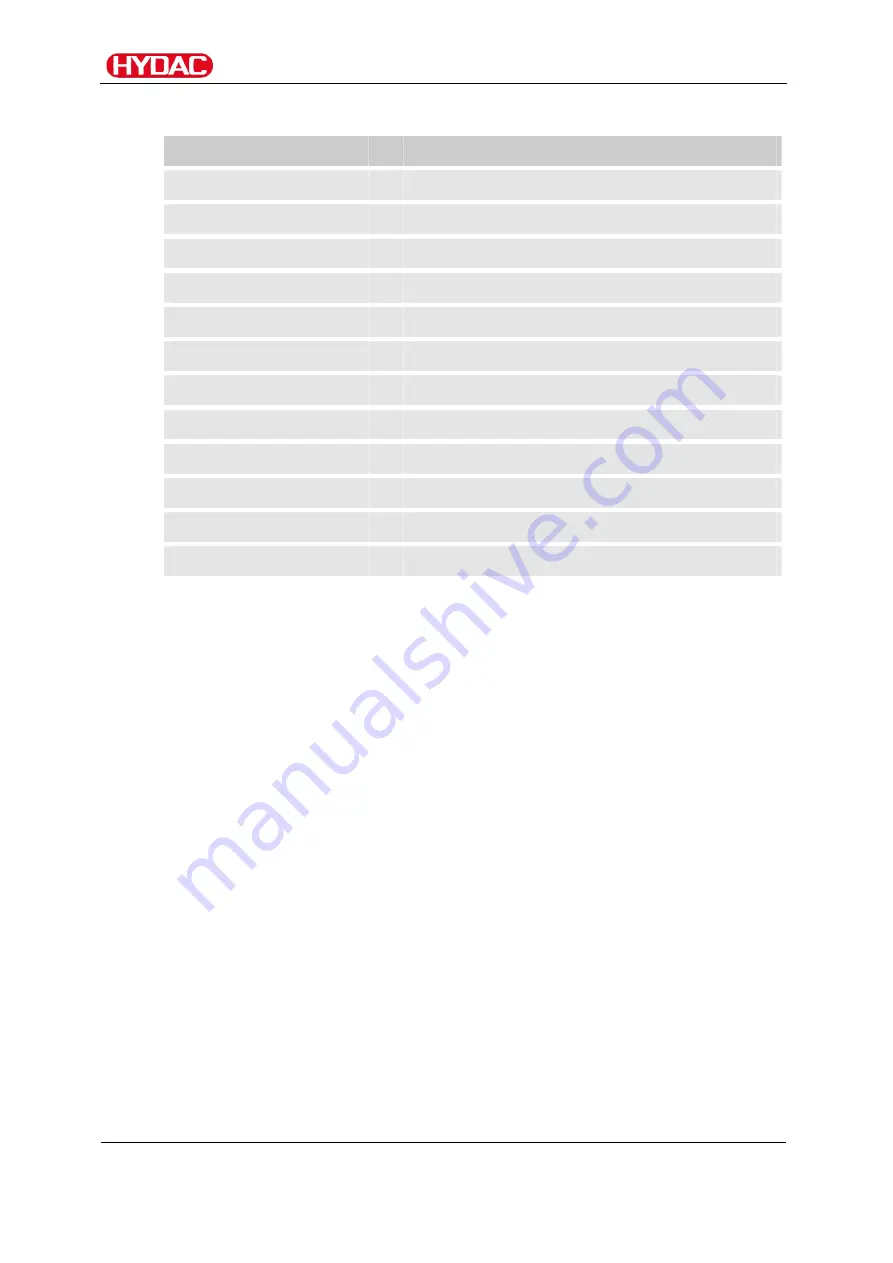
Decoding the name plate
LVU-CD-10
en(us)
Page 17 / 52
BeWa LVU-CD-10 Eco 4067271 en-us 2016-01-08.doc
2016-01-08
The following information can be found on the name plate of the unit:
Row
-> Description
Part No.
-> Part number
S/N
-> Serial number / year of production
Power
-> Power consumption
Voltage/Grid
-> Voltage / power supply
Frequency
-> Frequency
Current
-> Current consumption
Pressure max.
-> Operating pressure, maximum
Weight
-> Weight when empty
Flow rate
-> Flow rate
Temp. Fluid
-> Permitted fluid temperature range
Temp. Amb.
-> Permissible ambient temperature range
Volume
-> Fluid volume in unit
Summary of Contents for LVU-CD-10
Page 51: ......