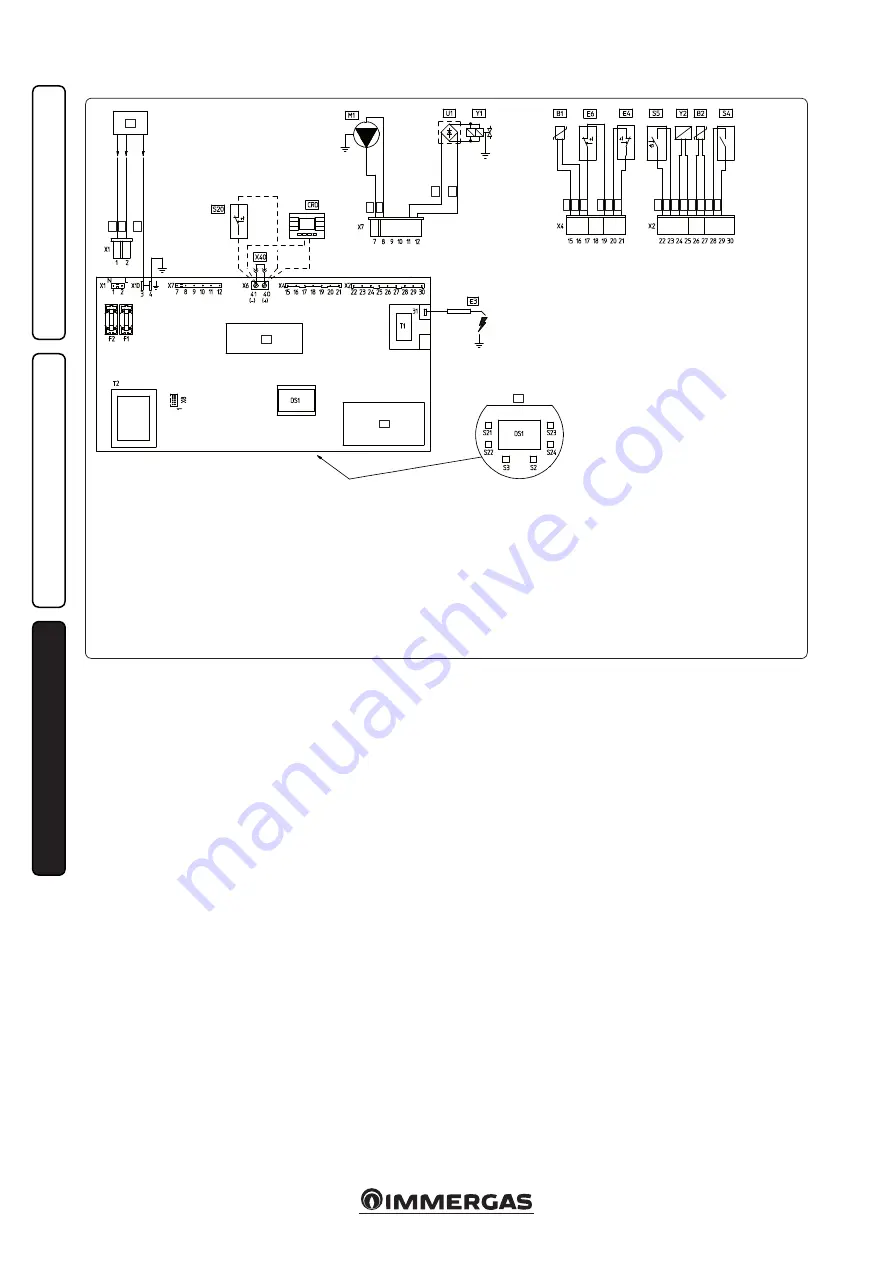
14
3-2
6
1
3
2
7
6
5
4
5
5
6
10
9
9
8
8
8
10
10
8
9
11
11
9
10
INS
TALLER
US
ER
MAINTEN
AN
CE TECHNI
CI
AN
Key:
B1 - Delivery probe
B2 - Domestic hot water probe
CRD - Digital Mini Remote Control (optional)
