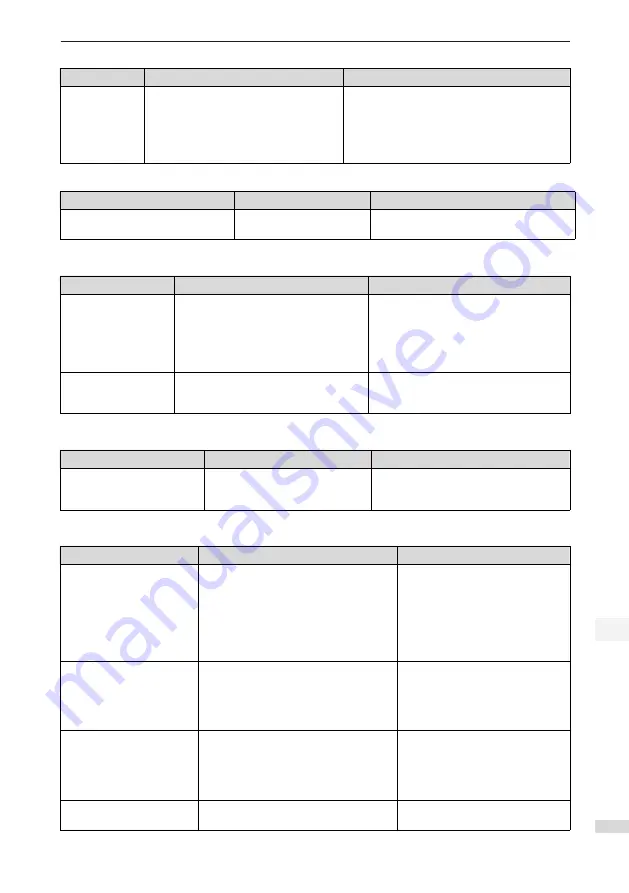
5 Troubleshooting
5
- 59 -
Cause
Confirming Methods
Corrective Action
3. Speed of high-
speed searching
home switch
signal is too
small.
Check distance from initial position of
returning to home to home switch. Then
check whether H5-32 (speed of home
switch signal at high-speed searching)
is too small, resulting in too long time of
finding home switch.
Increase H05-32.
Er.730: Encoder battery warning
Cause
Confirming Methods
Corrective Action
Battery voltage of absolute encoder is
lower than 3.0 V.
Measure battery voltage.
Replace a new battery with matching
voltage.
Er.831: AI zero drift too large
Cause
Confirming Methods
Corrective Action
1. AI wiring is incorrect
or interference exists.
Check wiring by referring to correct wiring
diagram.
Use shielded twisted pair cable and shorten
cable length.
Increase AI filter time constant:
AI1 filter time constant: H03-51
AI2 filter time constant: H03-56
2. The servo drive is
faulty.
Disconnect AI cable (input voltage is 0).
Check whether AI sampling value in group
H0B exceeds 500 mV.
If AI sampling value in group H0B exceeds
500 mV, replace the servo drive.
Er.900: DI emergency braking
Cause
Confirming Methods
Corrective Action
DI function FunIN.34:
EmergencyStop is triggered.
Check whether logic of DI set for
FunIN.34: EmergencyStop is valid.
Check the running mode and clear DI
braking valid signal on the prerequisite of
ensuring safety.
Er.909: Motor overload warning
Cause
Confirming Methods
Corrective Action
1. Wiring of motor and
encoder is incorrect or poor.
Check wirings between servo drive, servo
motor and encoder according to correct
wiring diagram.
Connect wirings based on correct
wiring diagram.
Prefer to use the cable configured by
Inovance as standard.
When self-made cable is used, make
and connect wirings according to
hardware wiring guidance.
2. The load is too heavy.
The motor keeps output of
effective torque higher than
rated torque for a long time.
Confirm overload characteristic of servo
drive or servo motor.
Check whether average load rate (H0B-12)
is greater than 100.0% for long time.
Replace a large servo drive and
matching servo motor.
Reduce the load and increase
acceleration/deceleration time.
3. Acceleration/deceleration
is too frequent or load inertia
is too large.
Calculate load inertia ratio or perform load
inertia ratio auto-tuning. Then view H08-15
(load inertia ratio).
Conform single running cycle when servo
motor runs in circular.
Increase acceleration/deceleration
time.
4. The gain is improper,
causing too high rigidity.
Observe whether motor vibrates and
generates noise during running.
Adjust the gain.
Summary of Contents for IS650P Series
Page 1: ......
Page 101: ...100 Revision History Date Version Change Description March 2017 A00 First issue...
Page 102: ......