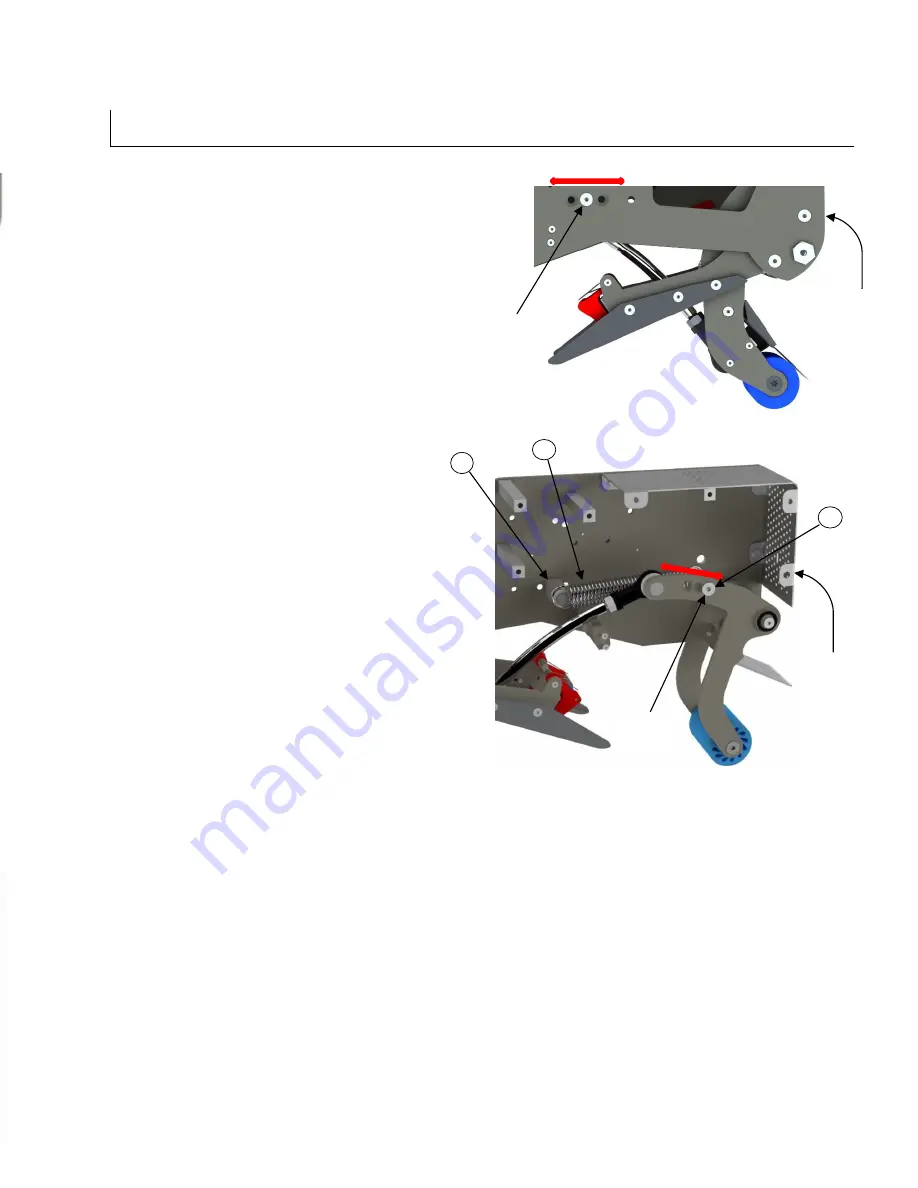
23
R05
FRONT OF
T.H.
M5 FHCS
S
ET
-U
P
P
ROCEDURES
Option 2:
To change the rollers’ pressure one can move
the spring retainer’s position on the cover
frame. Move the M5 FHCS towards the front of
the tape head to increase the pressure or
towards the rear to decrease the pressure. See
Figure 8-2
.
Option 3:
When the loop is still persevering in
the rear tape leg, one can raise the
spring retainers position on the rear
arm
.
This will increase the torque on
the rear arm. Loosen the M6 FHCS
on the rear arm and move a position
up, farther away from the pivot axis.
2
1
3
The previously listed 3 options may need to be employed in combination to get the best result.
For instance, to get the 3-inch tape head in top tape head mode at 120 ft/min line speed make
the following set up, refer to
Figure 8-3
. Put the M6 FHCS (
item 1
) on rear arm on the second
position from pivot shaft. Put the M6 FHCS (
Item 3
) on the Cover Frame closest to the rear end
position. Take the heavy stainless steel main spring UPH1091 (
item 2
) and attach it to these
spring retainer points.
A reminder to tone down unrealistic expectations; boxes without stamina cannot be processed at
high speeds!
Figure 8-2
Figure 8-3
M6
FHCS
REAR OF
T.H.
Summary of Contents for ET xtreme Series
Page 1: ...1 R05 ET xtreme STANDARD TAPE HEAD Serial Numbers UH230T UH430T ...
Page 2: ...2 R05 ...
Page 10: ...10 R05 SPECIFICATIONS UUUTape Head Dimensions Figure 6 1 ...
Page 11: ...11 R05 SPECIFICATIONS UUU Tape Head Components Figure 6 2 ...
Page 43: ...43 R05 THIS PAGE INTENTIONALLY LEFT BLANK ...
Page 44: ...4 6 10 8 1 9 3 5 7 2 11 12 13 44 ...
Page 46: ...1 15 2 3 6 10 12 14 7 11 8 9 5 4 16 14 13 13 4 18 17 46 ...
Page 48: ...6 11 8 14 2 12 9 7 10 5 3 3 13 48 ...
Page 50: ...6 7 15 11 10 14 4 2 9 3 5 13 12 8 1 16 50 ...
Page 52: ... 8 8 ...
Page 53: ... 7 0 3 57 6 5 37 21 8 47 8 47 83 8 52 5 83 2035 66 21 635 1 83 8 52 5 ...
Page 54: ...2 4 1 5 3 54 ...
Page 56: ... 8 8 ...
Page 58: ... 86 86 ...
Page 60: ...2 4 1 3 5 6 5 60 ...
Page 62: ...2 3 6 5 1 8 4 12 9 7 9 10 11 62 ...
Page 64: ...5 15 7 6 12 2 14 4 3 13 10 8 9 1 11 16 64 ...
Page 66: ...3 1 2 2 1 3 Standard Tape Head Mirror Tape Head 66 ...
Page 68: ...5 2 10 4 11 3 8 6 7 1 9 12 68 ...
Page 70: ...1 3 2 70 ...
Page 72: ... 8 8 ...
Page 74: ...6 1 2 5 3 4 74 ...
Page 76: ...19 4 9 16 6 7 5 8 1 11 3 10 14 12 15 13 18 17 2 20 76 ...
Page 78: ...1 2 No Tape options are available 78 ...