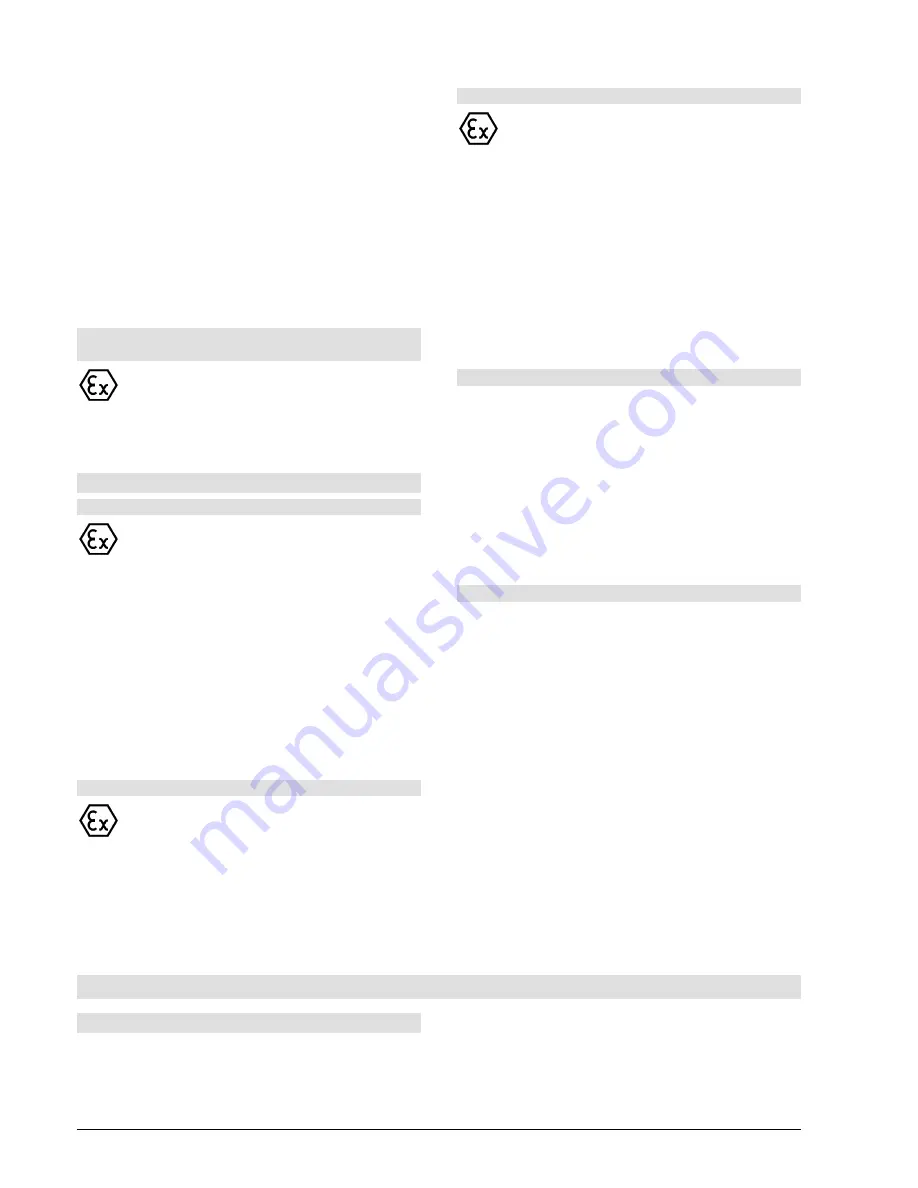
Installation, Operating and Maintenance Instruction
Model LSN
LSN 100-english
page 6
Revision 00
Article No 4264611
Issue
05/2003
Example: Function of bearings. Operation and
application conditions are essentially responsible for
their achievable life cycle.
By regular control of the lubricant and the running
sound the danger of occurring over temperatures by
bearings running hot or defect bearing seals is
avoided. Refer to chapter 6.6 and 7.4.
The function of the shaft sealing must be secured by
regular control.
If auxiliary systems (e.g. external flushing, cooling,
heating) are installiert, it must be checked, if
monitoring devices are necessary to secure the
function.
2.7.7 Electric switches and control device,
Instrumentation and accessories
Electric
switches
and
control
devices,
instrumentation and accessories like e.g. flush
tanks, a.s.o., must correspond with the valid
safety requirements and regulations for
explosion protection.
2.8 Use acc. to Regulations
2.8.1 Speed, Pressure, Temperature
Suitable safety measures must be taken at the
plant to ensure that the speed, pressure and
temperature of the pump and the shaft sealing
do not exceed the limit values given in the data
sheet and / or order confirmation. The given
admission pressures (system pressures) must
also be sufficiently high.
Further, pressure shocks, as can occur on too fast
shut down of the facility, must be kept away from the
pump (e.g. by non-return valve at pressure side, fly
wheel, airtanks). Quick temperature changes must be
avoided. They could cause a temperature shock and
lead to damage or impair the function of single
components.
2.8.2 Permitted Nozzle Loads and Torques
Basically the suction and discharge piping must
be designed in such way, that as little forces as
possible are effective to the pump. If that is not
possible, the values shown in chapter 3.5 must
not be exceeded under any circumstances. This
is valid for the operation as well as for the
standstill of the pump and therefore for all
possible pressures and temperatures of the
unit.
2.8.3 NPSH
The pumped liquid must have a min. pressure
NPSH at the impeller inlet, so that cavitation
free work is secured resp. a "break off" of the
pump flow is prevented. This condition is
fulfilled, when NPSH-value of the system
(NPSHA) lies above NPSH-value of the pump
(NPSHR) under all operating conditions.
Attentention must especially be piad to the NPSH-
value on pumping liquids near the vapour pressure. If
the NPSH-value of the pump remains under, this can
lead from damage of the material due to cavitation to
destruction by overheating.
The NPSH-value of the pump (NPSHR) is shown in
the curves of every pump type.
2.8.4 Sealing, Flushing, Cooling
Suitable provisions for the regulation and monitoring of
sealing, flushing or cooling are to be provided.
When handling dangerous liquids or if temperatures
are high, care should be taken to ensure that the
pump ceases operating if the sealing, flushing or
cooling system fails.
Sealing, flushing and cooling systems must always be
operational before the pump is started up. They
should not be taken out of operation until the pump
has stopped, provided that the nature of the operation
allows this at all.
2.8.5 Back Flow
In systems where pumps are operating in closed
circuits under pressure (gas cushions, steam
pressure), the pressure of the gas cushion must not
be reduced via the pump, since the back flow speed
may be much higher than the operating speed, which
would destroy the unit.
3. Description
3.1 Design
LSN-pumps
are single-stage volute casing pumps in
process design. Hydraulic design and dimensions
comply with ISO 2858/ EN 22858, the technical design
complies with ISO 5199/EN 25199.
LSNI-pumps
as design LSN, except that they have an
inducer.
LSNH- and LSNIH-pumps
pumps additionally
possess a cooling or heating of the casing cover
and/or the volute casing.