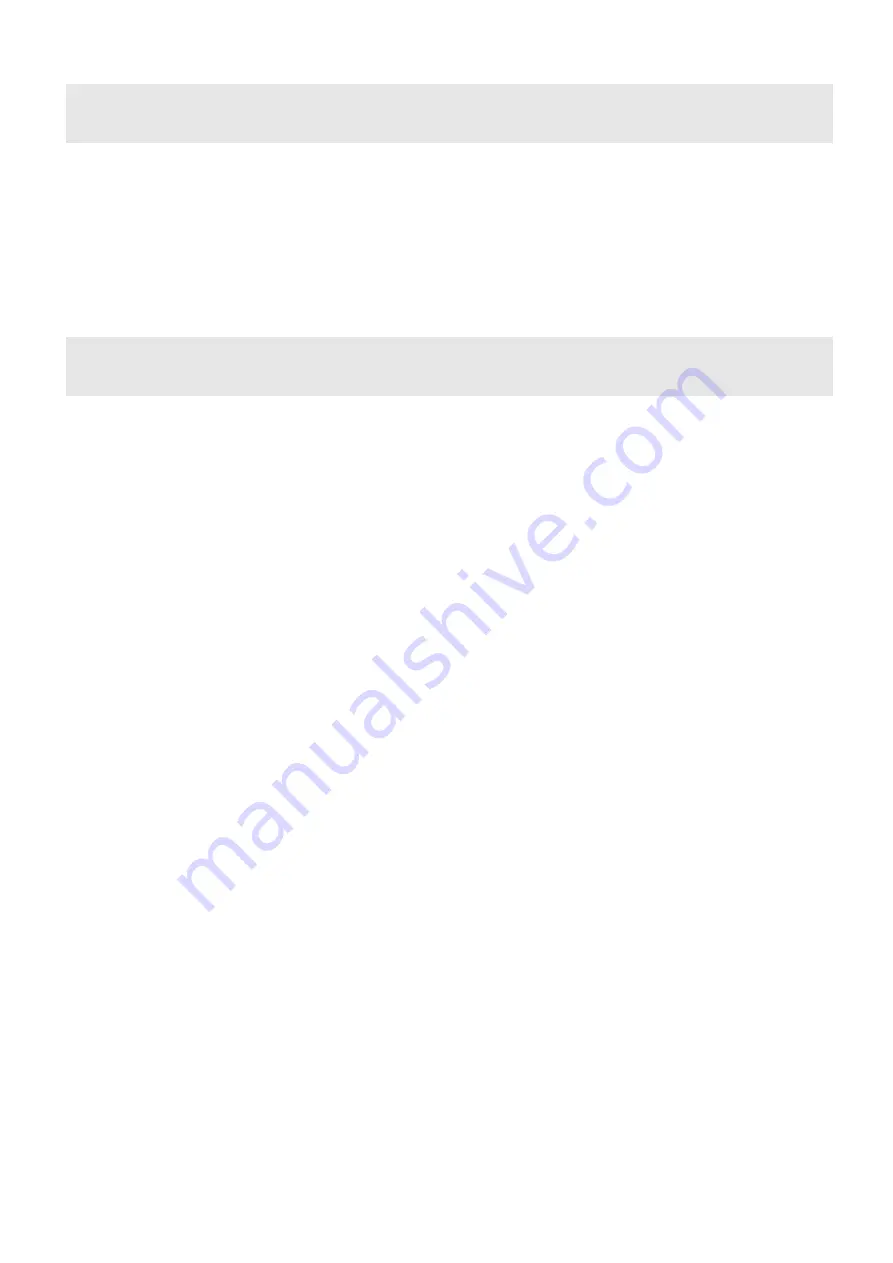
17
Maintenance
End Cap and Lubricating Systems are essential in order to protect and lubricate
the Bearing Units. These should be fitted back in place only when the guide
carriage has been mounted on the Shafts. Otherwise, it is important to ensure
the movable wipers are pressed back when sliding the guide carriage onto the
Shaft, to ensure they are not bent.
Wipers located in the internal recesses of the end-face End Cap and Lubricating
Systems are also designed to take up the lubricant. They are pressed against
the guiding Shaft by a spring. These wipers are supplied pre-charged with lubri-
cant and can be topped up with lubricant as required via the hole in the cap.
All good machine lubricating oils, bed track oils and transmission greases with
or without additives can be used, such as MoS2 or similar.
In the event of considerable soiling, you may need to replace the wipers.
Lubrication
Suitable for use in dry conditions and over the temperature range -20°C to
+70°C.
If operating conditions are unusual - e.g. special type of installation, dust, short
stroke, influence of solvents etc. the lubrication intervals must be adapted
accordingly.
This information does not discharge the user from the obligation to carry out his
own assessments and checks.
It is important to bear in mind that our products are subject to a natural process
of wear and ageing.
The rollers of the guide are maintenance-free. The spring-loaded end cap and
lubricating felts can be topped up with lubricant as required via a hole.
Recommended re-oiling period: Every 6 months or every 2500 km. The felt
pieces are supplied in ready-oiled condition.
Synthetic lubrication oil ISO VG 460, e.g. item Track Oil for Linear Guides
(0.0.612.75).
Add the following quantity to each maintenance hole at the end of each mainte-
nance interval: 1 ml
Greases containing solid particles (e.g. graphite and MoS2 additives) must not
be used!
Oil Can for Linear Guides (one actuation delivers approx. 1 ml of oil).
To ensure adequate lubrication, the carriage must cover a minimum travel
distance. Minimum stroke length [mm]: 80 mm
The Timing Belt is a maintenance-free drive element.
Check the tension on the Timing Belt after a running-in phase.
We recommend regular checks for damage and wear. These checks should be
carried out weekly at first and then adjusted to account for environmental and
operational conditions.
The Timing Belt may need to be replaced.
Ideal operating conditions:
Ambient temperature: 10°C ... 40°C
Load:
< 5%