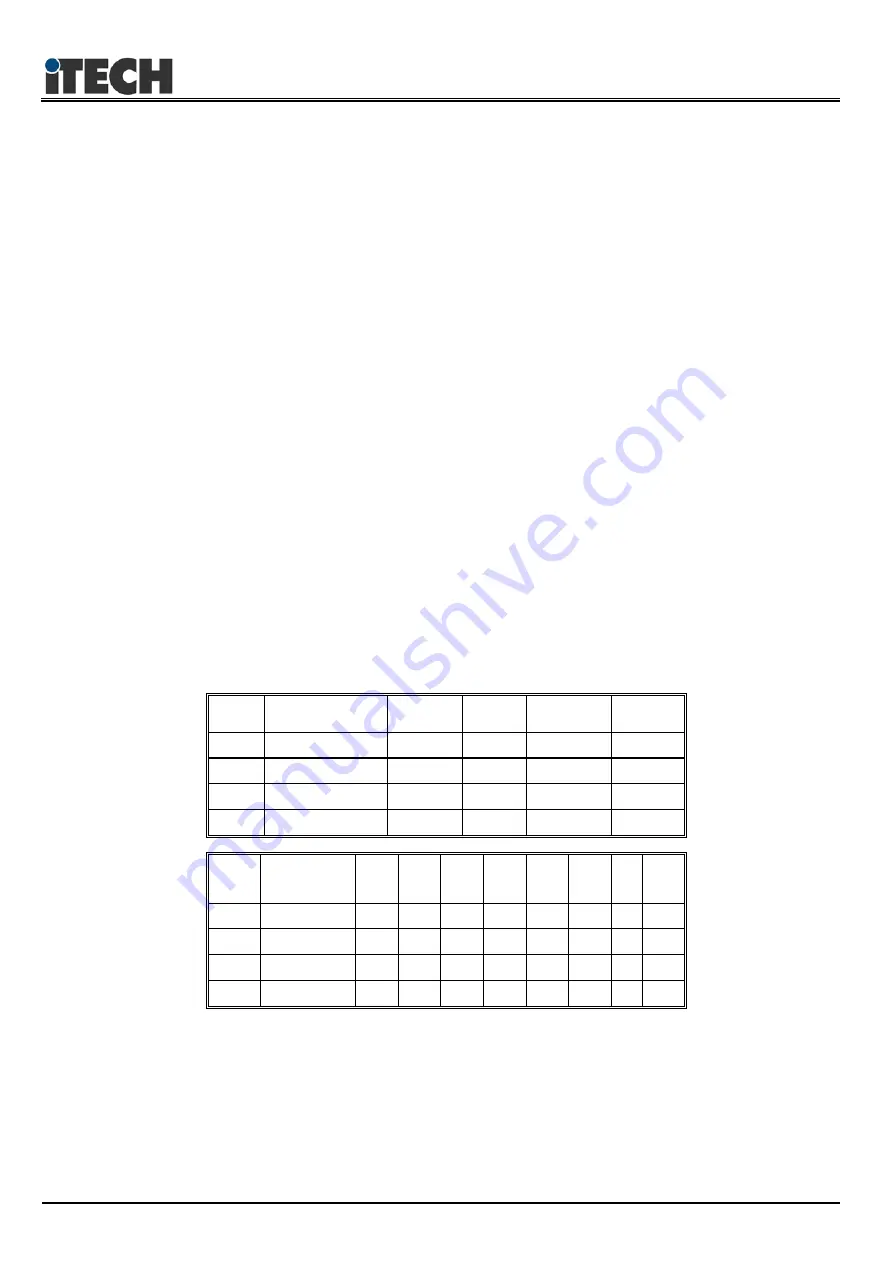
Dry Filter Spraybooth Installation and Maintenance Instructions
4
of panel joints. If the Booth canopy is to form part of a dust free environment the panel joints may be sealed with a
proprietary high velocity duct sealant.
8
Exhaust Ducting
Exhaust ducting venting an
Airflow
Spraybooth to atmosphere should be designed and installed by a competent
ventilation engineer. In order to ensure the correct operation of the
Airflow
Spraybooth and also ensure that the correct
volume of air is extracted at its face, the complete ducting system should be sized so as to achieve a maximum pressure
drop of “80Pa”.
Generally speaking, all ductwork should allow air an uninterrupted and smooth passage from the fan unit to the point of
discharge. All bends or transition sections should be designed so as to maintain the cross-sectional area of the fan
discharge diameter and performance checks should be carried out upon completion of the installation. Please Note:
Customers whose solvents consumption requires them to comply with the Environmental Protection Act (E.P.A.) must
pay particular attention to the design criteria of such ductwork as detailed by the Act.
Specialist information and advice can be sought from
Airflow
Product Finishing Limited on the suitability of intended
ductwork systems. Please contact our Sales Department for further advice.
9
Noise
Please refer to the tables over to obtain information of test results obtained from typical
Airflow
Spraybooth
installations. Please Note: Specific individual noise levels should be obtained following installation of your
Spraybooth, as it is impossible for
Airflow
to predict the properties of the acoustic environment in which your
Spraybooth is to be sited.
Please Note:
Airflow
will be pleased to advise on suitable in-duct silencers for use with their range of Spraybooths.
Please contact our Sales Department for further information.
SOUND TABLES
ITEM
IMPELLER CODE
MOTOR
kW
RPM
dB(A) @
3Dia
dBW
A
630/150/10s/30 DEG
1.5
1440
71
91
B
630/150/10s/40 DEG
2.2
1440
73
93
C
630/150/10s/40 DEG
3.0
1620
77
97
D
630/150/10s/40 DEG
4.0
1710
78
98
ITEM
MID
FREQUENCY
Hz
63
125
250
500
1k
2k
4k
8k
A
In-Duct dBW
88
86
85
84
83
78
73
62
B
In-Duct dBW
90
88
87
86
85
80
75
64
C
In-Duct dBW
94
92
91
90
89
84
79
68
D
In-Duct dBW
95
93
92
91
90
85
80
69
10
Electrical Data
Before removing the terminal box cover from the electric motor of the fan unit, ensure that its electrical supply has been
suitably isolated and cannot be switched on.
All electrical connections should be carried our by a qualified and authorised electrician in accordance with local site
regulations and the latest issue of the IEE Regulations.