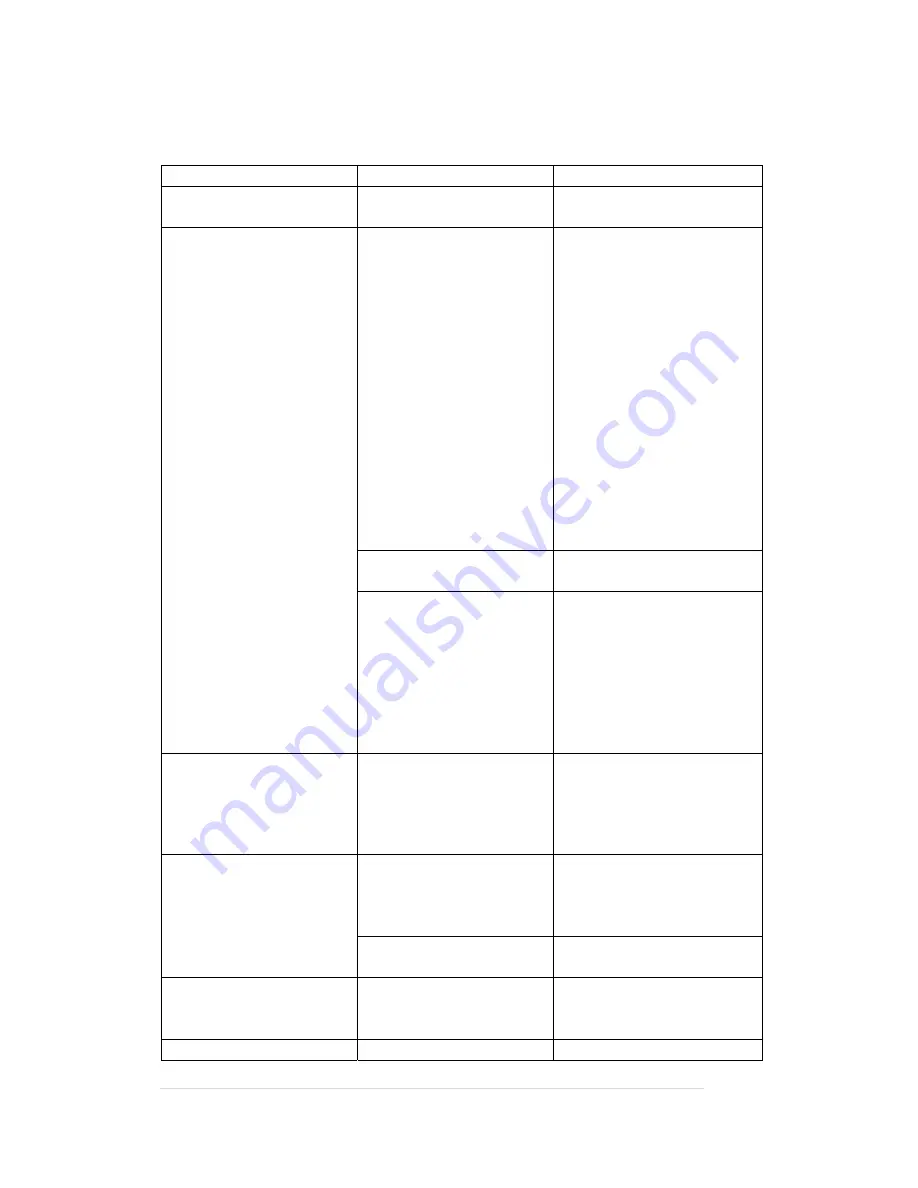
106 |
P a g e
Troubleshooting
Problem
Root Cause
Solution
Resin in the emulsion tank
hardened.
Tank not properly
emptied after use
Clean the emulsion tank
(see page 112).
Blocked nozzles or nozzles
spraying unevenly across
spray bars
Spray bar cold due to poor
circulation of hot
emulsion through the
spray bars, which is in
turn caused by blockage
or incorrect valve
alignment
Make sure emulsion in the
tank is 180° F or hotter.
1. Run Tank Circulate to
heat the plumbing in the
pump station.
2. Run Spray bar Circulate. If
the spray bar begins to
warm slowly, continue to
run Spray bar Circulate for
10 minutes to melt any hard
emulsion in the spray bar. If
hot emulsion is not flowing
through the spray bar,
check alignment of the
pump station valves (see
Appendix 1).
Nozzles mismatched
Verify all nozzles are the
same size and style.
Flow rate for nozzles too
low
Increase flow through
nozzles by 1, increasing
application rate and/or 2,
increasing travel speed.
If 1 and 2 cannot be done or
do not resolve the problem,
install lower capacity
nozzles.
Nozzles spray stopping
sporadically
Clogged nozzle
Remove the nozzle, and
rinse it with clean out fluid
to flush out any solid
particles and dissolve
hardened emulsion.
Spray nozzles continue to
drip although closed
With center or inner spray
bar nozzles: Spring
tension too low
Clean emulsion from the top
of the valve to free spring. If
still too loose, add washers
to increase tension.
With outer spray bar
nozzles: locknut too loose
Tighten the locknut on valve
stem.
Emulsion pump stuck
System not cleaned after
use
Clean the pump (see page
116).
Emulsion small pump
New pump installed
Set the small pump bypass