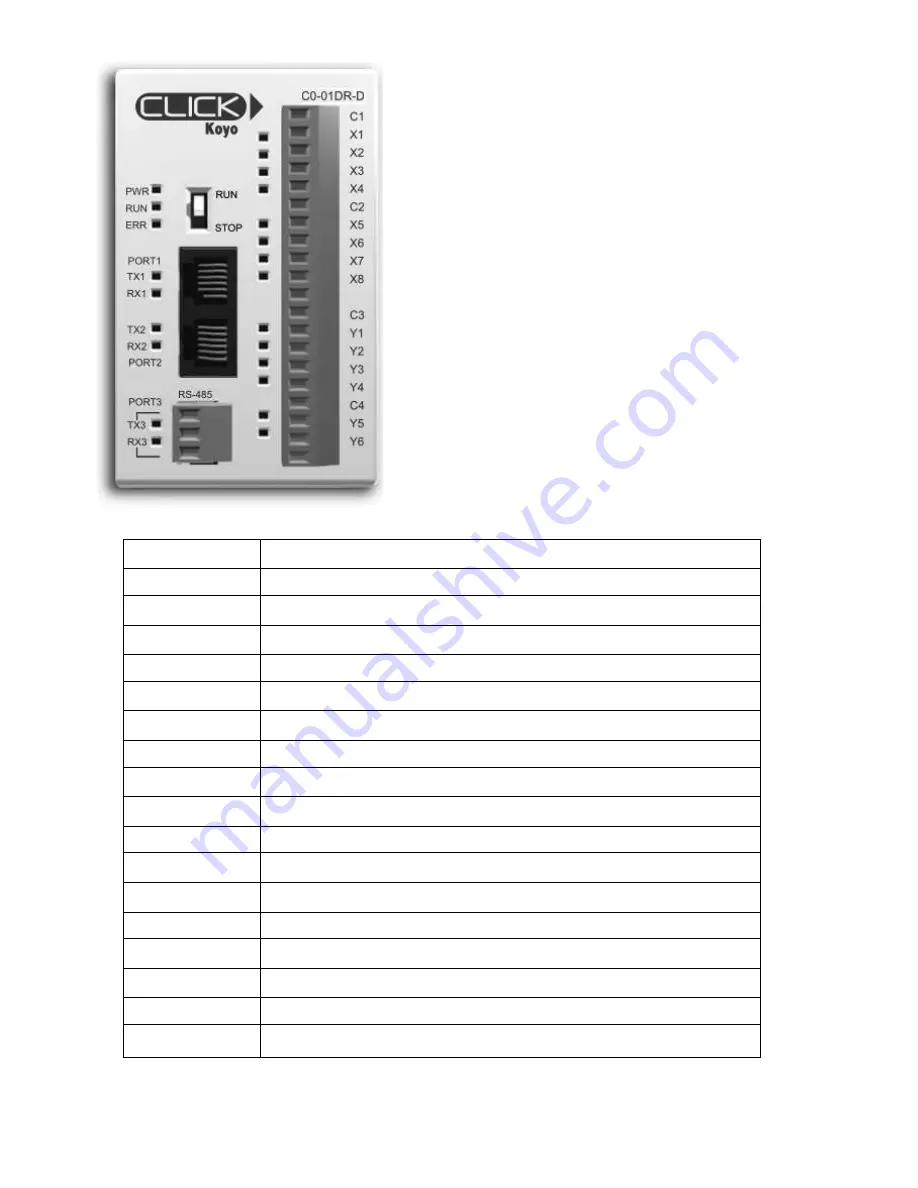
Page
9
PLC Overview:
Each RLA Style 3 Controller is equipped with a
Micro-PLC to control all of its functions.
The PLC comes programmed and wired from the
factory and should not be altered in any way.
Note:
All units will be shipped with the PLC
Mode switch in the STOP position. It should
remain in this position until Start-Up testing is
going to be performed. Once ready to test the
system, the switch must be set to the RUN
position for the controller to function.
Indicator Light
Description of Status When Light is On
PWR
PLC has 24VDC from Power Supply
RUN
PLC is set to RUN Mode and is operational
ERR
PLC Processor has incurred an error
X1
Door Panic Button is being pressed
X2
Alarm signal being received (Dry-Contact)
X3
Leak Sensor signal being received (Dry-Contact)
X4
Leak Sensor signal being received (Dry-Contact)
X5
Freeze Sensor signal being received (Dry-Contact)
X6
Seismic Sensor signal being received (Dry-Contact)
X7
Not Used
X8
Not Used
Y1
Circuit 1 active (Water - Supply)
Y2
Circuit 2 active (Water - Drain Down)
Y3
Circuit 3 active (Gas Supply)
Y4
Circuit 4 active (Electrical Shunt)
Y5
Beacon Output (ON with service)
Y6
Beacon Output (OFF with service)
Table 1
Summary of Contents for RLA Series
Page 5: ...Page 5...