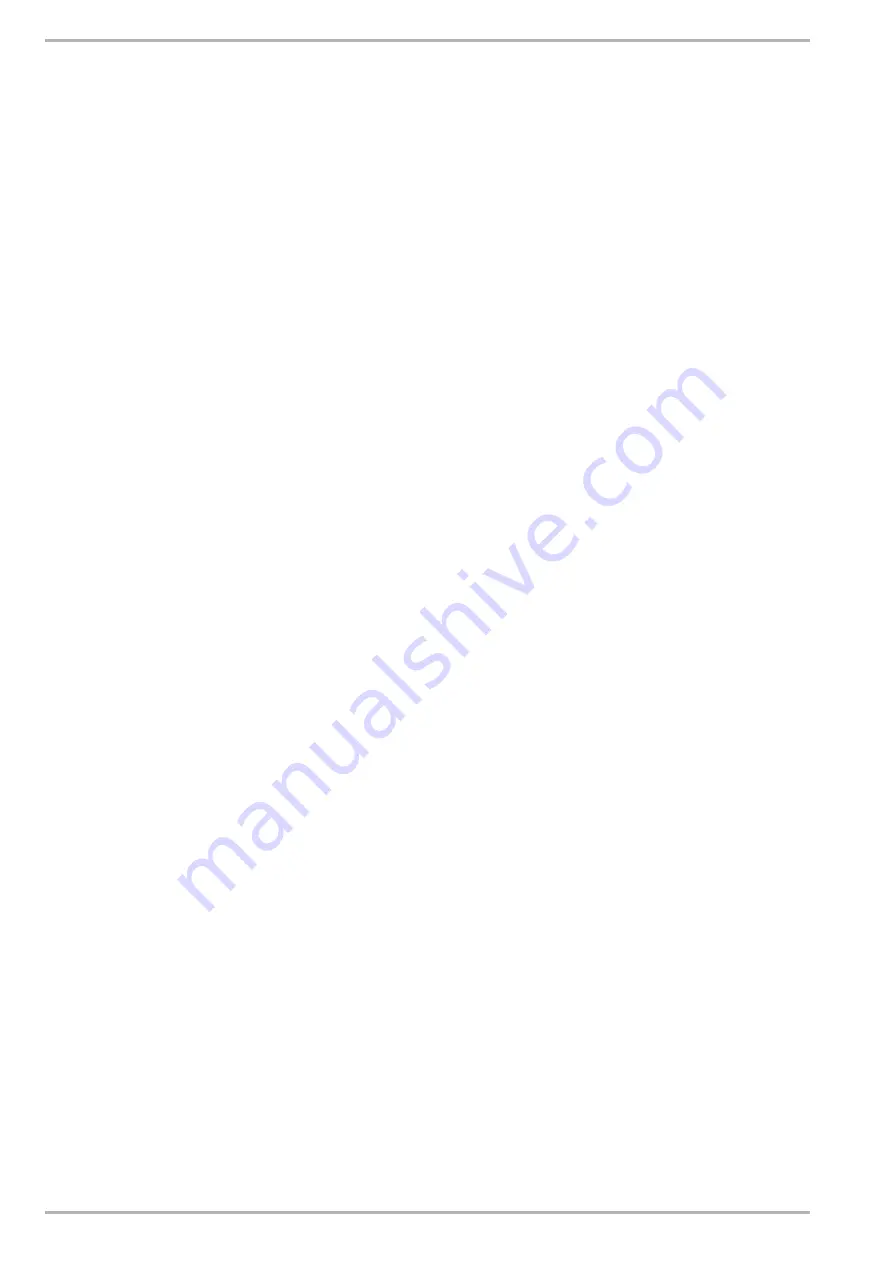
26 / 74
00U07352250-A_ EN
AHP60
26/32 kW -
Installation, Use and Maintenance
• Make sure that the passage of hydraulic connections is possible and easy, especially in the
case of several heat pumps.
• The outdoor unit is weatherproof, but avoid installing it in a place where it may be exposed to
dirt or heavy water run-off (under a leaking gutter, under a roof, etc.). Avoid installing the unit in
places where water is likely to stagnate or fall, for example from gutters
• The outdoor unit must be raised by at least 50 mm from the ground. Avoid places where snow
can accumulate (e.g. corners of buildings with sloping roofs). If the unit is to be installed in areas
prone to snowfall, it should be raised by at least 20 cm and at most 150 cm (depending on the
average snowfall in the area) to prevent snow from accumulating around the machine.
• During operation, water (due to the condensation of the water contained in the air) is discharged
from the outdoor unit. If the unit is installed on a terrace where there is a risk of frost, a connection
for the condensate drainage is required.
If the appliance is installed in a region where the temperature may fall below 0 °C for long
periods, fit the drain hose with a trace heater to prevent it from icing over.
•
If a water trap is installed, check the efficiency of the condensate drain and provide a trace of
the trap.
• Nothing should obstruct the air from circulating through the evaporator and out of the fan.
• The site where the unit is installed must be free of foliage, dust, etc., which could obstruct or
cover the heat exchanger.
• Ensure that the appliance does not disturb neighbours or users (noise level, draughts caused,
low temperature of the air blown causing a risk of freezing plants in its path).
• Exterior installation on a roof or in an open parking ramp is possible (contact the Pre-Sales
Department).
• It is advisable to create a support slab of suitable size for the unit. The units transmit a low level
of vibration to the ground. However, it is advisable to install anti-vibration mounts between the
base frame and the supporting surface. In the case of a suspended installation, it is necessary
to ensure that the wall is constructed of solid brick, concrete, or other material of equivalent
characteristics. The wall must be designed to support at least four times (4x) the weight of
the unit. Similarly, the supporting surface must be designed to support the weight of the unit.
This weight is indicated on the technical label affixed to the machine, and in this manual in the
chapter "technical specifications". The support surface must not be inclined in order to ensure
the operation of the refrigerant circuit and to avoid tilting of the unit.
• The installation surface of the unit must not be smooth, to avoid water/ice deposits, which can
be dangerous.
• Provide a gutter or condensate drain.
• The presence of cavities such as pits, manholes, building entrances, or sloping roofs, in which
refrigerant could accumulate in case of leakage and generate an explosive atmosphere, must
be avoided for at least 5 m around the unit.
• It is very important to avoid recirculation between suction and discharge, otherwise the
performance of the unit will deteriorate or even interrupt normal operation.
• In the case of a cascade of heat pumps, it is forbidden to place the fan of one unit facing the
evaporator (air inlet) of another unit.