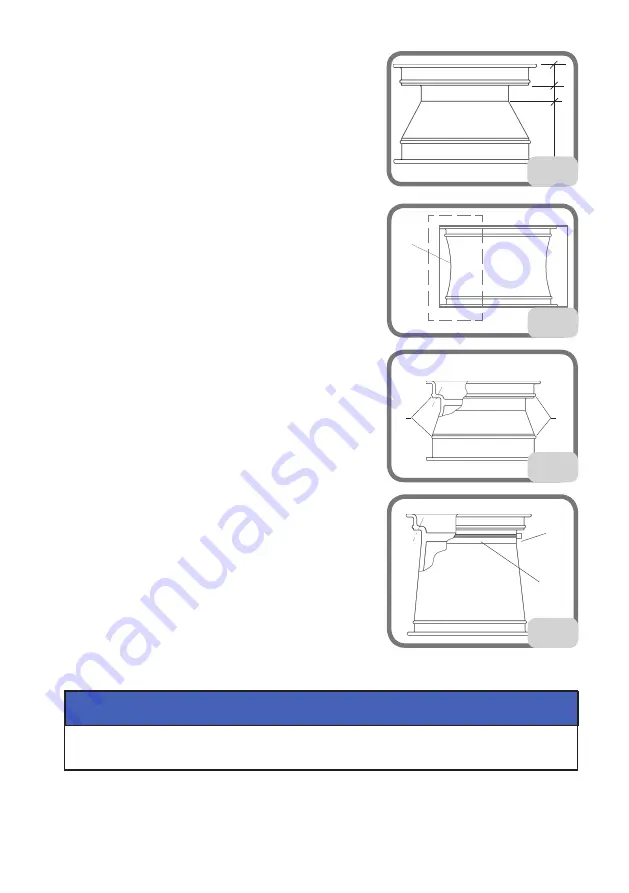
M 830 LL - M 830 M
User Manual
121
A
B
C
15c
6.2. DECIDING FROM WHICH SIDE
OF THE WHEEL THE TYRE MUST BE
DEMOUNTED
See Fig. 15. Find the position of rim well A on the
wheel rim. Find the largest width B and the smallest
width C. The tyre must be mounted and demounted
with the wheel on the turntable with the smallest width
side C facing upwards.
SPECIAL WHEELS
Alloy rim wheels:
some alloy rim wheels have minimal
rim wells A or no rim wells at all - Fig. 15a. These rims
are not approved by DOT (Department of Transporta-
tion) standards.
The initials DOT certify that tyres comply with the safety
standards adopted by the United States and Canada
(these wheels cannot be sold on these markets).
High-performance wheels (asymmetric curvature)
-
Fig. 15b: Some European wheels have rims with a very
pronounced curvature C, except in the area of the valve
hole A where the curvature is less pronounced B. On
these wheels the bead must first be broken in the area
of the valve hole, on both the top and bottom sides.
Wheels with pressure sensor
- Fig.15c. To operate cor-
rectly on these wheels and avoid damaging the sensor
(which is incorporated in the valve, fixed with the
belt, glued inside the tyre, etc.) appropriate mount-
ing/demounting procedures should be followed (ref.
Approved mounting/demounting procedure for runflat
and UHP tyres)
See the section “TABLE FOR USING CENTRING AND CLAMPING ACCESSORIES
ACCORDING TO RIM TYPE” in this manual.
NOTICE
A
B
C
15
A
15a
A
B
C
15b
Summary of Contents for M 830 LL
Page 37: ...M 830 LL M 830 M User Manual 123 A B C 1 2 D 17...
Page 38: ...124 M 830 LL M 830 M User Manual A B C D 1 2 2 18...
Page 49: ...M 830 LL M 830 M User Manual 135 1 2 3 4 30...
Page 76: ...162 M 830 LL M 830 M User Manual M13 M14 M11 M7 M2 M9 A M16 STANDARD RIM...
Page 77: ...M 830 LL M 830 M User Manual 163 M6 M5 M11 M7 M9 B M16 DROPPED CENTRE HOLE RIM...
Page 78: ...164 M 830 LL M 830 M User Manual C M11 M2 REVERSED RIM...
Page 79: ...M 830 LL M 830 M User Manual 165 D M10 M2 M15 M9 PICK UP RIM...
Page 80: ...166 M 830 LL M 830 M User Manual E CLOSED CENTRE RIM...
Page 81: ...M 830 LL M 830 M User Manual 167 F OPEN CENTRE RIM...
Page 84: ...170 M 830 LL M 830 M User Manual...
Page 85: ...M 830 LL M 830 M User Manual 171 49...