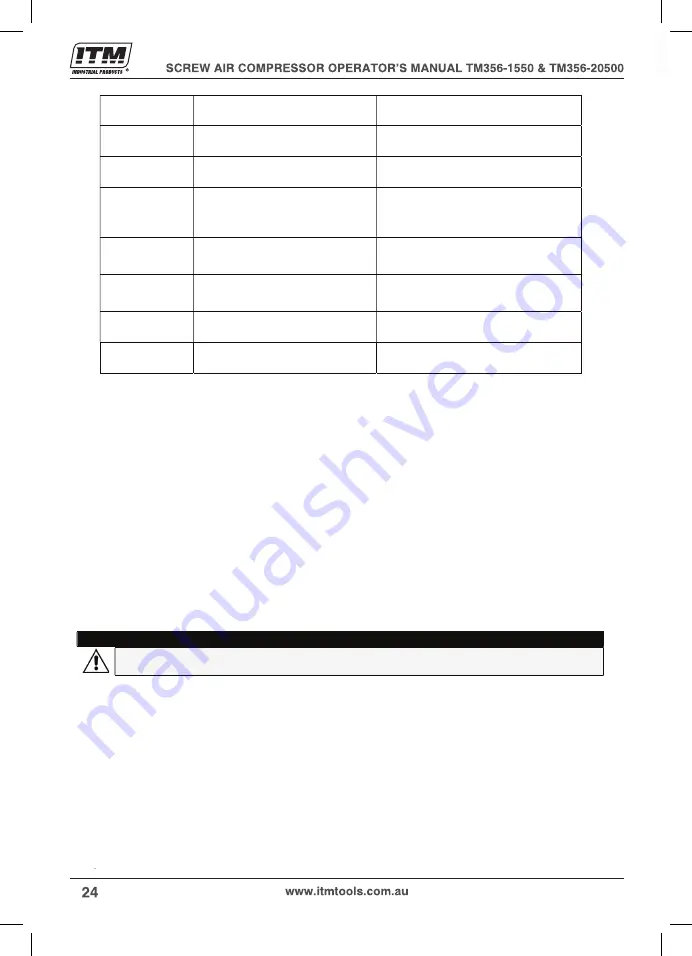
English
25
Code 1625186897- Edition 7/2019
mechanical failure or wrong set data
etc.
Short Circuit
Wrong Wiring, Incorrect Data
setting etc.
Checking the wiring and set the data
correctly
Wrong Phase
Sequence
Reversed Phase sequence or
phase off
Check the wiring
Overload or
Rotor locking
during starting
process
Host start time set to a value less
than the star - delta time delay
Reset the host starting time to be longer
than star-delta delay + Load delay time
Main Contactor
activate time to
time
The emergency button loose
Check the wiring
Air Exhaust
Temperature too
high
Bad Ventilation, Low Oil etc.
Check the vent condition and Oil level
etc.
Temperature
Sensor Failure
Cable off or PT1OO damaged
Checking the wiring and PT100
Over Pressure
The pressure too high or the
pressure sensor failure
Check the pressure and the pressure
sensor
14.2.5 Maintenance Alarm
We have set an alarm to remind for ordinary maintenance.
When reaching the maintenance cycle, the corresponding maintenance alarms will appear on the
display. After the implementation of maintenance related to the content, the controller has to be reset
Process as follows:
Starting from the main screen (see main menu):
1. Press the down button until the "user parameter" menu.
2. Press the right button to activate the submenus of the user menu
3. Press the down button to"maintenance timer reset" for
Oil Filter, Oil/Air Filter, Air Filter, Lube, Grease, Belt
4. Select Parameter & re-set to 0000.
5. Confirm the Reset.
Note: Check (15.2) MAINTENANCE SCHEDULE for componets to be changed at respective service
interval.
15.0 MAINTENANCE
BEFORE CARRYING OUT ANY MAINTENANCE JOBS IT IS OBLIGATORY TO STOP THE
MACHINE AND DISCONNECT IT FROM THE POWER MAINS.
The
maintenance jobs described in this chapter may be carried out by the user.
The more complex
maintenance jobs require professionally skilled personnel to carry out.
15.1 GENERAL INFORMATION
Routine maintenance must be carried out according to the maintenance schedule displayed on the
machine.
15.2 DRAINING CONDENSATE FROM THE OIL TANK
If the compressor work cycle contemplates long pauses during which the machine cools down, a certain
amount of condensate may collect in the oil tank. This happens, for example, when stopping overnight
or at weekends.
The condensate must be drained off every 50 hours or every week. This operation may be performed
only when the machine is cold, that is when it has been switched off for at least 8 hours.