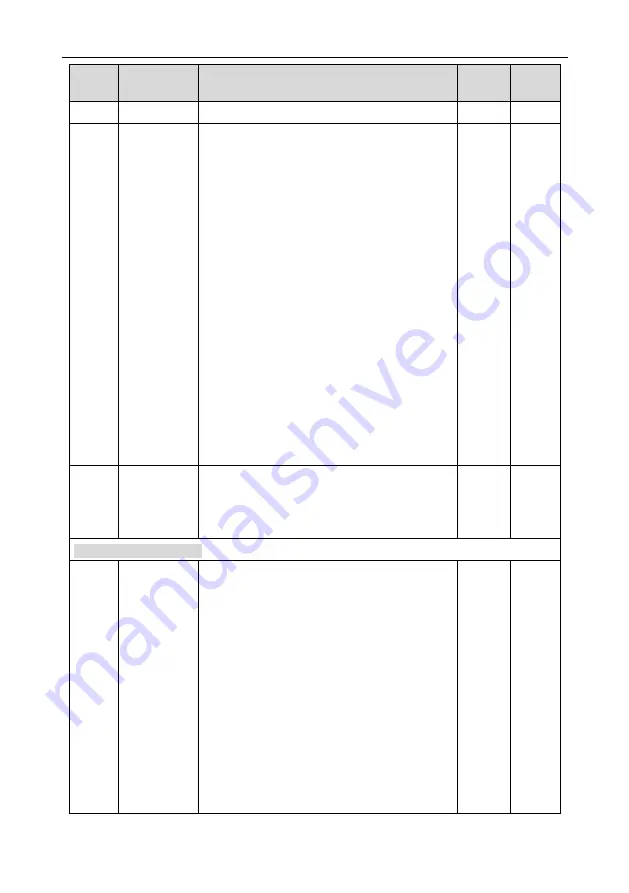
is procedure PID controlled.
monitors the state of the motor
used to increase the magnetic flux to
Function Parameters
81
Function
code
Name
Description
Default
value
Modify
: 0.0
–999.9
E08.50
Magnetic flux
braking
This function code is used to enable magnetic flux.
0: Invalid.
100
–150: The bigger the coefficient, the stronger
the braking is.
decelerate the motor. The energy generated by
the motor during braking can be converted into
heat energy by increasing the magnetic flux.
continuously even during the magnetic flux period.
So the magnetic flux can be used in the motor
stop, as well as to change the rotation speed of
the motor. Its other advantages are:
Brake immediately after the stop command. It
does not need to wait the magnetic flux weaken.
Better cooling for motors. The current of the stator
other than the rotor increases during magnetic flux
braking, while the cooling of the stator is more
effective than the rotor.
0
●
E08.51
Current
regulation
coefficient on
input side
This function code is used to adjust the displayed
current of the AC input side.
Setting range: 0.00
–1.00
0.56
○
E09 Group PID control
E09.00
PID reference
source
When the frequency command selection (
) is 7 or the voltage setting channel
selection (
) is 6, the running mode of the
The parameter determines the target reference
channel during the PID procures.
0: Keypad digital reference (
1: Analog channel AI1 reference (implemented
through the analog potentiometer on the keypad
for the 0150G/018P and lower models; not
available for the 018G/022P and higher models.)
2: Analog channel AI2 reference
3: Analog channel AI3 set
4: High speed pulse HDI set
0
○