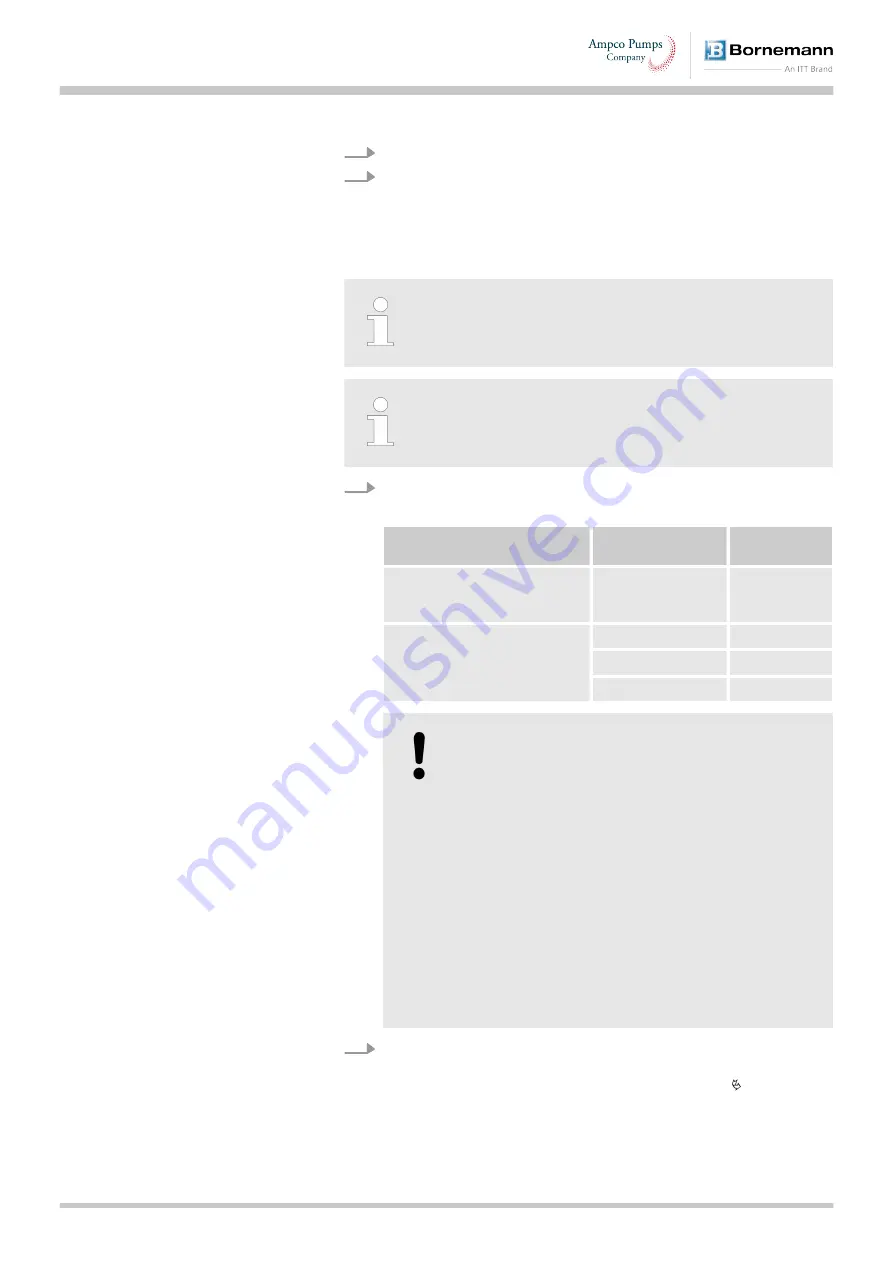
5.
Discharge flammable and potentially explosive pumped media safely.
6.
Ensure that the pressure level in the safe area guarantees pressure relief
via the safety device.
5.6.6 Including safety and control equipment
A filter in the inlet line is also recommended during ongoing opera-
tion.
If necessary, due to the conveyed medium, the size of the filter
mesh can be increased or omit the filter altogether. Hard solids must
then be prevented by appropriate measures.
1.
Incorporate filter into the inlet line, in accordance with the following table:
Filter for inlet line – mesh size per operating phase
Operating phase
Pump size
Mesh size
[mm]
Start-up phase with initial com-
missioning, after maintenance
work, etc.
All
1
Ongoing operation
10xx
2 – 5
20xx
2 – 5
30xx
2 – 5
NOTICE!
Pump damage due to unsuitable filter!
–
The use of an unsuitable filter can affect the pumping
capacity of the pump and may lead to cavitation and
damage to the pump.
–
The filter with 1 mm mesh size is only used during com-
missioning and the start-up phase. This filter is unsuitable
for use during operation because the mesh size is too
small.
–
After starting up, clean the filter and replace the filter
insert. When doing so, observe the mesh size data
(
).
–
Regularly check the filter insert and filter housing for con-
tamination and clean:
–
For prevention at least once every six months.
–
In the event of high solid content levels as necessary
at shorter intervals.
2.
In order to monitor the contamination include differential pressure moni-
toring:
n
Observe permissible differential pressure of the filter (
Manufactur-
er's instructions).
Avoiding contamination
Installation and connection
40
Type SLH-4U
0
3
/20
20
JP Rev. 1