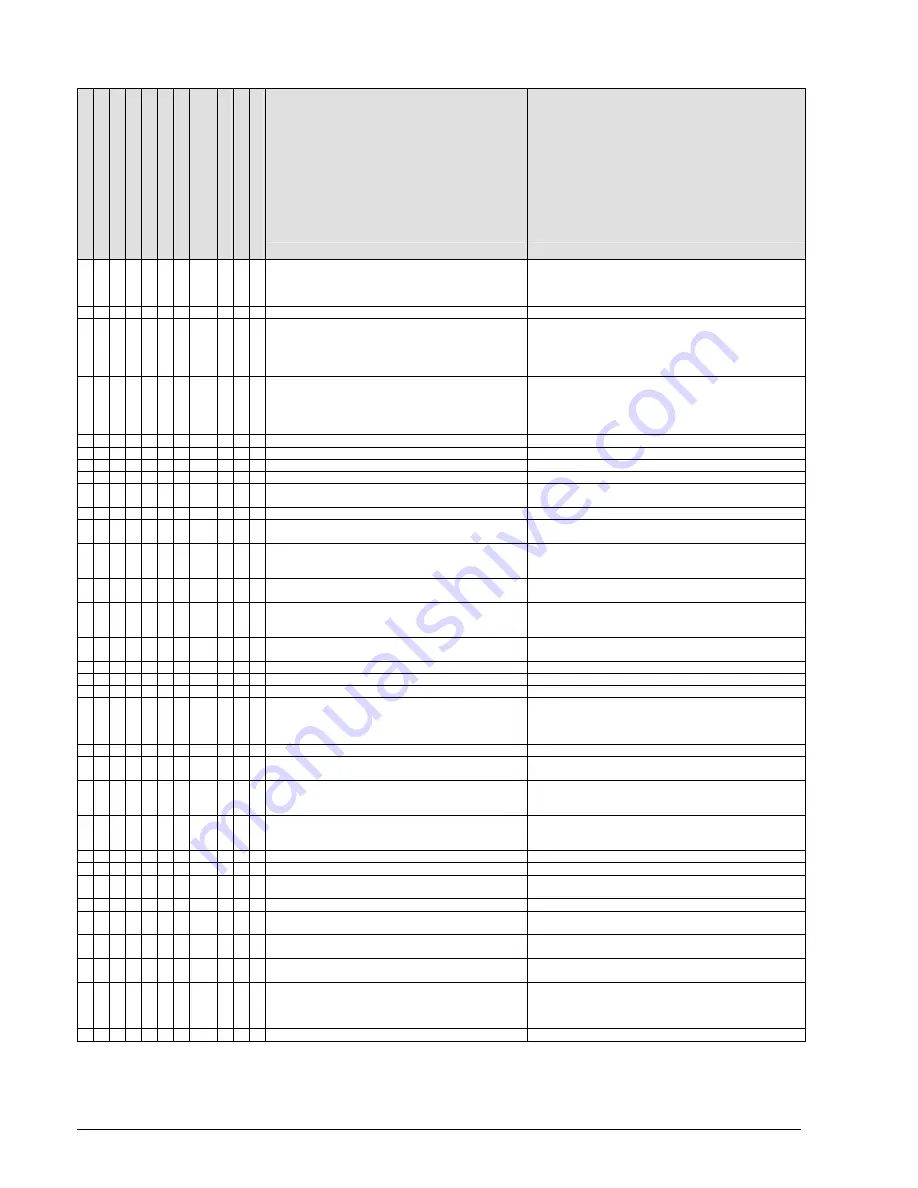
Installation, Operating and Maintenance Instruction
Model LSN
LSN 100-english
page 20
Revision 00
Article No 4264611
Issue
05/2003
D
is
ch
ar
ge
to
o
lo
w
D
is
ch
ar
ge
s
to
ps
a
fte
r
a
tim
e
H
ea
d
to
o
lo
w
H
ea
d
to
o
hi
gh
D
riv
e
m
ec
ha
ni
sm
o
ve
rlo
ad
ed
P
um
p
no
t r
un
ni
ng
q
ui
et
ly
T
em
pe
ra
tu
re
in
p
um
p
to
o
hi
gh
T
em
pe
ra
tu
re
in
s
ha
ft
se
al
in
g
to
o
hi
gh
T
em
pe
ra
tu
re
a
t t
he
b
ea
rin
g
to
o
hi
gh
P
um
p
le
ak
in
g
Le
ak
ag
e
ra
te
a
t s
ha
ft
se
al
in
g
to
o
hi
gh
Cause
Solution
■
Back-pressure too high
check facility for pollution, open discharge valve
reduce resistance in discharge pipe (e.g. clean filter if
necessary)
use larger impeller (note available motor power)
■
■
■
Back-pressure too low, discharge too low
throttle discharge valve
■
■
Speed too high
reduce speed
compare speed of motor with specified pump speed (rating
plate)
when adjusting speed (frequency transformer) check refer-
ence value setting
■
■
Speed too low
increase speed (check available motor power)
compare speed of motor with specified pump speed (rating
plate)
when adjusting speed (frequency transformer) check reference
value settings
■
■
■
■
Flow too little
increase min. flow (open discharge valve, bypass)
■
Flow too big
reduce flow (throttle discharge valve)
■
■
Impeller diameter too big
use smaller impeller
■
■
Impeller diameter too small
use larger impeller (check available motor power)
■
■
■
■
Pump and/or pipes not completely filled with liquid
fill
vent
■
■
■
Pump or suction/intake pipe blocked
clean
■
■
Air pocket in pipeline
vent
improve course of pipe
■
■
■
■
■
Suction height too big / NPSH of system too small
increase liquid level and admission pressure
reduce resistance in the intake/suction pipe (change course
and rated width, open shut-off valves, clean filters)
■
■
■
Air being sucked in
increase liquid level
