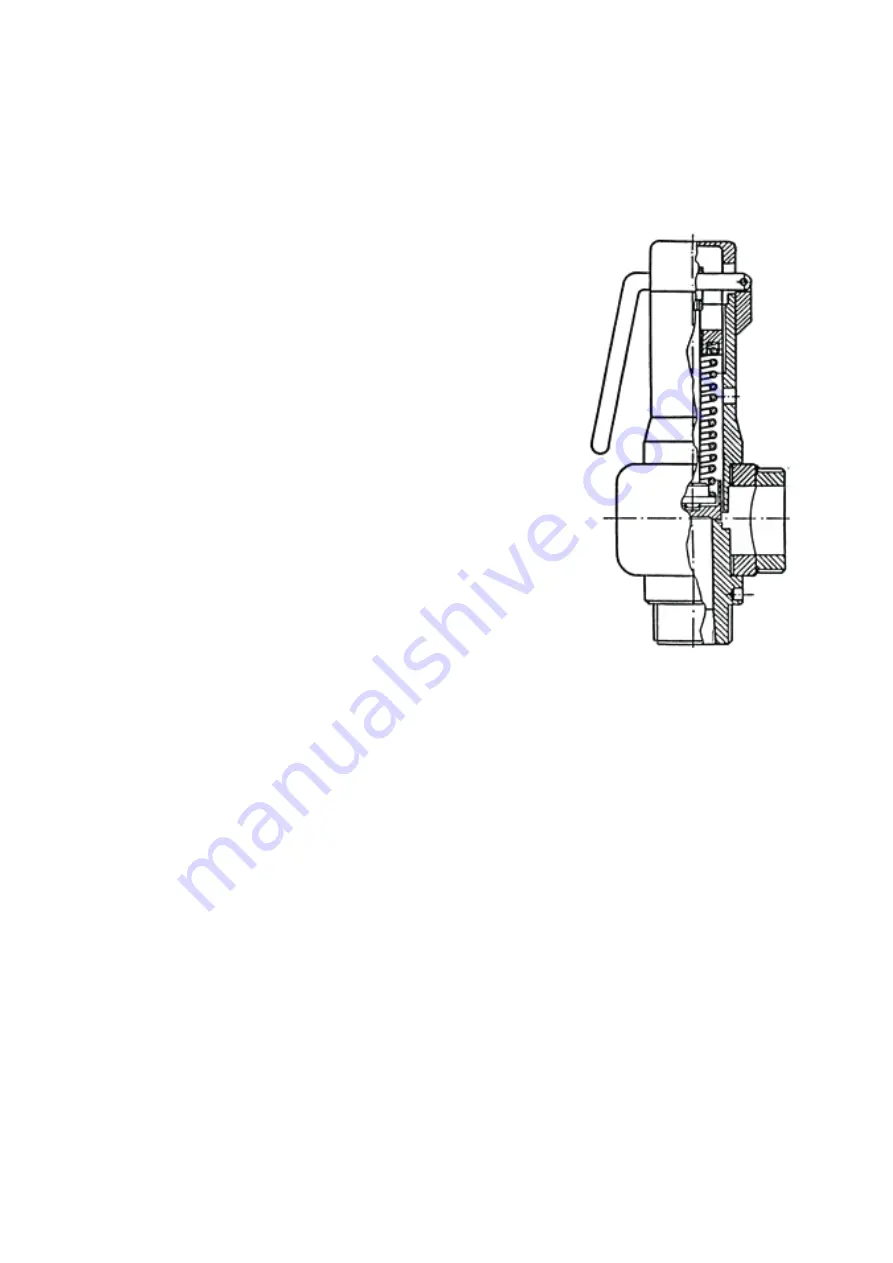
General information
15
SAFETY VALVE
It releases the steam when generator maximum design pressure is reached.
The valve used on boilers is of the spring-type.
The operator must pay the utmost attention to the safety valve, careful and accurate maintenance is important. The safety valve
is the most important and delicate accessory of the generator, and ensures that the pressure in the generator never exceeds the
design pressure.
As the safety valve never trips during boiler normal operation, it is good practice to make sure it is not jammed, i.e. that the shutter
is not stuck to its seat, by working the side lever (spring valve) or the horizontal lever that is holding the load (load valve and lever)
until steam starts to come out.
ATTENTION
Upon first start-up, check that safety valve is calibrated at generator design
pressure. The spring-type safety valve is usually supplied already calibrated. The
drain of the safety valve installed on generators must be conveyed outside the
room. When preparing the drain pipes, specific recommendations should be
considered; a few examples are listed below.
–
We recommend preparing the drain pipes using pipes having a diameter at
least equal to safety valve output flange diameter.
–
Drain pipe curves shall have a wide radius.
–
All drain pipes must be laid out so as to avoid any condensate build-up. This
means that they must be suitably slanted to ensure full drainage.
Special care should be taken when grinding the shutter and the seat; should this
be necessary because of leakage or sweating, make sure to use silicon carbide
or carborundum based abrasive agents and oil. It is recommended to carry out
a first grinding pass using a fine-grained abrasive agent and then a second pass
using a very fine-grained abrasive agent.
LEVEL
LEVEL INDICATOR
The level indicator includes a set of two taps connected to a reflex box that contains a prismatic glass. This equipment is connected
to the boiler above and below normal water level, while at its lower end it features a blowdown tap used to discharge the sludge
and keep the glass clean. The efficiency of the level control system can be periodically inspected using these taps as follows:
Open the blowdown valve for a few seconds and then close it. If no water is there and it then goes quickly back to the previous
point with wide oscillations, you can consider the level to work fine. While if water comes again slowly or stops at a different point
than before, it means that one of the communications is obstructed. To check which one of the two is obstructed and try to blow
it down, close the steam valve and leave the water one open, then open again the blowdown valve: water should drain out of
it together with any sludge built up in the pipes. Close the water valve and open the steam one: steam should come out of the
blowdown. Close the blowdown valve and leave the water and steam ones open: water should go back to the starting point. If
that is not so, clean the pipes connecting the level indicator to the generator. During commissioning, make sure that the vent and
drain are closed. During operation, shut-off valves must be fully open.
To reduce the possibility of leakage, the indicators must be periodically insulated to make sure that the tightening torque of the
nuts and bolts is at least 30 Nm.
Do not proceed with maintenance without having firstly checked that:
–
pressure in the generator is not equal to the atmospheric pressure.
–
The indicator temperature is equal to the environment temperature.
Maintenance must be carried out when:
–
The sight glass clearness partially deteriorates, it is partially matt, marks of internal roughness due to erosion or corrosion,
entailing loss of proper geometry and difficult reading.
–
There are leaks, even slight, through the seals or shut-off units
Cooke Industries - Phone: +64 9 579 2185 Email: [email protected] Web: www.cookeindustries.co.nz