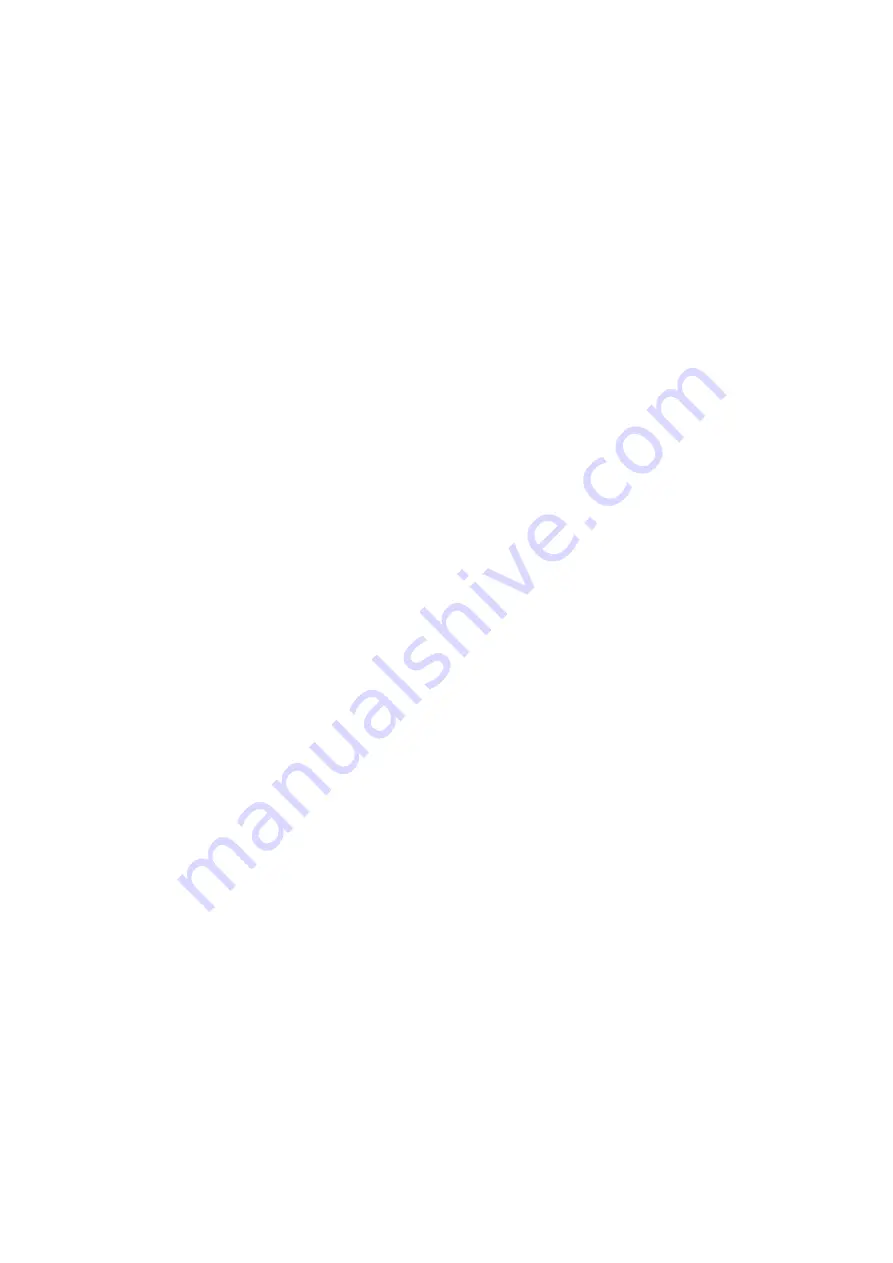
1-4
Thoroughly clean the machine. In particular, be careful to clean the filler caps, grease fittings and the
area around the dipsticks. Be careful not to let any dirt or dust into the system.
Always use HYUNDAI Forklift genuine parts for replacement.
Always use the grades of grease and oil recommended by HYUNDAI Forklift.
Choose the viscosity specified for the ambient temperature.
Always use pure oil or grease, and be sure to use clean containers.
When checking or changing the oil, do it in a place free of dust, and prevent any dirt from getting into
the oil.
Before draining the oil, warm it up to a temperature of 30 to 40
。
C.
After replacing oil, filter element or strainer, bleed the air from circuit.
When the strainer is located in the oil filler, the strainer must not be removed while adding oil.
When changing the oil filter, check the drained oil and filter for any signs of excessive metal particles
or other foreign materials.
When removing parts containing O-ring, gaskets or seals, clean the mounting surface and replace
with new sealing parts.
After injecting grease, always wipe off the oil grease that was forced out.
Do not handle electrical equipment while wearing wet places, as this can cause electric shock.
During maintenance do not allow any unauthorized person to stand near the machine.
Be sure you fully understand the contents of the operation. It is important to prepare necessary tools
and parts and to keep the operating area clean.
When checking an open gear case there is a risk of dropping things in. Before removing the covers to
inspect such cases, empty everything from your pockets. Be particularly careful to remove wrenches
and nuts.
Way to use dipstick
Push the dipstick fully into the guide, and then pull out.
Carrying out other difficult maintenance work carelessly can cause unexpected accidents. If you
consider the maintenance is too difficult, always request the HYUNDAI Forklift distributor to carry out
it.
·
·
·
·
·
·
·
·
·
·
·
·
·
·
·
·
Summary of Contents for 20G-7
Page 1: ......
Page 2: ......
Page 3: ......
Page 6: ......
Page 41: ...2 7 Mast Refer to the chapter 1 MAST Page 2 2 1 2 POWER TRAIN ASSEMBLY REMOVAL 1 D503RE04 ...
Page 59: ...3 7 OPERATING MODES Forward INPUT OUTPUT 4 1 INPUT OUTPUT 20D7PT29 20D7PT30 Reverse 2 ...
Page 231: ...7 3 FUEL SYSTEM CIRCUIT TIER 3 LPG 20L7EL07 ...
Page 232: ...7 4 FUEL SYSTEM CIRCUIT TIER 3 BI FUEL 20L7EL06 ...
Page 233: ...7 5 FUEL SYSTEM CIRCUIT NON CERT LPG 20L7EL08 ...
Page 234: ...7 6 FUEL SYSTEM CIRCUIT NON CERT BI FUEL 20L7EL09 ...
Page 235: ...7 7 MEMORANDUM ...
Page 267: ...MODEL L4GC SHOP MANUAL FOR INDUSTRIAL USE ...
Page 284: ...GENERAL 2 1 GENERAL OUTLINE L4GC001A ...
Page 285: ...GENERAL 2 2 L4GC002A ...
Page 346: ...LUBRICATION SYSTEM 2 63 4 Front case Oil pump 5 Timing belt 6 Timing belt cover ...
Page 390: ...3 21 5 Loosen 4 through bolts L4GC330A L4GC048A 6 Separate the rotor and cover CHARGINGSYSTEM ...
Page 402: ...1 GENERAL 4 1 2 INJECTOR 4 14 4 PVC VALVE 4 16 CHAPTER 4 FULE SYSTEM AND OTHER ...
Page 420: ......