DS1 - Display
E3 - Ignition and detection electrodes
E4 - Safety thermostat
E6 - Flue safety thermostat
F1 - Phase fuse
3.2 WIRING DIAGRAM.
F2 - Neutral fuse
M1 - Boiler circulating pump
S2 - Selector switch functioning
S3 - Reset block keys
S4 - Domestic hot water flow switch
S5 - System pressure switch
S20 - Room thermostat (optional)
S21 - Domestic hot water temperature
increase key
S22 - Domestic hot water temperature
reduce key
S23 - Heating temperature increase key
S24 - Heating temperature reduce key
T1 - Switch-on transformer
T2 - Boiler board transformer
U1 - Rectifier inside the gas valve
connector (Only available on
Honeywell gas valves)
X40 - Room thermostat jumper
Y1 - Gas valve
Y2 - Gas valve modulator
1 - User interface
2 - N.B.: The user interface is on the
welding side of the boiler board
3 - The X6 connector is used for
automatic inspection
4 - 230 Vac 50Hz power supply
5 - Blue
6 - Brown
7 - Yellow/Green
8 - Black
9 - Grey
10 - White
11 - Red
The boiler is designed for application of a room
thermostat (S20), an On/Off room chrono-
thermostat, a program timer or a Digital Mini
Remote Control (CRD). Connect it to clamps
40 –41 eliminating jumper X40.
3.3 TROUBLESHOOTING.
N.B.:
Maintenance must be carried out by a
qualified company (e.g. Technical After-Sales
Assistance Service).
- Smell of gas. Caused by leakage from gas circuit
pipelines. Check sealing efficiency of gas intake
circuit.
- Irregular combustion (red or yellow flame).
When the burner is dirty or the boiler lamellar
pack is blocked. Clean the burner or the boiler
lamellar pack.
- Frequent activation of the temperature over-
load thermostat. It can depend on the lack of
water in the boiler, little water circulation in
the system or blocked pump. Check on the
manometer that the system pressure is within
established limits. Check that the radiator val-
ves are not closed and also the functionality of
the pump.
- The boiler produces condensate. This can be
caused by obstructions of the chimney or flues
with height or section not proportioned to the
boiler. It can also be determined by functioning
at boiler temperatures that are excessively low.
In this case, make the boiler run at higher
temperatures.
- Frequent interventions of the chimney safety
thermostat. This can be caused by obstructions
in the fumes circuit. Check the flue. The flue
may be obstructed or by height or section
not suitable for the boiler. Ventilation may be
insufficient (see room ventilation point).
- Presence of air in the system. Check opening
of the special automatic vent valve (Fig. 1-6).
Make sure the system pressure and expansion
vessel pre-charge values are within the set
limits; the pre-charge value for the expansion
vessel must be 1.0 bar, and system pressure
between 1 and 1.2 bar.
- Ignition block and Chimney block. (See par.
2.5 and 1.5 (electric connection).
- Low water flow: if, as a result of limescale (cal-
cium and magnesium), the domestic hot water
system does not work properly contact a qua-
lified technician for descaling e.g. Immergas
After-Sales Technical Service. Descaling must
be carried out on the domestic hot water side
of the bithermal heat exchanger in accordance
with good practice. To preserve integrity and
efficiency of the heat exchanger, a non corro-
sive descaler must be used. Cleaning must be
carried out without the use of tools which can
damage the heat exchanger.
3.4 CONVERTING THE BOILER TO
OTHER TYPES OF GAS.
If the boiler has to be converted to a different gas
type to that specified on the data plate, request
the relative conversion kit for quick and easy
conversion.
Boiler conversion must be carried out by a
qualified company (e.g. After-Sales Technical
Assistance Service).
To convert to another type of gas the following
operations are required:
- remove the voltage from the appliance;
- replace the main burner injectors, making sure
to insert the special seal rings supplied in the
kit, between the gas manifold and the injectors;
- apply voltage to the appliance;
- select using the boiler key, the gas parameter
type (P1) and select (
nG
) in case of Methane
supply or (
LG
) in the case of LPG
select gas parameter type (P2) in the case of
G110 gas supply;
- adjust the boiler nominal heat output;
- adjust the boiler nominal heat output in dome-
stic hot water phase;
- adjust the boiler nominal heat output in heating
phase;
- adjust (if necessary) the boiler maximum heat
output in heating phase;
- seal the gas flow rate regulation devices (if
settings are modified);
- after completing conversion, apply the sticker,
present in the conversion kit, near to the data-
plate. Using an indelible marker pen, cancel the
data relative to the old type of gas.
These adjustments must be made with reference
to the type of gas used, following that given in
the table (parag. 3.17).
Summary of Contents for Nike Star 24 4 ErP
Page 18: ...18 3 4 3 2 2 4 1 INSTALLER USER MAINTENANCE TECHNICIAN ...
Page 27: ...27 ...