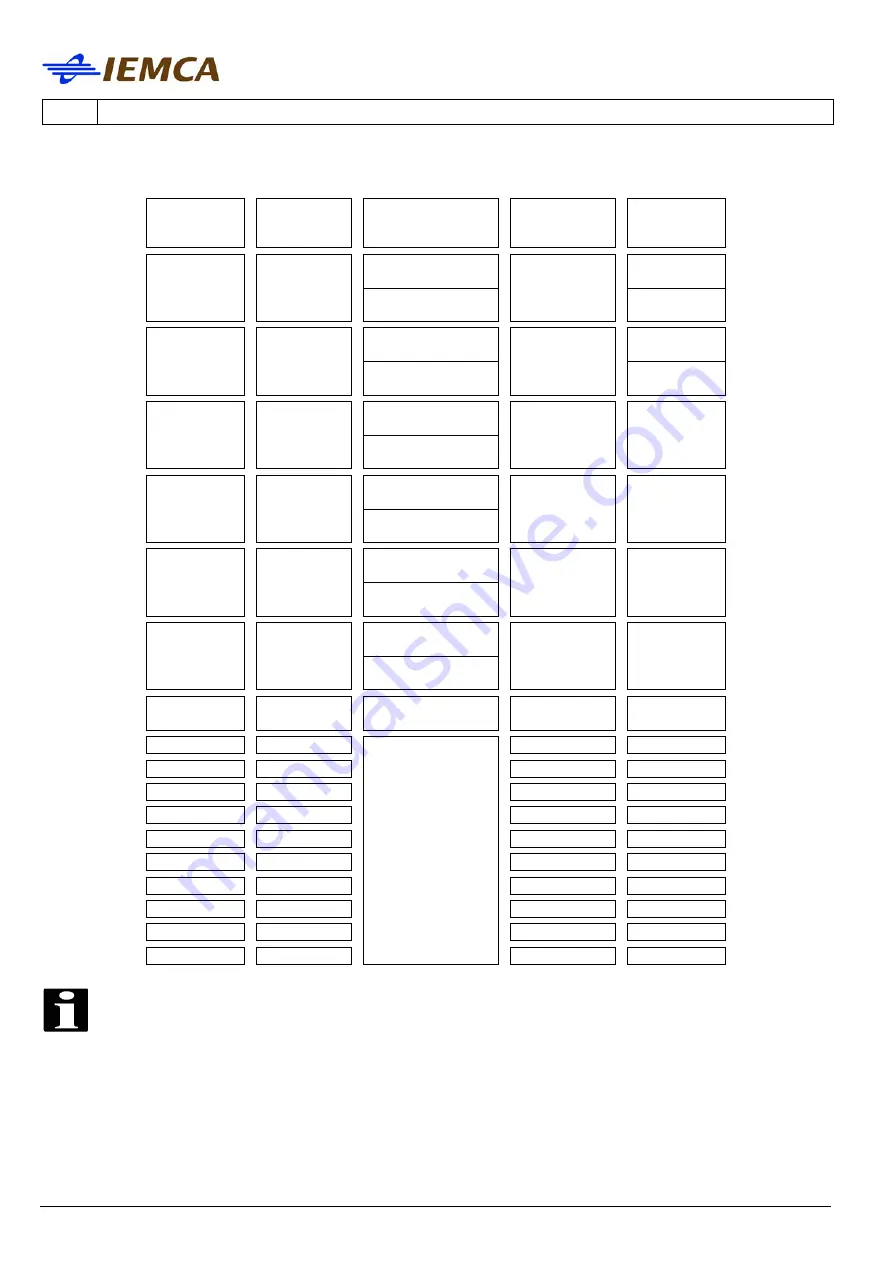
EN
10 - GUIDE CHANNELS-BAR PUSHER-REVOLVING TIPSMASTER 880/880r VERSO
10 - Pag. 4 / 12
øB
(mm)
Guide channel
diameter
øC
(mm)
Bar pusher
diameter
Collet version
– D
(type of coupling)
øGR
(mm)
Revolving tip
diameter
Revolving tip
code
21
20
Threaded (IEMCA)
20
D71152010
With quick coupling
pin
D71152011
26
25
Threaded (IEMCA)
25
D71152510
With quick coupling
pin
D71152511
33
32
Threaded (IEMCA)
32
D70153210
With quick coupling
pin
36
35
Threaded
(IEMCA)
35
D70153510
With quick coupling
pin
38
37
Threaded
(IEMCA)
37
D70153710
With quick coupling
pin
43
42
Threaded(IEMCA)
42
D70154210
With quick coupling
pin
46
45
Threaded (IEMCA)
45
D70154510
52 51
With quick coupling
pin(IEMCA) With
quick coupling
screw(IEMCA)
Threaded
“OPTIONAL”
51
D77155110
57 56
56
D77155610
61 60
60
D77156000
66 65
65
D77156500
69 68
68
D77156800
71 70
70
D77157000
73 72
72
D77157200
76 75
75
D77157500
81 80
80
D77158000
86 85
85
D77158500
IMPORTANT: the single components of the bar pusher and revolving tips are
showed in the spare parts catalogue.
Summary of Contents for MASTER 880-VERSO P
Page 2: ......
Page 4: ......
Page 16: ......
Page 26: ...EN 2 TECHNICAL INFORMATION MASTER 880 880r VERSO 2 Pag 10 34...
Page 41: ...2 TECHNICAL INFORMATION MASTER 880 880r VERSO EN 2 Pag 25 34 2 6 TECHNICAL DATA...
Page 64: ......
Page 120: ......
Page 144: ......
Page 145: ...7 MASTER 880 880r VERSO EN 7 Pag 1 9 INDEX 7 1 2 7 2 3 7 2 1 4 7 2 2 5 7 2 3 6 7 2 4 7 7 3 8...
Page 146: ...EN 7 MASTER 880 880r VERSO 7 Pag 2 9 7 1...
Page 148: ...EN 7 MASTER 880 880r VERSO 7 Pag 4 9 7 2 1 6 A B C CKB 150...
Page 149: ...7 MASTER 880 880r VERSO EN 7 Pag 5 9 7 2 2 A B C CKB 150 80...
Page 150: ...EN 7 MASTER 880 880r VERSO 7 Pag 6 9 7 2 3 6 A B...
Page 151: ...7 MASTER 880 880r VERSO EN 7 Pag 7 9 7 2 4 A B C 4 5 D 0 D...
Page 152: ...EN 7 MASTER 880 880r VERSO 7 Pag 8 9 7 3 MASTER 880 P...
Page 153: ...7 MASTER 880 880r VERSO EN 7 Pag 9 9 MASTER 880 F...
Page 154: ......
Page 156: ...EN 8 TROUBLES CAUSES CURES MASTER 880 880r VERSO 8 Pag 2 4...