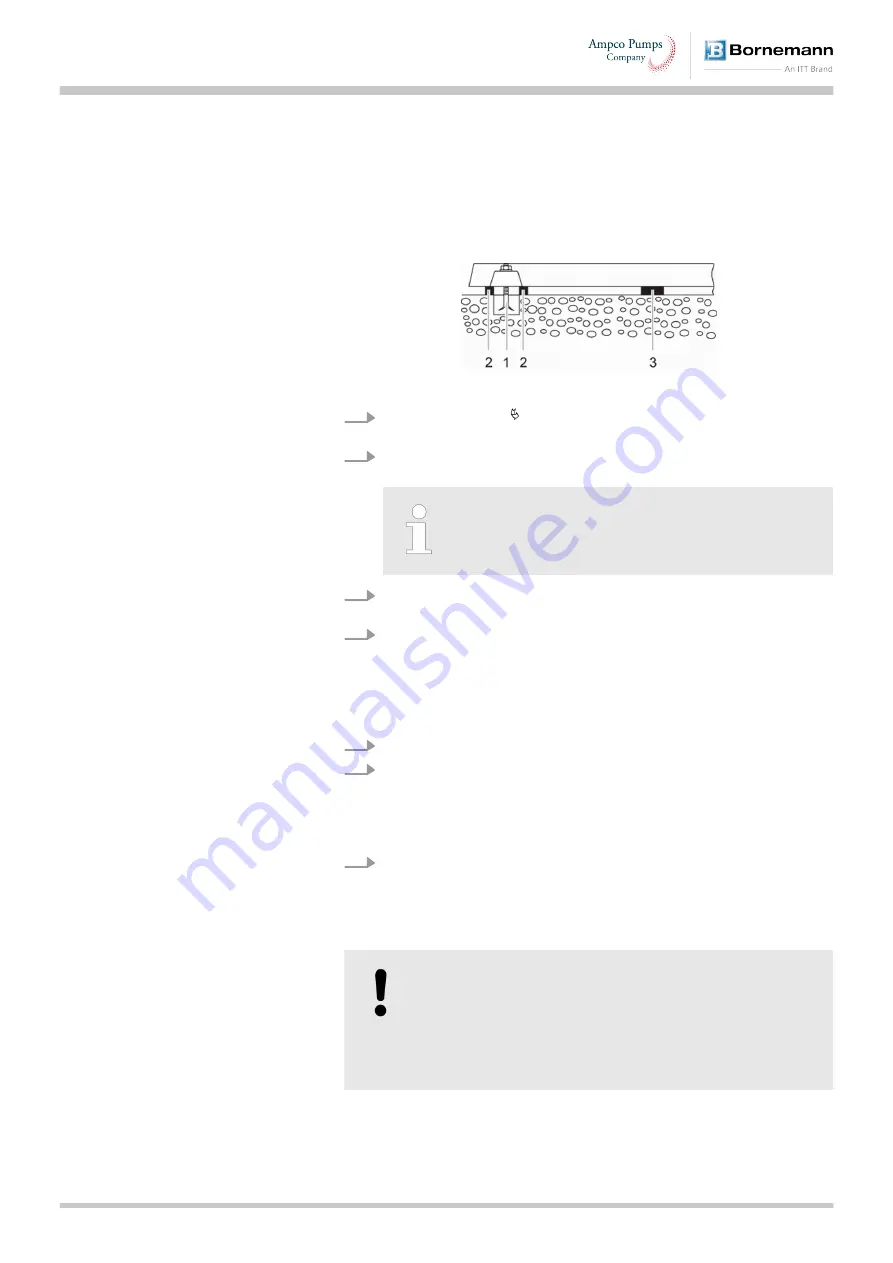
5.3.1 Placing the pump unit on the foundation
Special tool:
n
Spirit level
Materials:
n
Foundation bolts
n
Steel fixtures
n
Casting mortar, non-shrinking
Fig. 7: Installation on a foundation (schematic diagram)
1.
Lift pump assembly (
pump system operating instructions and
Chapter 4.1 ‘Transportation’ on page 21
).
2.
Hook in the foundation bolts (1) into the base plate fastening holes from
below.
When using adhesive anchors: Observe the manufacturer's
instructions.
3.
Place the pump unit on the foundation. When doing so, sink the foundation
bolts (1) into the prepared anchor holes.
4.
Using steel fixtures, align the pump unit in accordance with the height and
system dimensions as follows:
n
Place a steel fixture (2) to the left and right of each foundation bolt (1)
respectively.
n
If the distance from the anchor holes is greater than 750 mm, locate
additional steel fixtures (3) centrally on either side of the base plate.
5.
Ensure that the base plate and steel fixtures lie flush.
6.
Using a digital spirit level (laser alignment device), check in longitudinal
and transverse directions:
n
Permissible height deviation (
Chapter 5.3.2 ‘Aligning the base plate’
, dimensional drawings, pump system operating instruc-
tions).
7.
Repeat the process until the base plate is correctly aligned.
5.3.2 Aligning the base plate
NOTICE!
Property damage due to base plate tension!
–
A tensioned base plate may prevent coupling alignment and
result in pump damage.
–
Base plate on level foundation only and fasten as follows.
–
It is essential to observe the alignment tolerances.
Installation and connection
30
Type SLH-4U
0
3
/20
20
JP Rev. 1