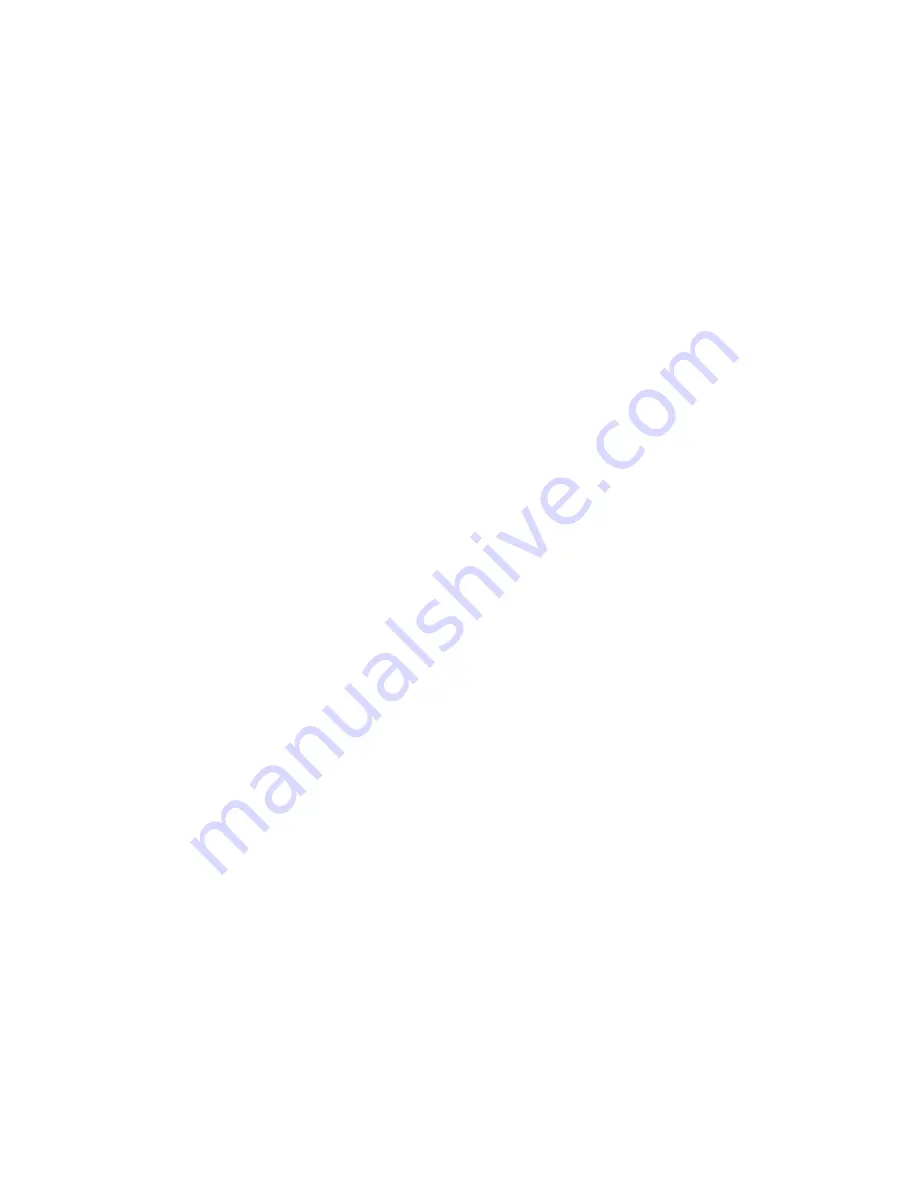
5-4
M
aintenance
P/N 0518258_D
U.S. & Canada 1-800-922-1919 • Mexico 1-800-890-2900 • WWW.HUSSMANN.COM
CLEANING COILS
NEVER USE SHARP OBJECTS AROUND
COILS. Use a soft brush or vacuum brush to
clean debris from coils. Do not puncture coils!
Do not bend fins. Contact an authorized
service technician if a coil is punctured,
cracked, or otherwise damaged.
ICE
in or on the coil indicates the refrigeration
and defrost cycle is not operating properly.
Contact an authorized service technician to
determine the cause of icing and to make
adjustments as necesssary. To maintain
product integrity, move all product to a cooler
until the unit has returned to normal
operating temperatures.
Do NOT use chlorine or ammonia-based
cleaners to clean aluminum coils.
CLEANING UNDER MERCHANDISERS
Remove splashguards not sealed to floor.
Use a vacuum with a long wand attachment
to remove accumulated dust and debris from
under the merchandiser.
REMOVING SCRATCHES FROM BUMPER
Most scratches and dings can be removed
using the following procedure.
•Use steel wool to smooth out the surface area
of the bumper.
•Clean area.
•Apply vinyl or car wax and polish surface for
a smooth glossy finish.
MAINTAINING FLUORESCENT LAMPS
Fluorescent lamps should not be allowed to
run to failure. If a re-lamp schedule is not in
place, the tubes should be inspected for signs
of degradation (blackened ends). Degraded or
failed tubes should be replaced.
Allowing severly degraded lamps to operate
may cause a ballast failure or could expose
the lamp holder to excessive heat. Replacing
degraded bulbs is more cost effective than
replacing ballast and lamp-holders.
Traditional re-lamp programs are 18-to-24
month intervals. In the absence of a re-lamp
program, a yearly inspection of the lighting
system is recommended.
1. Inspect all lamp sockets and plug-receptacle
connections for signs of arching. Replace any
component that shows signs of arching.
2. Make sure all unused receptacles have their
close-off covers securely installed.
3. Make sure proper cleaning procedures are
followed. Lights and fans MUST be turned off
when a case is cleaned and MUST be allowed to
dry before turning power back on.
4. Do not use a pressure nozzle to clean inside
of case.