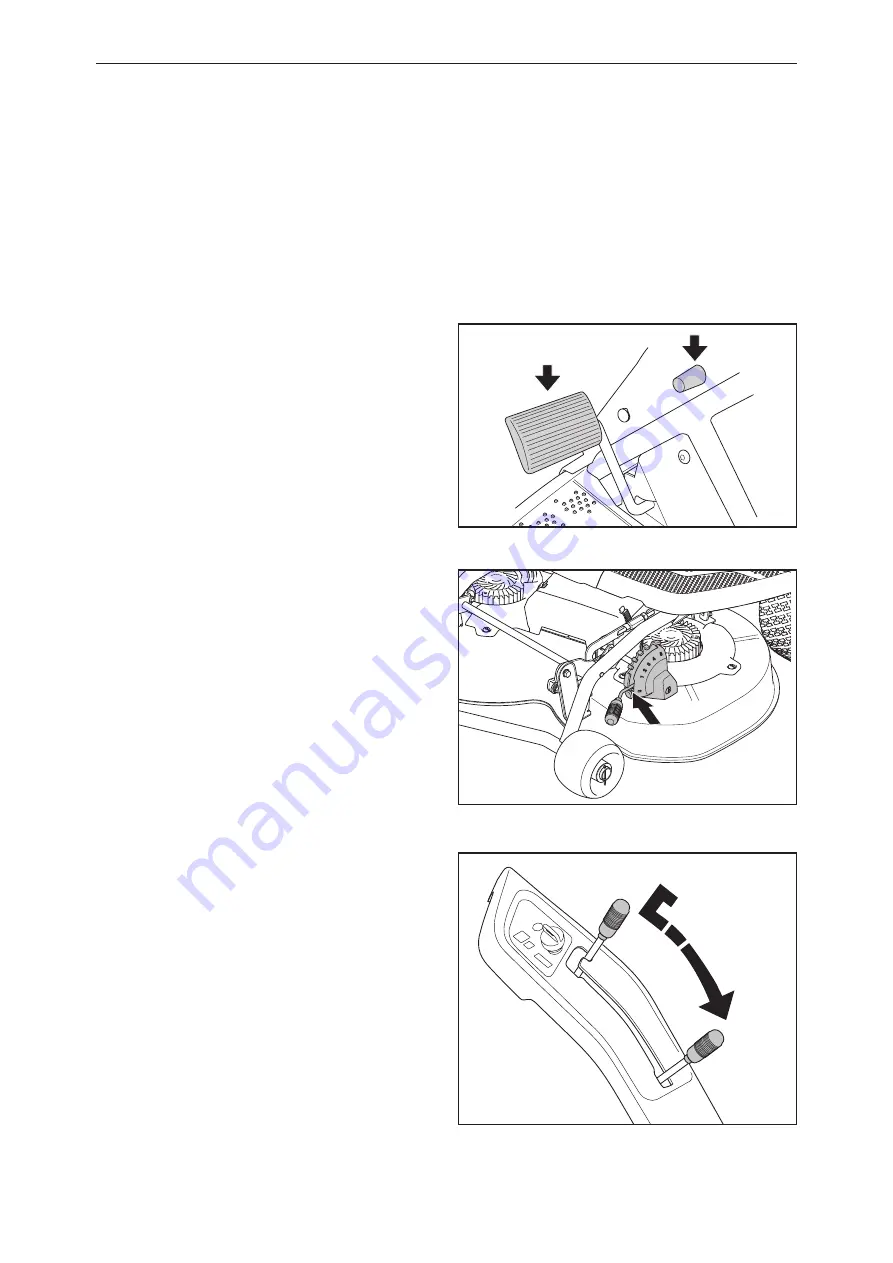
English –
29
Basic dismantle/assembly
6.6 Removing the Cutting Deck
To dismantle the cutting deck proceed as follows:
1
Put the machine in a level position.
2
Turn off the machine and remove the ignition key.
3
Apply and secure the parking brake.
4
Check that the lever for setting the cutting height is
in the S position.
5
Lower the cutting unit.
Summary of Contents for 967187001
Page 1: ...Workshop manual Rider Battery English ...
Page 2: ......
Page 28: ...English 28 6 5 Exploded View Drawing Cutting Deck Basic dismantle assembly ...
Page 62: ...Repair Work English 62 4 Assemble the new baffle plate 5 Refit the spring and contact ...
Page 143: ......
Page 144: ...2015W44 115 75 74 26 ...