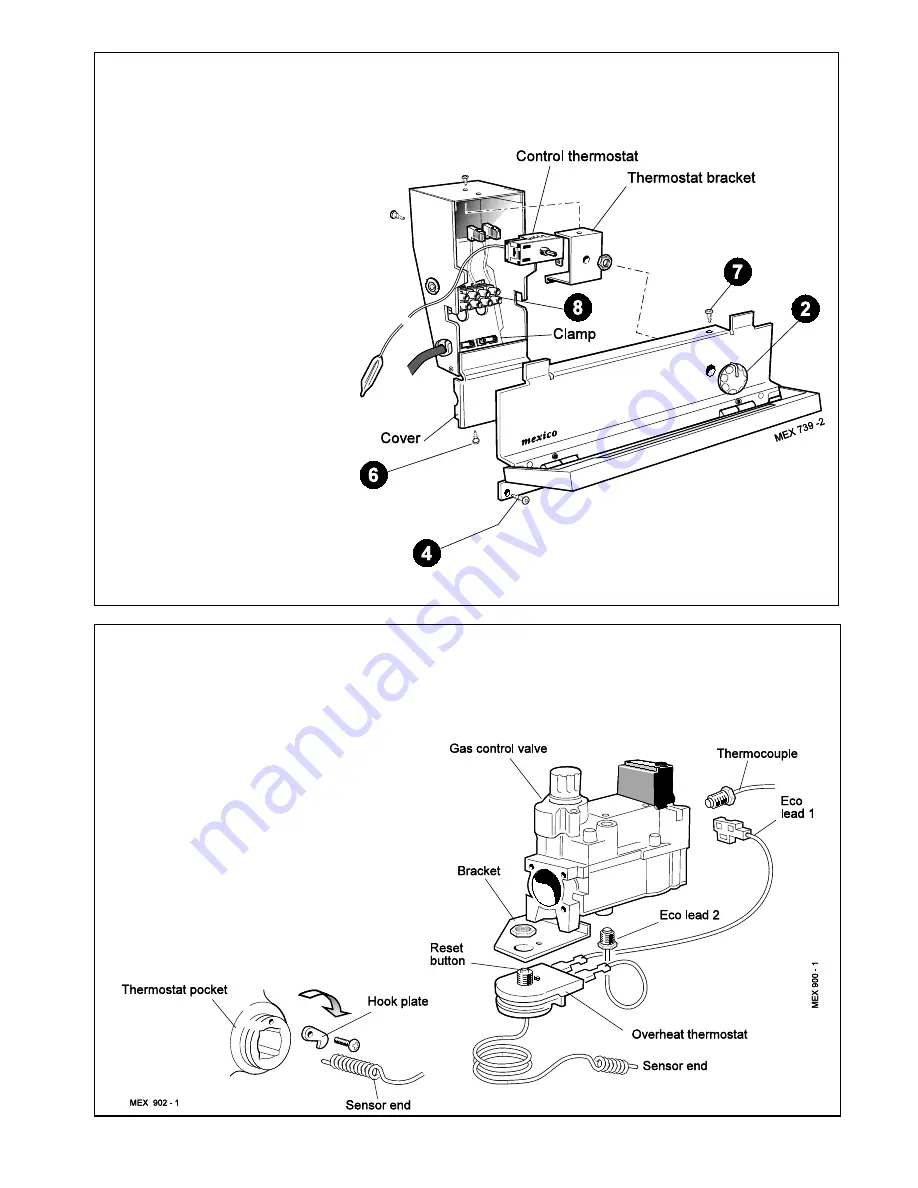
25
Mexico Super RS 3/60P - 3/100P -
Installation
SERVICING
1.
Lift off the lower front panel. Refer Frame 30
2.
Pull off the thermostat knob.
3.
Disconnect the electrical connections
from the gas valve.
4.
Unscrew the 2 screws and pull down the
control panel so that the 2 tabs clear the
top panel.
5.
Remove the thermostat phial from the
pocket. Refer to Frame 30.
6.
Remove the bottom screw and remove
the cover from the control box.
7.
Remove the top screw and ease the
control box off the control panel.
8.
Disconnect the mains electrical supply
from the terminal strip and release from
its clamp.
9.
Assemble new control box and panel
and fit to the casing reverse order.
10.
Insert control thermostat phial into
pocket and secure with the split pin.
11.
Connect gas valve electrical leads.
12.
Remove control box cover and make
electrical supply connections to the
terminal strip. Refer to frame 17.
13.
Replace front lower panel.
42 CONTROLS PANEL REPLACEMENT
43 OVERHEAT THERMOSTAT REPLACEMENT (if fitted)
1.
Lift off front lower panel. Refer to Frame 30.
2.
Slacken the screw at the thermostat pocket and withdraw
the phial from the pocket.
3.
Remove the thermostat backnut.
4.
Remove the 2 Eco leads.
5.
Fit the new thermostat (lead polarity immaterial),
ensuring that the alignment peg on the thermostat
sits in the small hole adjacent to the main fixing hole
and reassemble in reverse order.
6.
Replace the lower front panel.
7.
Check the operation of the boiler.