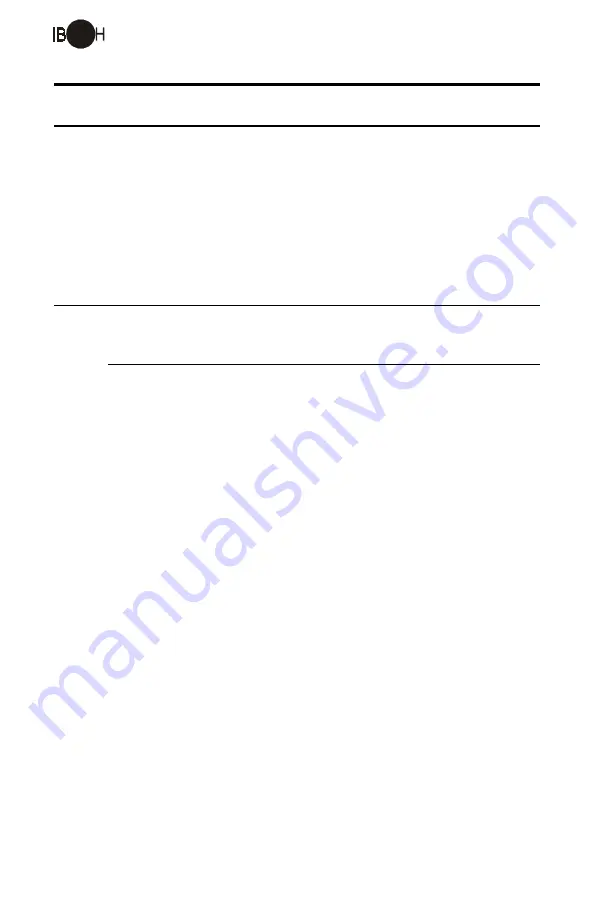
16
462
S e c t i o n 1 . 5
P o w e r S u p p l y R e q u i r e m e n t s
S e c t i o n O v e r v i e w
This section covers the power supply requirements the IB462H. Precise wiring
and connection details may be found in Section 1.7,
Interfacing to the
IB462H
. The following is covered by this section:
Selecting power supplies.
Recommended wiring.
AC line filtering.
S e l e c t i n g P o w e r S u p p l i e s
S e l e c t i n g a M o t o r S u p p l y ( + V )
Proper selection of a power supply to be used in a motion system is as
important as selecting the drive itself. When choosing a power supply for a
stepping motor driver there are several performance issues that must be
addressed. An undersized power supply can lead to poor performance and
possibly even damage to your drive.
T h e P o w e r S u p p l y - M o t o r R e l a t i o n s h i p
Motor windings can be basically viewed as inductors. Winding resistance and
inductance result in an L/R time constant that resists the change in current. To
effectively manipulate the rate of charge, the voltage applied is increased. When
traveling at high speeds there is less time between steps to reach current. The
point where the rate of commutation does not allow the driver to reach full
current is referred to as Voltage Mode. Ideally you want to be in Current Mode,
which is when the drive is achieving the desired current between steps. Simply
stated, a higher voltage will decrease the time it takes to charge the coil and,
therefore, will allow for increased torque at higher speeds.
Another characteristic of all motors is back EMF. Back EMF is a source of
current that can push the output of a power supply beyond the maximum
operating voltage of the driver and, as a result, could damage the stepper
driver.
T h e P o w e r S u p p l y - D r i v e r R e l a t i o n s h i p
The IB462H is very current efficient as far as the power supply is concerned.
Once the motor has charged one or both windings of the motor, all the power
supply has to do is replace losses in the system. The charged winding acts as
an energy storage in that the current will recirculate within the bridge, and in
and out of each phase reservoir. This results in a less than expected current
draw on the supply.