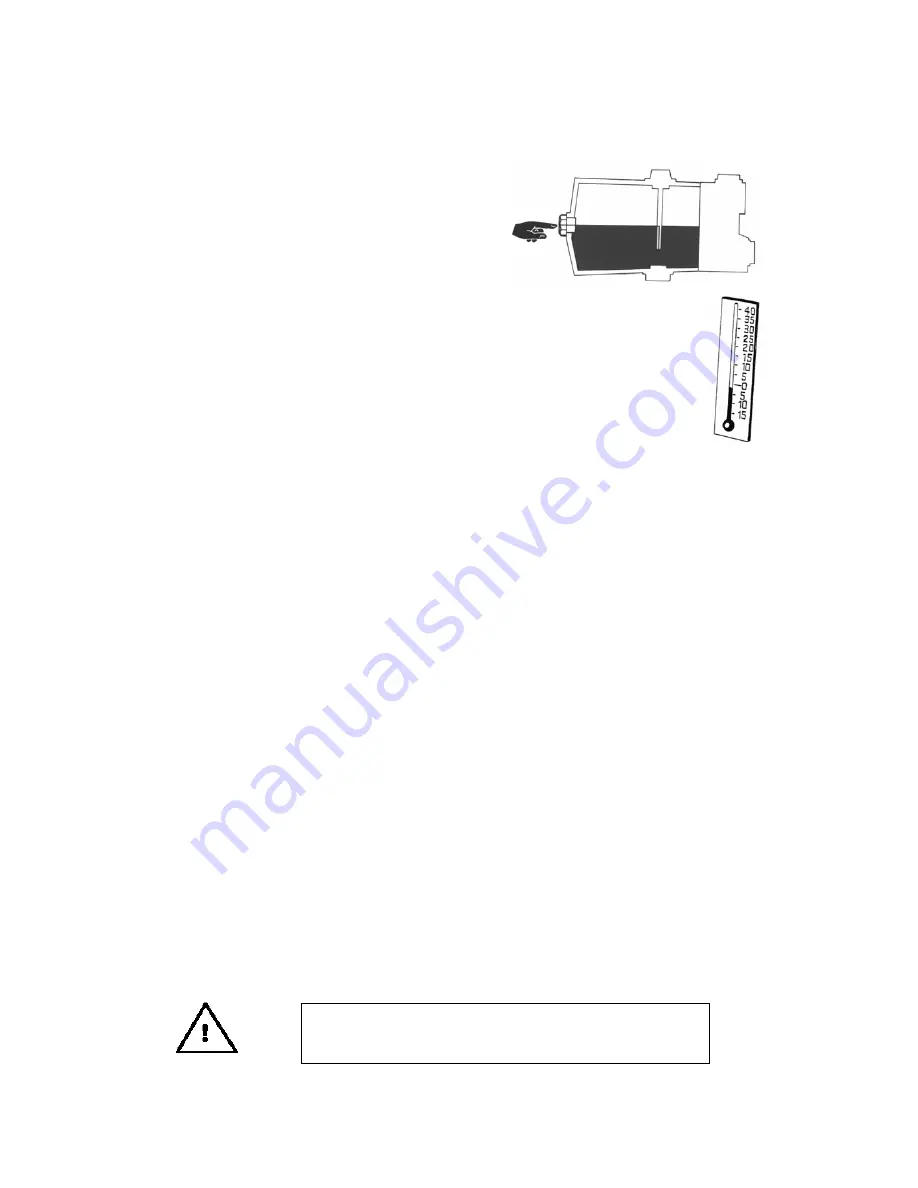
1)
The pump oil level should be regularly checked; it must always be above the marker. Change
the oil after 50 working hours, and successively every 500 hours; use oil type SAE 20/30. To
check the oil level, unscrew the grips and lift the cover vertically upwards.
Now check that the oil level inside the high-pressure
pump is at least half of the oil inspection hole of the
pump (or unscrew the oil cap and check that the oil
level is above the minimum marker). If the quantity of
oil is not enough, do not start the machine.
2)
Do not leave the pump exposed to very low temperatures as it may freeze.
Stopping the machine at temperatures below 0°C can cause damage or breakage to
the pump and hoses; it is therefore advisable to drain them completely and intake a
small quantity of antifreeze for the winter period. Conversely, very high temperatures
can cause the motor to overheat when the machine is operating.
DAMAGE CAUSED BY FREEZE ARE NOT COVERED BY WARRANTY
3)
When the pump is not used for a long period of time, scale may form and make
instant start of the electric motor difficult. In this case, to avoid anomalous current
absorption with consequent voltage drop, we advise moving the driving shaft by using
a screwdriver before starting the motor (
Important:
this must be done when the machine is not
connected to the power supply). This will let you check why the motor jammed (if caused by
frost, scale, or anything else) and take appropriate measures.
4)
Never intake corrosive liquids (paints, acids, solvents, oily or very thick liquids), which could
permanently damage the pump. To avoid chemical deposits building up, we suggest intaking
clean water.
5)
The cleaning of the boiler must be done each 200 working hours as follows:
- disassemble the nozzle and the electrode-holder flange (burner head)
- clean the nozzle filter using compressed air and check the position of the electrodes
- take away the boiler cover and clean the baffle
- remove the inside cover
- unscrew the locking nuts of the coil and take it off from boiler
- clean the coil using a wire brush
- suck the residue from the boiler
- reassemble the cleaner proceeding in the reverse order
- the total check and the combustion regulation must be regularly carried out by specialized
personnel as provided for by current regulations
6)
Descaling must be regularly done by using specific products according to the water
hardness. In a water can of about 15 litres, pour one litre of scale preventer type “TM KAL” or
“TM COILS” following the instructions provided on the package.
Use a can with tap, connect the tap to the water supply of the cleaner (Fig. 4).
Keep the can in such a way so that the scale preventer flows out.
Take the gun off from the high-pressure hose, put the other end of the hose inside the can to
create a closed circuit and let the cleaner intake the scale preventer for at least 10 minutes.
We advise the delivery hose discharge inside a small cloth bag to avoid intaking the scale taken
away. Restore the normal connection and rinse with cold water.
This operation should be carried out by our technical support because the scale preventer could
damage the components.
For the disposal of the scale preventer, observe the current regulations.
CAUTION:
the scale preventer/scaler contains acid
substances, which could damage the objects to be cleaned.
Make sure you have correctly rinsed the cleaner.
Page 13
Summary of Contents for HYW10200
Page 1: ...ELECTRIC HOT WATER PRESSURE WASHER Models HYW11120 HYW10200 HYW13170 3 User Manual ...
Page 17: ...MX STANDARD SINGLE PHASE WIRING DIAGRAM Page 17 ...
Page 18: ...MX STANDARD THREE PHASE WIRING DIAGRAM Page 18 ...
Page 19: ...MC STANDARD THREE PHASE WIRING DIAGRAM Page 19 ...
Page 20: ...MX STANDARD SINGLE PHASE WIRING DIAGRAM Page 20 ...