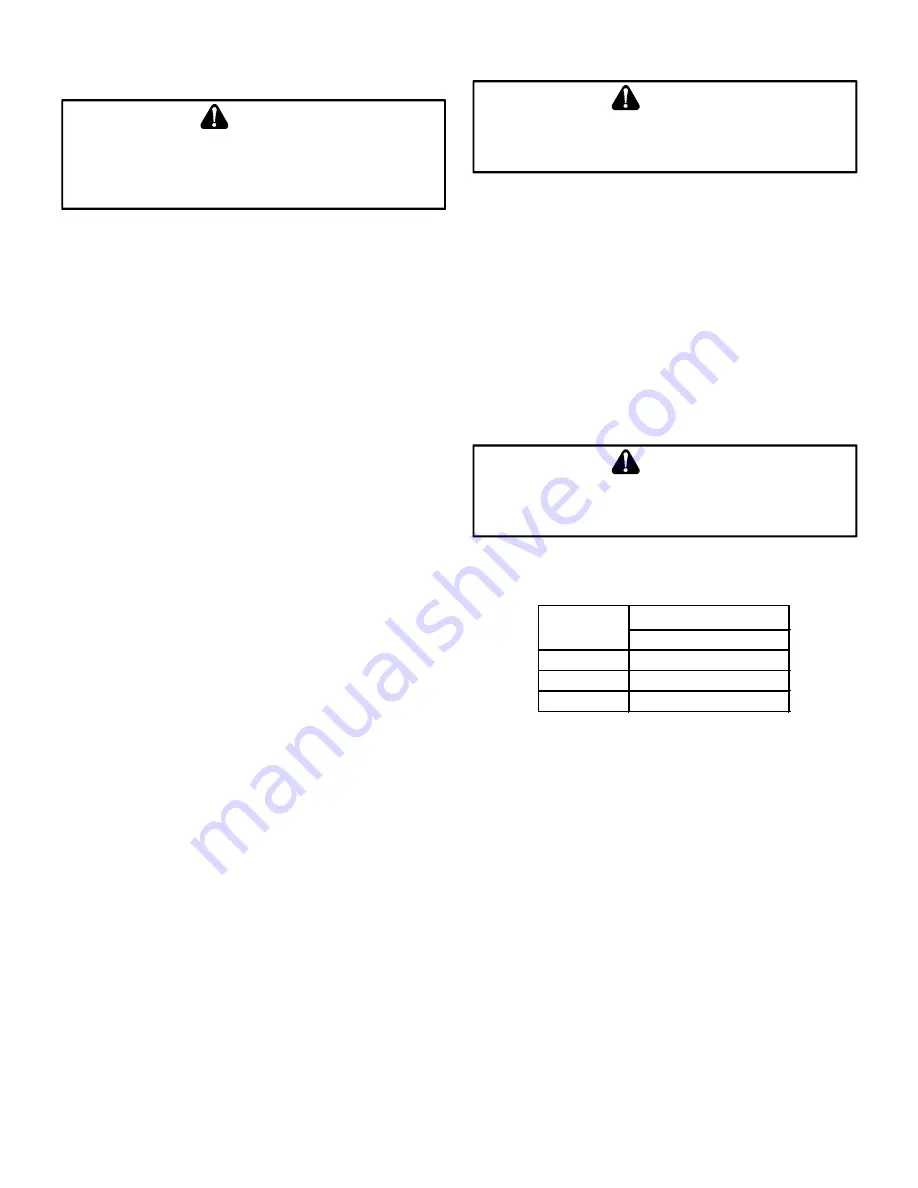
10
Combustion and Ventilation
Air Requirements
T
O
AVOID
PROPERTY
DAMAGE
,
PERSONAL
INJURY
OR
DEATH
,
SUFFICIENT
FRESH
AIR
FOR
PROPER
COMBUSTION
AND
VENTILATION
OF
FLUE
GASES
MUST
BE
SUPPLIED
. M
OST
HOMES
REQUIRE
OUTSIDE
AIR
BE
SUPPLIED
INTO
THE
FURNACE
AREA
.
WARNING
Improved construction and additional insulation in buildings
have reduced heat loss by reducing air infiltration and escape
around doors and windows. These changes have helped in
reducing heating/cooling costs but have created a problem
supplying combustion and ventilation air for gas fired and
other fuel burning appliances. Appliances that pull air out
of the house (clothes dryers, exhaust fans, fireplaces, etc.)
increase the problem by starving appliances for air.
House depressurization can cause back drafting or improper
combustion of gas-fired appliances, thereby exposing building
occupants to gas combustion products that could include
carbon monoxide.
If this furnace is to be installed in the same space with other
gas appliances, such as a water heater, ensure there is an
adequate supply of combustion and ventilation air for all
appliances. Refer to the latest edition of the National Fuel
Gas Code NFPA 54/ANSI Z223.1 or applicable provisions of
the local building codes for determining the combustion air
requirements for the appliances.
This furnace must use indoor air for combustion. It cannot be
installed as a direct vent (i.e., sealed com bustion) furnace.
Most homes will require outside air be supplied to the furnace
area by means of ventilation grilles or ducts connecting directly
to the outdoors or spaces open to the outdoors such as attics
or crawl spaces. A furnace installed in a confined space (i.e.,
a closet or utility room) must have two ventilation openings
with a total minimum free area of 0.25 square inches per
1,000 BTU/hr of furnace input rating. Refer to Specification
Sheet applicable to your model for minimum clearances to
combustible surfaces. One of the ventilation openings must
be within 12” of the top; the other opening must be within 12”
of the bottom of the confined space. In a typical construction,
the clearance between the door and door frame is usually
adequate to satisfy this ventilation requirement.
Category I Venting (Vertical Venting)
T
O
PREVENT
POSSIBLE
PERSONAL
INJURY
OR
DEATH
DUE
TO
ASPHYXIATION
,
THIS
FURNACE
MUST
BE
C
ATEGORY
I
VENTED
. D
O
NOT
VENT
USING
C
ATEGORY
III
VENTING
.
WARNING
Category I Venting is venting at a non-positive pressure. A
furnace vented as Category I is considered a fan-assisted
appliance and the vent system does not have to be “gas tight.”
NOTE:
Single stage gas furnaces with induced draft blowers
draw products of combustion through a heat exchanger
allowing, in some instances, common venting with natural
draft appliances (i.e. water heaters). All installations must be
vented in accordance with the latest edition of the National
Fuel Gas Code NFPA 54/ANSI Z223.1 .
Note:
The vertical height of the category 1 venting system
must be at least as great as the horizontal length of the vertical
system.
T
O
PREVENT
POSSIBLE
PERSONAL
INJURY
OR
DEATH
DUE
TO
ASPHYXIATION
,
COMMON
VENTING
WITH
OTHER
MANUFACTURER
’
S
INDUCED
DRAFT
APPLIANCES
IS
NOT
ALLOWED
.
WARNING
The minimum vent diameter for the Category I venting system
is as shown:
MINIMUM VENT
UPFLOW
40
4 Inch
60
4 Inch
80
4 Inch
MODEL
Table 2
Under some conditions, larger vents than those shown above
may be required or allowed.
When an existing furnace is
removed from a venting system serving other appliances
, the
venting system may be too large to properly vent the remaining
attached appliances.