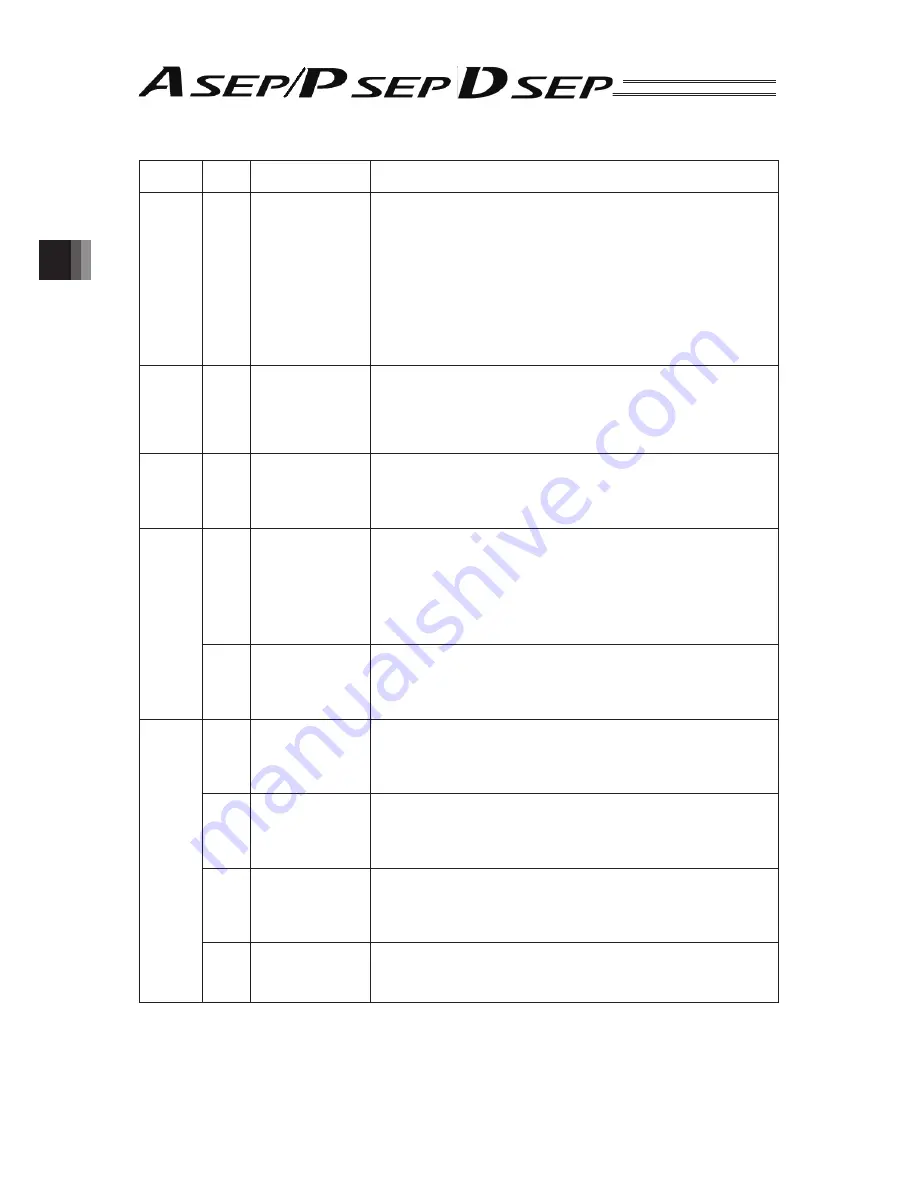
72
/
3. Operation
Error
Level
Code
Alarm Name
Cause/Treatment
Operation
Cancellation
0C1
Servo-Motor Error
The motor operation is not available for 2 seconds or more after the movement command is
received and before the actuator reaches the target position.
Cause :
(1)
A looseness in the connection section of the actuator connecting cable or wire
breakage is considered.
(2) In the case of the unit with the brake, the brake is not released.
(3) The motor load might be too large due to the external force.
(4) The sliding resistance in the actuator itself might be too large.
Treatment : (1) and (2) Check for the actuator connecting cable wiring condition.
(3)
Con
fi
rm that there is no error in the mechanical part assembly condition.
(4)
In the case that the load weight is normal, move the actuator by hand to check
the sliding resistance after the power is turned OFF. In the case that there is any
error in the actuator itself, contact our company.
Cold Start
0C8
Overcurrent
Cause :
The output current in the power circuit section is increased abnormally. The motor
coil insulation degradation might be considered.
Treatment :
Measure the resistance between the motor connecting cable U, V and W and
insulation resistance with earth cable and con
fi
rm whether or not there is insulation
degradation.
When the measurement is performed, consult with our company.
Operation
Cancellation
0C9
Overvoltage
An over-voltage is caused in the 24V input power (24V
20%: 28.8V or more).
Cause
: (1) The source voltage in the 24V power unit is too high.
(2) A breakdown of the part inside the controller is considered.
Treatment : Check for the input source voltage.
In the case that the voltage is normal, contact our company.
Cold Start
0CA
Overheat
Cause
: (1) The temperature inside the controller is too high. (95
C or more)
(2)
When the actuator is vertically installed, in the case that the deceleration setting
is too high when it is moved downward, the regenerative resistance energy
might be insuf
fi
cient.
(3) The defective part inside the controller is considered.
Treatment : (1) Lower the surrounding temperature around the controller.
(2)
Review the setting conditions so that the deceleration curve becomes linear.
In the case that the cause is not applicable to (1) or (2), contact our company.
0CB
Current Sensor Offset
Adjustment Error
An error is found in the current detection sensor in the initialization in the start-up operation.
Cause :
(1)
A breakdown of the current detection sensor or peripheral component is
supposed.
(2) An error in the offset adjustment is supposed.
Treatment : A work (PC board) change or offset adjustment is required. Contact our company.
Operation
Cancellation
0CC
Control Power Source
Voltage Error
An over-voltage is caused in the 24V input power (24V
20%: 28.8V or more).
Cause
: (1) The source voltage in the 24V power unit is too high.
(2) A breakdown of the part inside the controller is considered.
Treatment : Check for the input source voltage.
In the case that the voltage is normal, contact our company.
0CE
Control Power Source
Voltage Drop
The source voltage from the 24V power unit is decreased (24V
20%: 19.2V or less).
Cause
: (1) The source voltage from the 24V power unit is too low.
(2) A breakdown of the part inside the controller is considered.
Treatment : Check for the input source voltage.
In the case that the voltage is normal, contact our company.
0D2
Motor Power Source
Voltage Excessive
An over-voltage is caused in the motor power source (24V
20%: 38V or more).
Cause
: (1) The source voltage in the 24V power unit is too high.
(2) A breakdown of the part inside the controller is considered.
Treatment : Check for the input source voltage.
In the case that the voltage is normal, contact our company.
0D8
De
fl
ection Over
fl
ow
The position deviation counter is over
fl
own.
Cause
: The velocity might be lowered in the movement operation due to an external force.
Treatment :
Con
fi
rm about the load conditions, that the work does not interfere with any object
nearby or the brake has been released, etc., and if any, remove the cause.
Summary of Contents for ASEP
Page 1: ...DSEP Controller ASEP Controller PSEP Controller Instruction Manual Tenth Edition ...
Page 2: ......
Page 4: ... ...
Page 115: ......