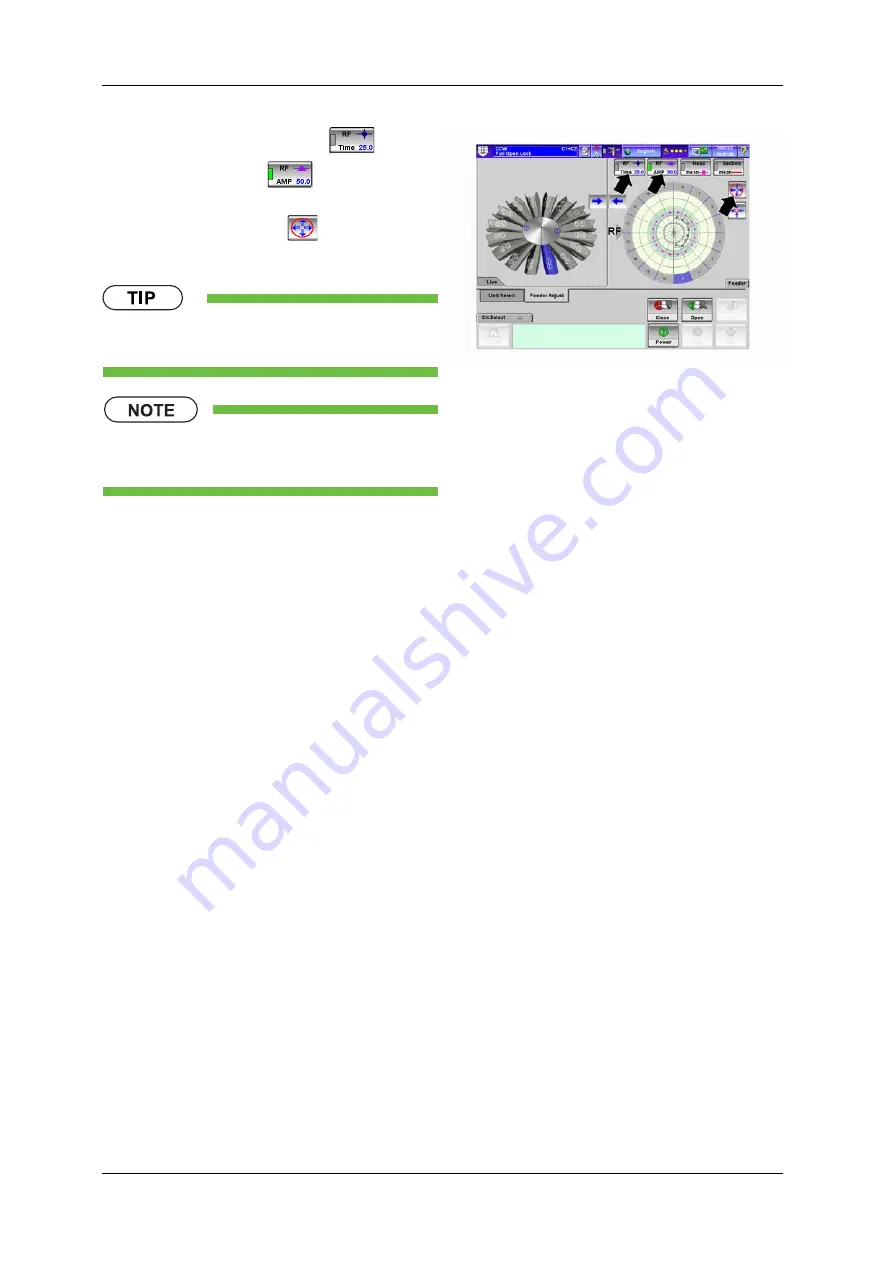
7 USEFUL FUNCTIONS
CCW-R-2**B INSTRUCTION MANUAL
7-10
5. Press the [RF Time] lamp key
and the
[RF AMP] lamp key
to select the
operation time and operation amplitude, and
press the [Increase] key
to set a larger
value for each setting.
•
Setting a larger value can discharge products
faster.
•
Feeder values changed during full open
lock are not reflected in the preset.
Fig.7-21 [Feeder Adjust] Tab Screen
([Full Open Lock] Screen)
Summary of Contents for CCW-R-2 B Series
Page 4: ... 2 ...
Page 20: ...CCW R 2 B INSTRUCTION MANUAL 12 ...
Page 28: ...1 SAFETY PRECAUTIONS CCW R 2 B INSTRUCTION MANUAL 1 8 ...
Page 115: ...CCW R 2 B INSTRUCTION MANUAL 6 FUNCTIONS OF THE OPERATION SCREENS 6 3 ...
Page 116: ...6 FUNCTIONS OF THE OPERATION SCREENS CCW R 2 B INSTRUCTION MANUAL 6 4 ...
Page 117: ...CCW R 2 B INSTRUCTION MANUAL 6 FUNCTIONS OF THE OPERATION SCREENS 6 5 ...
Page 118: ...6 FUNCTIONS OF THE OPERATION SCREENS CCW R 2 B INSTRUCTION MANUAL 6 6 ...
Page 119: ...CCW R 2 B INSTRUCTION MANUAL 6 FUNCTIONS OF THE OPERATION SCREENS 6 7 ...
Page 120: ...6 FUNCTIONS OF THE OPERATION SCREENS CCW R 2 B INSTRUCTION MANUAL 6 8 ...
Page 288: ...7 USEFUL FUNCTIONS CCW R 2 B INSTRUCTION MANUAL 7 14 ...
Page 310: ...8 OPTIONAL FUNCTIONS CCW R 2 B INSTRUCTION MANUAL 8 22 ...
Page 374: ...11 CAUSES AND ACTIONS FOR ERRORS AND FAILURES CCW R 2 B INSTRUCTION MANUAL 11 26 ...
Page 463: ... 0 00 102 4577 052 ...
Page 465: ... 00 1 11 2 34 34 2 5 5 66 6 7276 89 4 0 8 03 0 0344 A93 A 3 8 A B 4A 3 3C 5 ...
Page 466: ... 107 2454 00 ...
Page 467: ... 107 2452 02 ...
Page 470: ... 107 2458 04 ...
Page 471: ... 0 1 0 1 0 1 0 1 0 1 0 1 2 3 105 0490 021 ...
Page 473: ... 0 123 2456781597 0 102 3901 053 00 ...
Page 476: ... 0 0 1 2 1 1 2 1 1 1 3 33 086 6134 04 ...
Page 477: ...086 6135 08 ...
Page 488: ...10 INDEX CCW R 2 B INSTRUCTION MANUAL ...
Page 490: ......
Page 491: ......
Page 492: ......