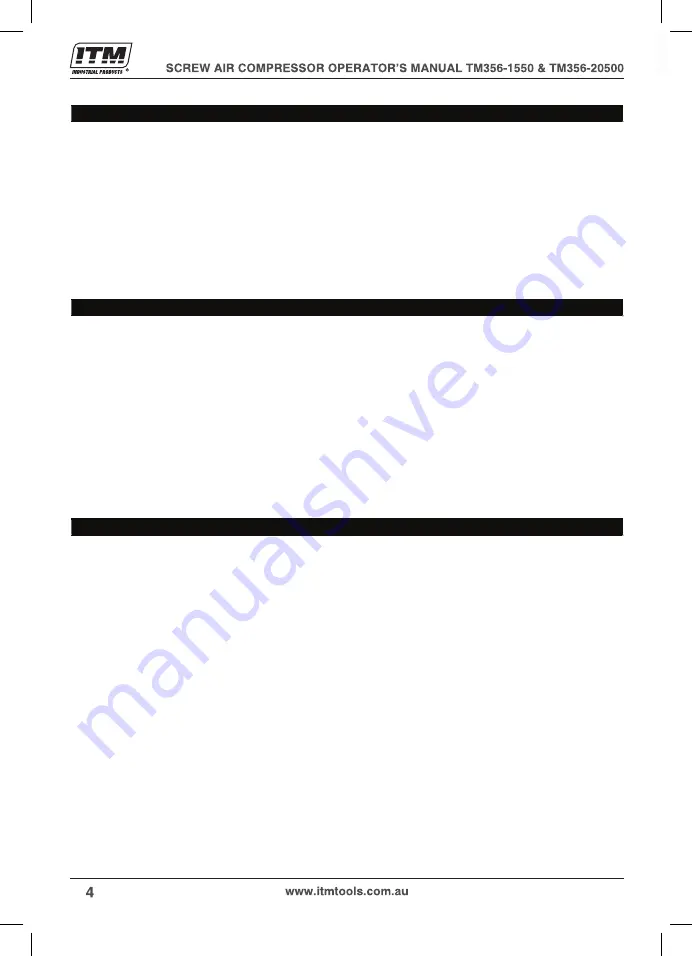
English
5
Code 1625186897- Edition 7/2019
1.0 GENERAL CHARACTERISTICS
The compressor units use single-stage screw rotary air compressors with oil injection.
The central unit comprises:
compressor; oil separator; oil cooler and output air cooler; fan; electric start; safety and regulation devices;
instrument panel.
The system is self-bearing and does not require bolts or other devices to anchor it to the floor.
The unit is completely assembled in the factory; the necessary connections for setting it up are:
connection to the power mains (see installation chapter)
connection to the compressed air network (see installation chapter)
The compressor-motor unit is fitted on the machine chassis by means of flexible supports: this allows
the compressor unit to be laid directly on the floor without any need of further vibration-damping
systems.
2.0 INTENDED USE
The compressor has been built to supply compressed air for industrial use.
The machine cannot be used in premises where there is a risk of fire or explosion or where work is
carried out which releases substances into the environment which are dangerous with regard to safety
(for example: solvents, inflammable vapours, alcohol, etc.).
In particular the appliance cannot be used to produce air to be breathed by humans or used on direct
contact with foodstuffs. These uses are allowed if the compressed air produced is filtered by means of
a suitable filtering system as per the applicable standards.
(Consult the manufacturer for these special uses.)
This appliance must be used only for the purpose for which it was specifically designed.
All other uses are to be considered incorrect and therefore unreasonable.
The Manufacturer cannot be held responsible for any damage resulting from improper, incorrect or
unreasonable use.
3.0 OPERATION
The electric motor and the compressor unit are coupled by means of a belt transmission.
The compressor unit takes in the outside air through the suction valve. The air taken in is filtered by
panel pre-filter fitted one the panel of the external covering and by the filter cartridge fitted upstream
from the suction valve. Inside the compressor unit, the air and the lubricating oil are compressed and
sent to the oil separating filter where the oil is separated from the compressed air; the air is then filtered
again by the oil separating cartridge to reduce the amount of suspended oil particles to a minimum. At
this point the two flows (of oil and air) are sent to two separate coolers where they are cooled, using a
flow of air taken from the environment by a special fan inside the machine.
The cooled oil returns to the circuit while the compressed air is sent to the using network.
Refer to figure 2.