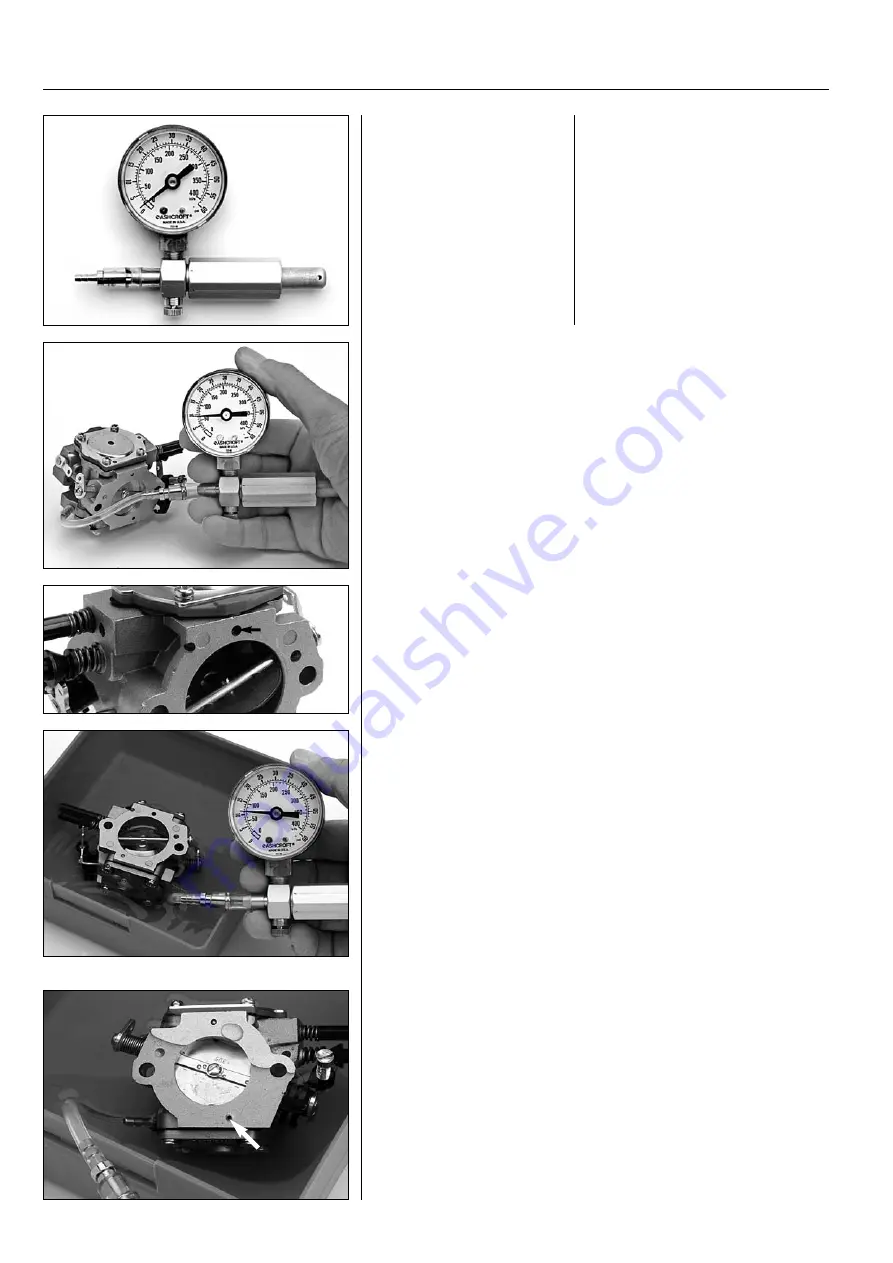
CARBURETTOR
11
25
Functional test
Pressure tester 501 56 27-01
The pressure tester has a pump piston
that is operated with one hand.
The pressure tester is supplied with an
adapter nipple for small sizes. Make the
hose connection to the nipple as short as
possible, this gives a clearer test result.
Functional test
Pressure tester
501 56 27-01
The pressure tester is sup plied
with an adapter nipple for small
sizes. Make the hose connection
as short as possible.
Leaking needle valve – indications
A leaking needle valve can be seen in numerous ways. A machine that is run
for short periods is often difficult to start when it is warm, fuel leaks into the
venturi and gives too much fuel for the next warm start. With a cold start,
especially when the machine has not been used for a long period, the fuel
chamber above the needle has been slowly emptied and fuel has evaporated.
First after several attempts to start, has new fuel been pumped forwards and
the machine starts.
Needle valve – testing
Reliable inspection of the needle valve's function demands certain conditions.
The clearest result is obtained from a carburettor that is drained of fuel, yet
still has some fuel residue. A completely “dry” carburettor, or a carburettor
that has not been used for a long time gives a measurement result that is diffi-
cult to interpret.
Connect a thin, short hose to the carburettor's fuel pipe. Pump up the
pressure to approximately 200 kPa and let the fuel run out through the venturi.
Not until air emerges from the venturi, can the function of the needle valve
be tested as set out below. If the needle valve does not open at 250 kPa (max.
permitted pressure test) the needle valve has jammed. This can usually be
forced open by blowing gently through the hole for filter compensation (A).
Test the needle valve's function as follows: Pump a pressure to 100–250 kPa,
the needle valve should then lift. The pressure should then drop to 100–50 kPa
and then drop significantly slower or stop completely. Pressure drop after
50 kPa indicates a leaking needle valve, or a leaking carburettor. Check that
the screws on the pump and measurement chamber covers are tightened.
Testing can also be performed with the carburettor assembled on the
machine. Drain the fuel from the carburettor by pressurising this repeatedly
before the measurement values are read.
Water bath
By immersing the carburettor in water, any external leakage can be checked
simultaneously with the function of the needle valve. Let the carburettor
remain in the water for as short a time as possible.
Connect the pressure tester to the fuel pipe. Pump up a pressure to
50–100 kPa and observe if air bubbles come from the carburettor.
Pump diaphragm
Connect the pressure tester to the fuel pipe. Place the carburettor in a water
bath and pump up pressure to a maximum of 250 kPa. If air comes out of the
impulse channel the pump diaphragm is leaking.
Measurement chamber diaphragm
The condition of the diaphragm cannot be checked by pressure measurement.
A punctured diaphragm results in air being sucked into the nozzle in the
venturi instead of fuel.
A