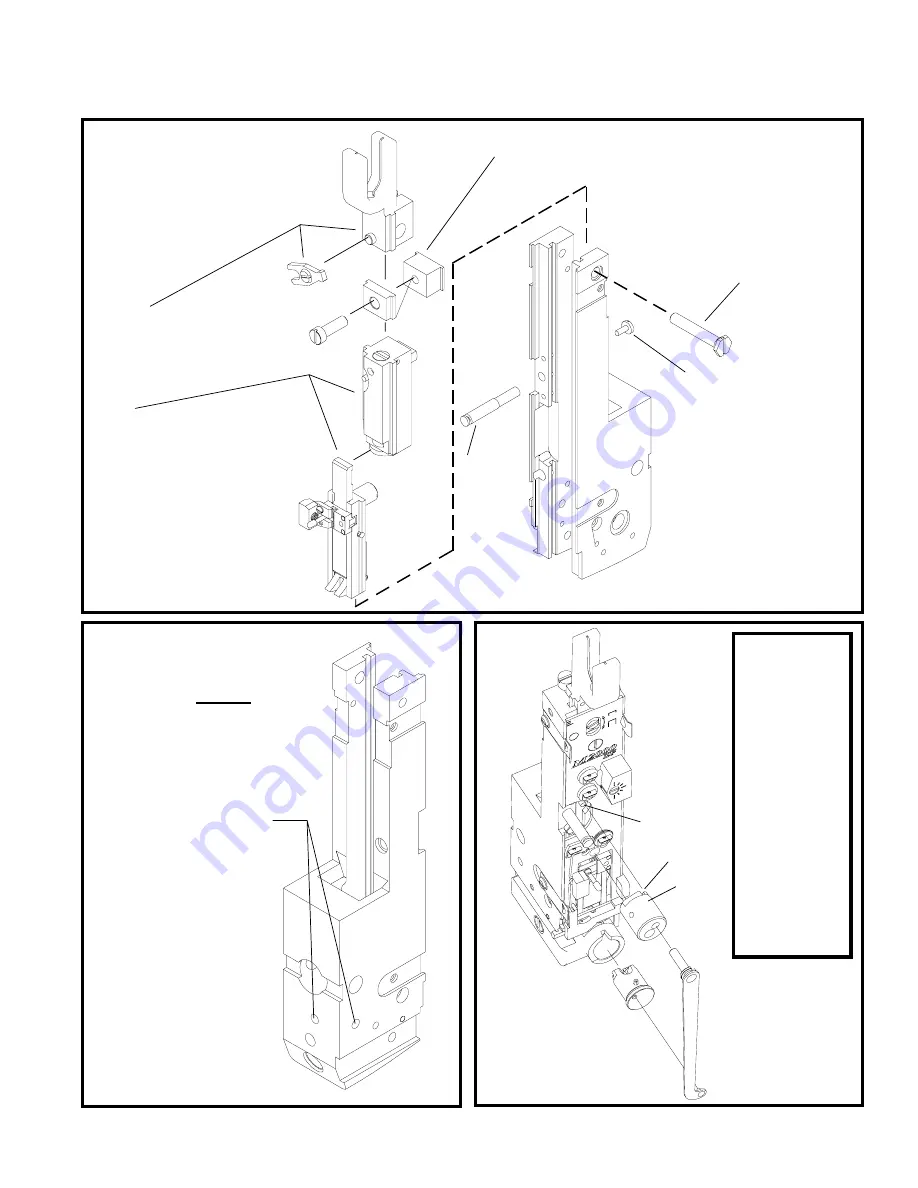
21
16. Slide tension spring bracket
and adjusting lever from top.
15. Remove screw
17. Loosen face plate clamp screw and
slide out face plate locating block.
18. Slide the driving slide and bender
bar assemblies from the top. When
reassembling, hook bender bar to
driving slide before sliding into place.
This must be assembled as a complete
unit.
A
B
C
Caution
When reassembling,
make certain that pin
(Index A) is visible
and is aligned with
slot (Index B) of
rotator operating cam
(Index C). If not
assembled in this
way, the bonnet
casting will crack or
break on the next
cycle under power.
It is recommended
that the stitcher be
cycled by hand to
test that proper
r e a s s e m b l y
procedure has been
followed.
DISMANTLING/REASSEMBLING M2000 HEAD
DO
NOT
REMOVE
OR ADJUST
THESE TWO
SCREWS.
(CTT2605 Scene 5)
F
D
The screws
are factory set
to control the
s u p p o r t e r
lever location.
E
(CTTT2605 Scene 23)
14. Remove
r o t a t o r
operating cam
stud.
13. Remove rotator
operating cam stud
screw.
(CTTT2605 Scene 22)