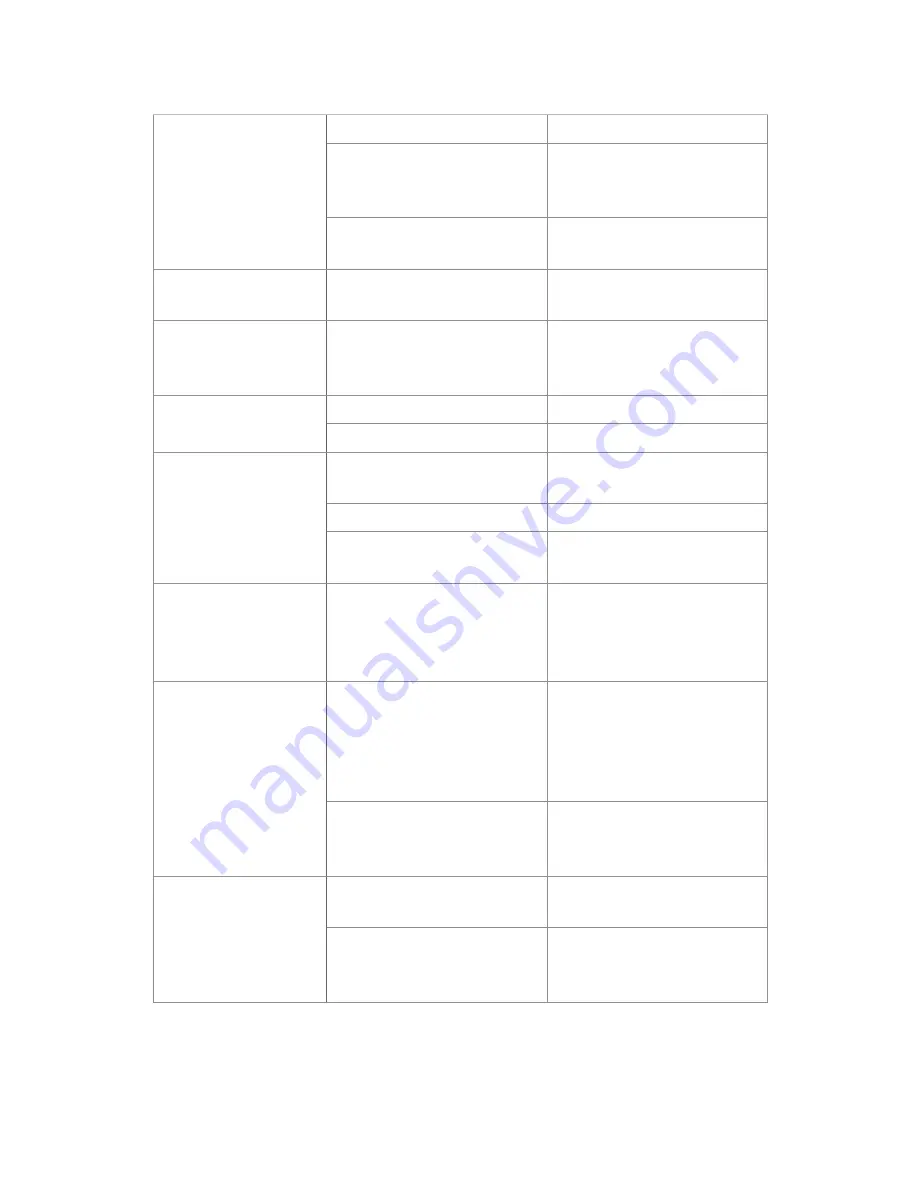
Appendix II
47
Unknown Fiber Type
Dust on the fiber surface.
Re-prepare the fiber.
Different fiber types on two sides.
AUTO mode is not applicable in
this case; select a suitable splice
mode to redo splicing.
The fiber is a non-standard fiber.
AUTO mode can only detect
standard SM, MM, NZ fibers.
Fiber Clad Over Limit
Fiber edge is not located in the
camera range.
Adjust the fiber position; perform
[Motor Calibration].
Focus Motor Home
position Error
Shock occurred to the splicer
during the splicing process.
Perform [Motor Calibration]. If
the problem still exists, please
contact the sales agent.
Fiber Endface Gap Wrong
[Overlap] is too much.
Adjust [Overlap] parameter.
Motor is not calibrated.
Perform [Motor calibration].
Focus Motor Distance
Over Limit
The fiber is misplaced.
Press RESET button and
reposition the fiber correctly.
Dust or dirt on the fiber surface.
Prepare the fiber again.
Dust or dirt on the lenses.
Perform [Dust Check] after the
lenses are cleaned.
Fibers Mismatch,
Continue?
Different fiber types on two sides.
It may result in large splice loss
if you continue to splice. Please
use the proper splice mode
corresponding to the fibers.
Cleave Angle Over Limit
Bad fiber endface.
Check the condition of the fiber
cleaver. If the blade is worn,
rotate the blade to a new position
or change a new one, and then
re-prepare the fibers.
[Cleave Angle Limit] is set too low.
Increase the [Cleave Angle Limit]
to an adequate limit (standard:
3.0˚).
Core Angle Over Limit
[Core Angle Limit] is set too low.
Increase the [Core Angle Limit] to
an adequate limit (standard: 1.0˚).
Dust or dirt on the V-groove or
fiber holders.
Clean the V-groove and fiber
holders. Prepare the fibers and
re-load them.
Summary of Contents for VIEW 5
Page 2: ...1 View 5 User Manual...
Page 3: ...2...