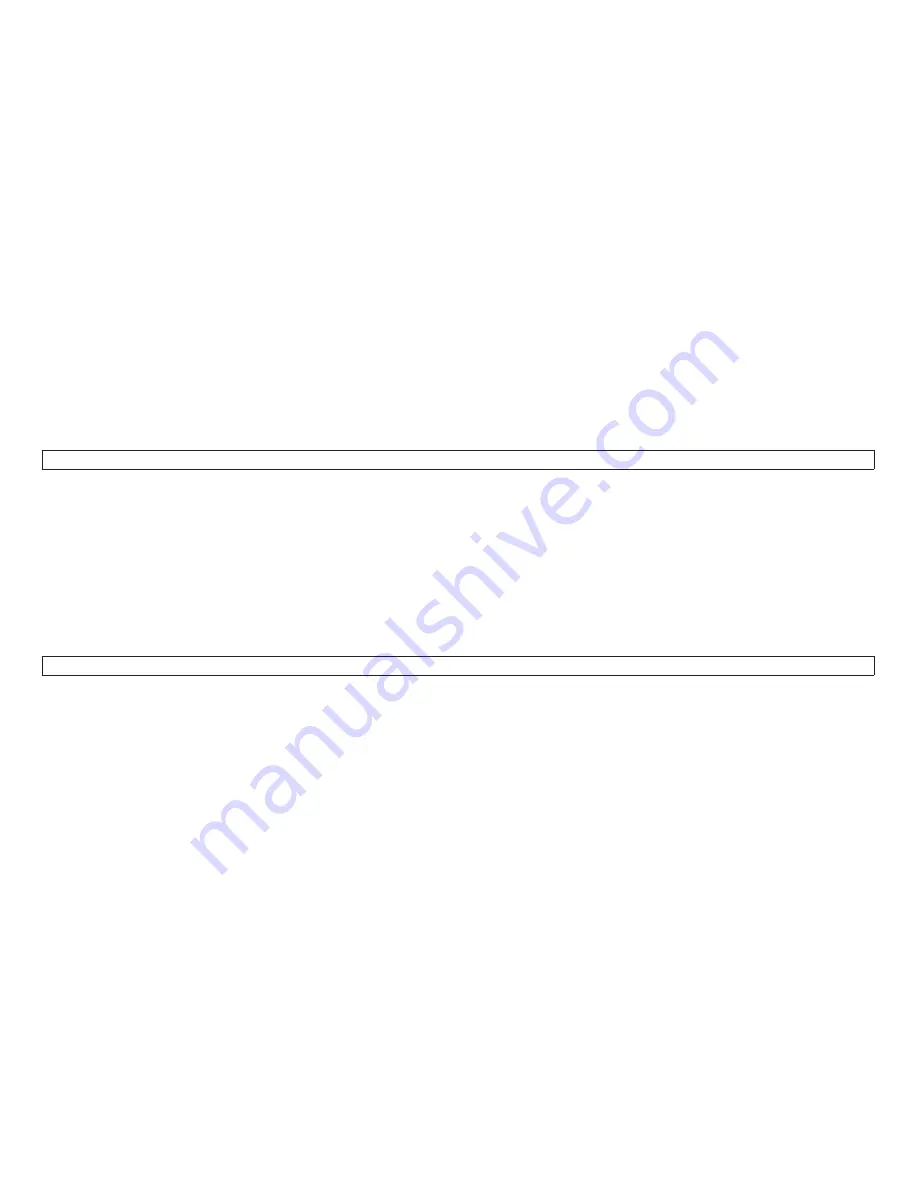
Note: The message TEST RUNNING will display during the test.
If an error message is displayed, go to T&D error messages and actions. The test completed successfully if the
display advances to the next test number.
T&D34—Adapter board static RAM test
This test checks the attachment card SRAM.
Display:
T&D34 Adapter Board Static RAM Test RUN TEST ? YES END NO
Note: The message TEST RUNNING will display during the test.
If an error message is displayed, go to T&D error messages and actions. The test completed successfully if the
display advances to the next test number.
T&D35—Adapter board shared RAM test
This test checks the attachment card shared RAM.
Display:
T&D35 Adapter Board Shared RAM Test RUN TEST ? YES END NO
Note: The message TEST RUNNING will display during the test.
If an error message is displayed, go to T&D error messages and actions. The test completed successfully if the
display advances to the next test number.
T&D36—Adapter board BCP test
This test checks the attachment card Biphase Communications Processor (BCP).
Chapter 2. Diagnostics
124
Summary of Contents for V03
Page 24: ...Reference table 8 ribbon lift and 26 pin cable connectors 93 Chapter 1 Diagnosing problems 24...
Page 138: ...Operator panel cable wiring Chapter 3 Wiring diagrams 138...
Page 144: ...Tractor assembly cable wiring Chapter 3 Wiring diagrams 144...
Page 164: ...Chapter 5 Removals service checks and adjustments 164...
Page 173: ...Table 24 Print quality sample 1 2 3 Chapter 5 Removals service checks and adjustments 173...
Page 246: ...Assemblies Chapter 6 Parts catalog 246...
Page 307: ...Taiwanese EMC Notices 307...
Page 310: ...Index Copyright IBM Corp 2002 310...
Page 311: ...IBMR Part Number 75P1301 Printed in U S A G544 5873 00 1P P N 75P1301...