check if suction pipe is vacuum-tight
■
■
■
Air being sucked in through shaft sealing
clean sealing pipe
increase sealing pressure
replace shaft sealing
■
■
Direction of rotation is wrong
swap over two phases of power supply (to be done by an
electrician)
■
■
■
■
Inner components suffering from wear
replace worn parts
■
■
■
Density and/or viscosity of liquid handled is too high
seek assistance
■
■
Stuffing box not straight
tighten evenly
■
Stuffing box is fastened too tight resp. shaft sealing is worn loosen stuffing box
replace packing and/or mechanical seal
check sealing, flushing and cooling pipes (pressure)
avoid dry running
■
■
Lines and roughness on shaft or shaft sleeve
replace parts
■
■
Unsuitable packing material
use suitable material (check shaft or shaft sleeve for damage
beforehand)
■
■
Deposits on mechanical seal
clean
replace mechanical seal if necessary
if necessary provide additional rinsing or quench
■
■
Impeller out of balance
remove blocks/deposits
replace impeller if broken or unevenly worn
check shafts to ensure that they are running true
■
■
■
Coupling not aligned
align pump unit better
■
■
Coupling distance too small
change
■
■
■
■
■
Forces in pipeline too high (pump unit under strain)
change (support pipes, use compensators, etc.)
is foundation plate/frame properly cast in place?
■
Too much, too little or the wrong type of lubricant
change
■
Electricity supply not right (2-phase running)
check voltage of all phases
check cable connections and fuses
■
Sealing insufficient
tighten screws
replace sealing
■
■
Bearing damaged
replace
check lubricant and bearing space for pollutants (rinse oil area)
■
Relief fittings insufficient
clean relief openings in impeller
replace worn parts (impeller, split rings)
adjust in line with the system pressure/intake pressure given on
ordering
■
System-related vibrations (resonance)
seek assistance