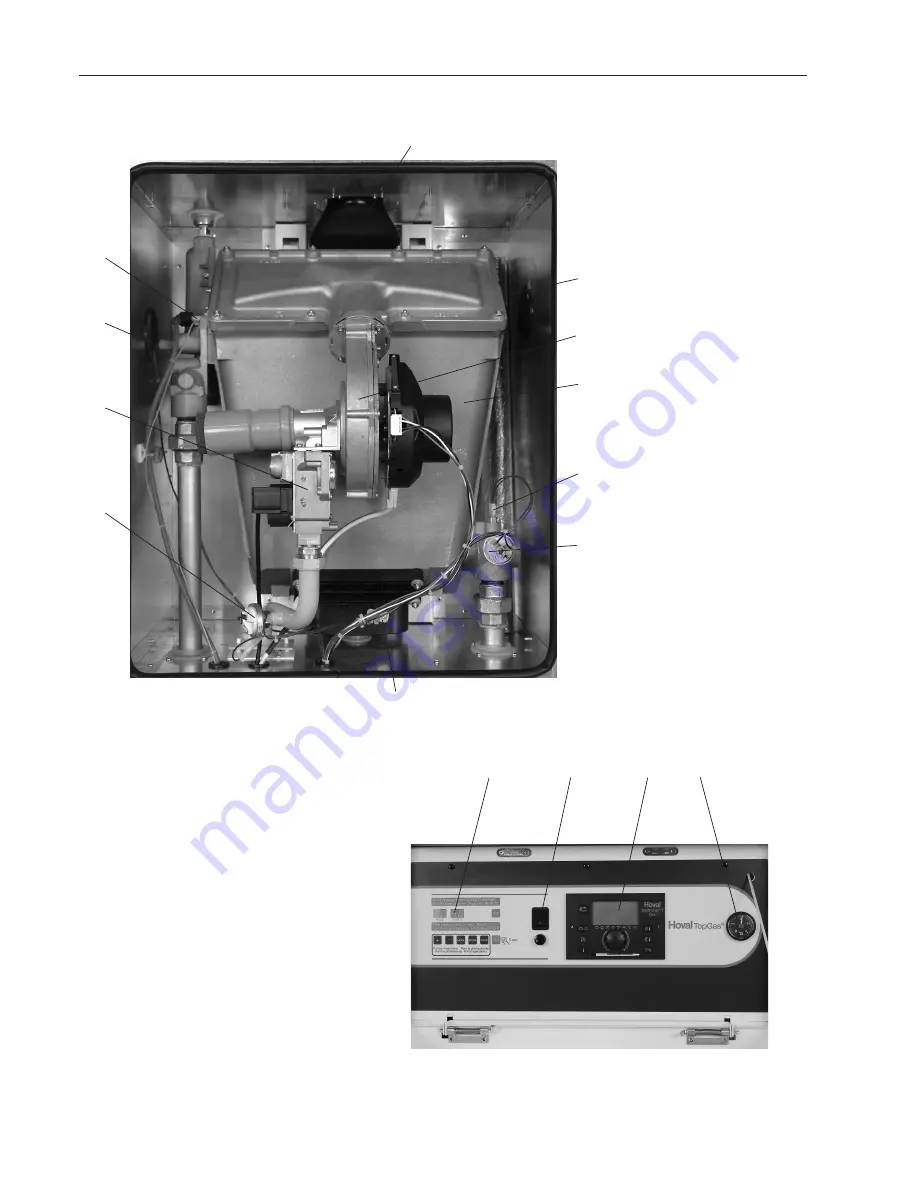
14
4 205 254 / 03
Installation
Picture 3.1.8-1
Picture 3.1.8-2
TopGas
3.1.8
®
component designation
13
14
12
15
1
2
4
7
5
9
3
10
8
11
6
1 Burner viewing window
2 Fan
3 Flue gas air inlet
4 Water pressure deflector
5 Flue gas temperature sensor
6 Flow temperature sensor
7 Return temperature sensor
8 Ignition/ionisation electrode
9 Heat exchanger
10 Gas fitting
11 Gas pressure deflector
12 ON/OFF deflector
13 Automatic firing unit control panel
14 TopTronic
®
control panel (optional)
15 Manometer
Summary of Contents for TopGas 30
Page 33: ...33 4 205 254 03...