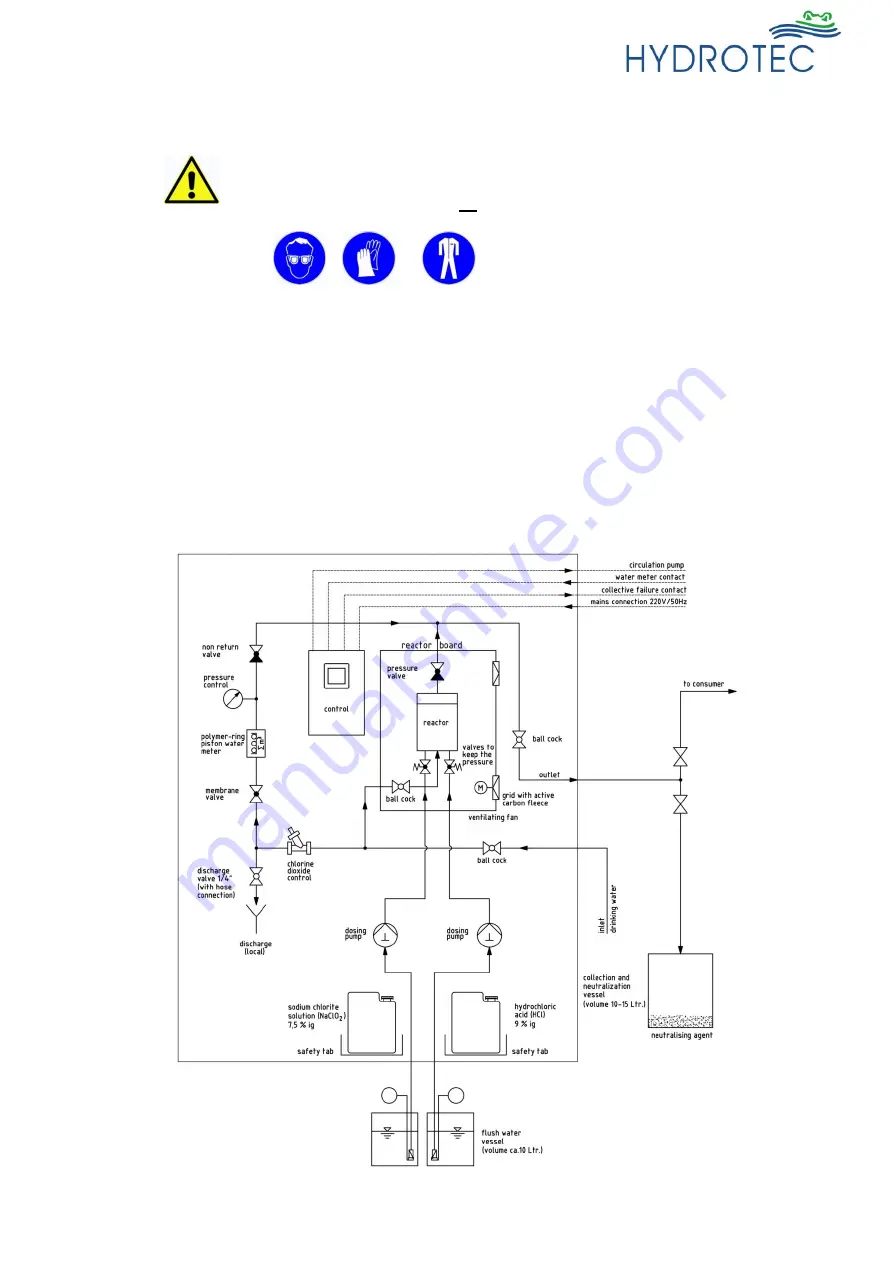
I-79/103
Last change 04/2016 E-P – AL/TW/PW | Subject to technical modifications
5. Putting out of operation / Flushing of chlorine dioxide production plant
Caution!
Protective clothing as per the actual valid accident prevention
rules has to be worn for all work at the plant!
5.1 Short-term operational interruption
No special measurements are required for short-term operational interruptions of ca. 1 to 2 hours!
- The plant must be
switched off with button “OFF”, LED “FAILURE” lights.
- The emergency-off-button must be set to
“OFF”.
Restart as per point 2.8. The dosing pumps must be de-aired on request!
5.2 Flushing of plant
The plant must be flushed carefully with water if put out of operation for a longer time period or prior
to plant opening for maintenance work.