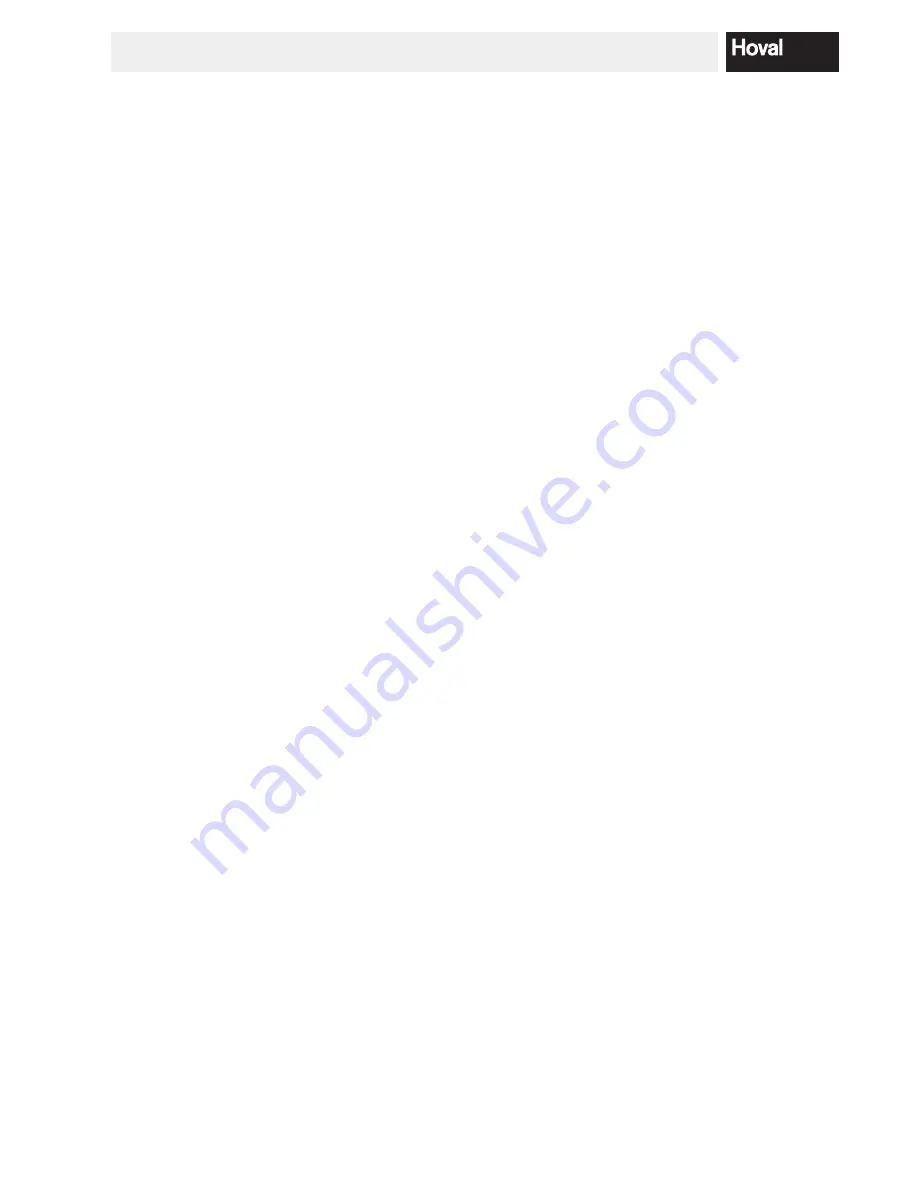
33
4 213 894 / 01
33
4 213 894 / 00
FAULTS
E 10 Flame stop during a heating demand
A locking will occur, when the ionisation flow sinks more
than 3 times under 1.5mA during a single heating de-
mand.
E 11
Flame message without reason
A locking will occur, when there is a flame without an
open gas valve.
E 12 Fan speed out of the limits
If the fan actual-speed is out of a range of the fan set-
speed for more than 15 seconds, a locking is occured. A
maximum variation is 20 % of the set value.
E 13 Parameter programming
After loading of a parameter from the laptop to the au
-
tomatic firing unit the boiler will be locked automatically.
After reseting the boiler can be used again.
E 14 Failure while loading parameters
A connection failure while loading of the parameters with
SITlab is occured. The progress needs to be repeated.
E 15 Internal fault in the automatic firing unit
E 16 Internal fault in the automatic firing unit
E 17 (Flow – Return) > 45K for 10 sec
If the difference between the flow temperature and return
temperature is higher than 45K for more than 10 seconds
during a heating demand, a locking is occurred.
E 18 Safety boundry thermostat (STB is not used!)
If the safety boundary thermostat is activated, a blo-
cking is demanded immediately. After 5 seconds this will
change into a locking.
E 19 Air pressure switch function devective (Air pres-
sure switch is not used!)
Control occurs before starting the burner while the pre-
ventilation phase (switch is closed) and while the fan is
standing still (switsch is open). If there is a failure a „5“
(air pressure switch is defective) appears on the display.
The period of this condition should only last maximum 5
minutes, afterwards a locking occurs.
Summary of Contents for TopGas 80
Page 36: ...36 4 213 894 01 ...
Page 37: ...37 4 213 894 01 ...