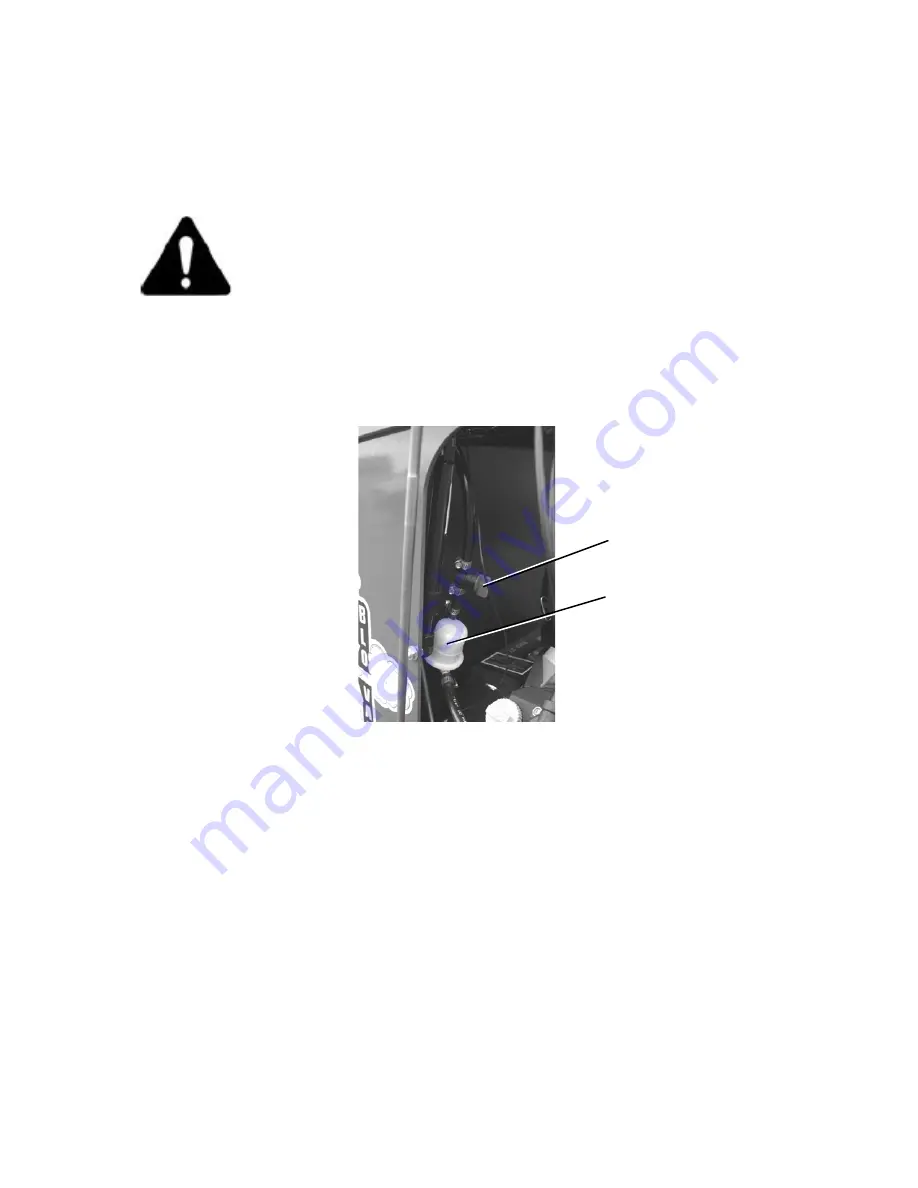
SERVICE
Service Engine
1. Park machine safely.
2. Allow engine to cool.
3. Turn OFF fuel shut off valve.
4. Loosen and slide hose clamps away from fuel filter.
5. Place drain pan under hoses to catch any fuel that may be left in the hoses.
6. Disconnect hoses from fuel filter.
7. Install new fuel filter by connecting hoses to new fuel filter. Make sure fuel
filter is installed in the proper direction.
8. Install hose clamps.
9. Turn ON fuel shut off valve.
10. Start engine and check for fuel leaks.
Replacing Fuel Filter
CAUTION: Avoid injury! Fuel vapors are explosive and
flammable:
• Shut off engine before servicing.
• Cool engine before servicing.
• Work in a well-ventilated area.
• Do not smoke while handling fuel.
• Keep fuel away from flames or sparks.
• Clean up spilled fuel immediately.
Fuel shut off
Fuel filter
28