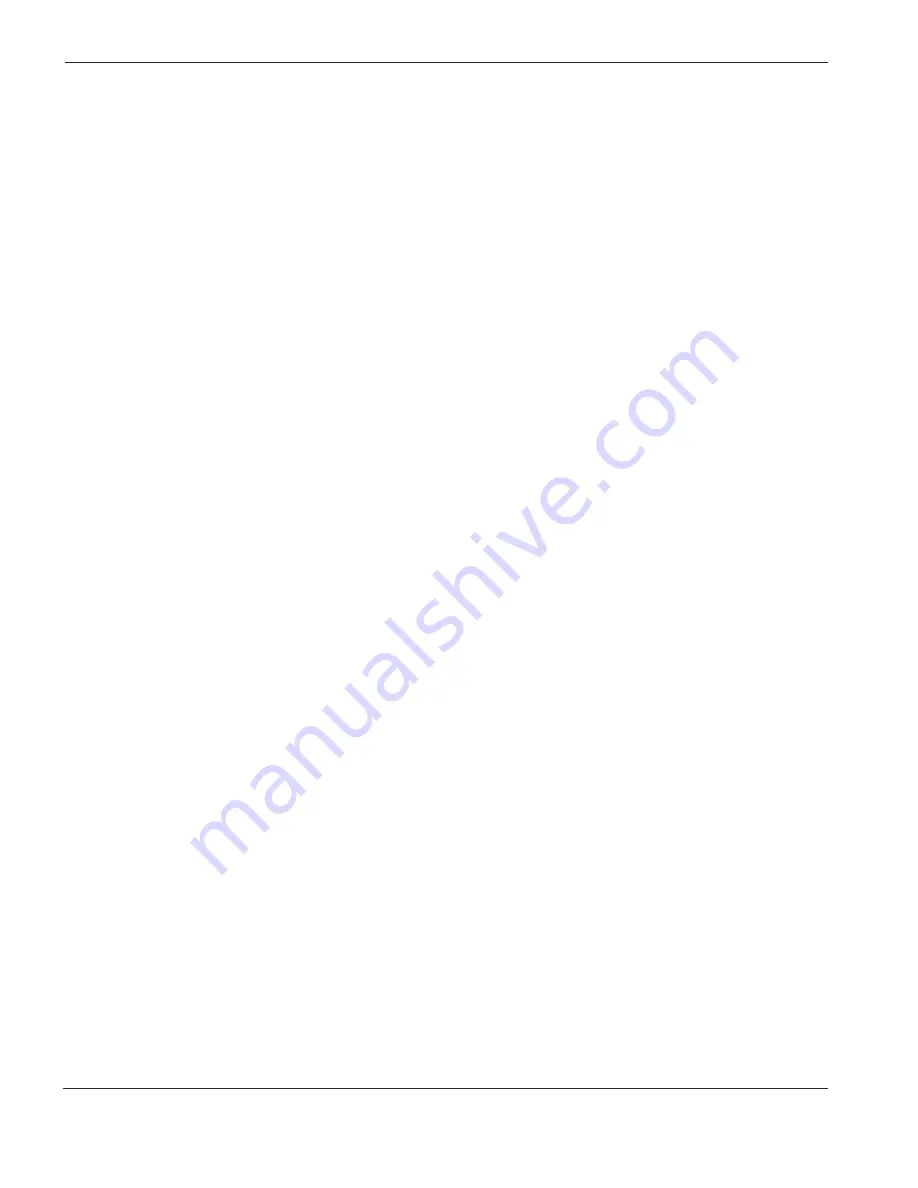
Maintenance
5-44
HPR400XD Auto Gas –
806160
leak test 2 (system leak test)
Purpose: Tests for leaks to the atmosphere from the gas system.
Test description: The gas for the process selected is purged through the gas system. The metering console valves
(B1-B4), and the inlet valves (for the selected process) in the selection console are closed. Gas
pressure is now trapped in the system. The trapped pressure is monitored. Code number 14 (cut gas
channel number 1 failed) or 15 (cut gas channel number 2 failed) will be displayed if the pressure
drops faster than 0.14 bar/minute (2 psi/minute). Code number 13 will be displayed if the pressure
decreases within the acceptable limit of 0.14 bar/minute (2 psi/minute).
Procedure:
1. Perform System Leak Check on the CNC controller.
2. Turn OFF power and then turn ON power. This will purge gases from the system.
leak test 3 (proportional valve test in the metering console)
Purpose: Tests the Burkert valves (B1 and B3) in the metering console to ensure that they are working within the
correct parameters.
Test description: 130-amp mild steel consumables, and the 30-amp O
2
/O
2
mild steel process are used for this test,
because there is a known flow rate.
Gas flows from the torch, and the Burkert valve that controls the plasma gas channel (B3) attempts to
maintain the set plasma gas pressure (monitored by P7 and P8) by adjusting the valve dynamically. The
signal percentage to the valve is measured (example – 65% on), and the value is checked against the
expected range (55% – 75%). The test is successful if the signal percentage is within the expected
range. Code number 14 (shield gas channel failed) or 15 (plasma gas channel failed) will be displayed
if the test fails. The same test is repeated for the Burkert valve that controls the shield gas channel
(B1).
For the next part of the test, the Burkert valve that controls the plasma gas channel (B3) is closed, and
the pressure is measured milliseconds later (pressure should decrease). The test is successful if the
pressure is below a given limit (0.69 bar [10 psi]). The same test is repeated on the shield gas channel
(B1).
Code number 16 (plasma ramp-down test failed) or 17 (shield rampdown test failed) will be displayed
if the signal percentage is out of the expected range. Code number 13 (test passed) will be displayed
if the signal percentage is within the expected range.
Procedure:
1. Install 130-amp mild steel consumables in the torch and select the 30-amp O
2
/O
2
mild steel process.
2. Perform Metering Valve Flow Check on the CNC controller (test 3).
3. Turn OFF the power and then turn ON the power. This will purge gases from the system.
Summary of Contents for HyPerformance HPR400XD
Page 1: ...HyPerformance Plasma HPR400XD Auto gas Instruction manual 806160 Revision 4 ...
Page 26: ...Specifications 2 2 HPR400XD Auto Gas 806160 ...
Page 48: ...Installation 3 10 HPR400XD Auto Gas 806160 ...
Page 53: ...Installation HPR400XD Auto Gas 806160 3 15 Horizontal RHF mounting Vertical RHF mounting ...
Page 57: ...Installation HPR400XD Auto Gas 806160 3 19 This page is blank intentionally ...
Page 65: ...Installation HPR400XD Auto Gas 806160 3 27 7 8 8 7 ...
Page 100: ...Installation 3 62 HPR400XD Auto Gas 806160 ...
Page 107: ...Operation HPR400XD Auto Gas 806160 4 7 Diagnostic screen ...
Page 108: ...Operation 4 8 HPR400XD Auto Gas 806160 Test screen ...
Page 109: ...Operation HPR400XD Auto Gas 806160 4 9 Cut chart screen ...
Page 197: ...Operation HPR400XD Auto Gas 806160 4 97 ...
Page 287: ...7 4 HPR400XD Auto Gas 806160 Discrete output functionality ...
Page 347: ...Appendix B CNC Interface Protocol b 28 HPR400XD Auto Gas 806160 ...
Page 355: ...4 HPR400XD Auto Gas 806160 ...