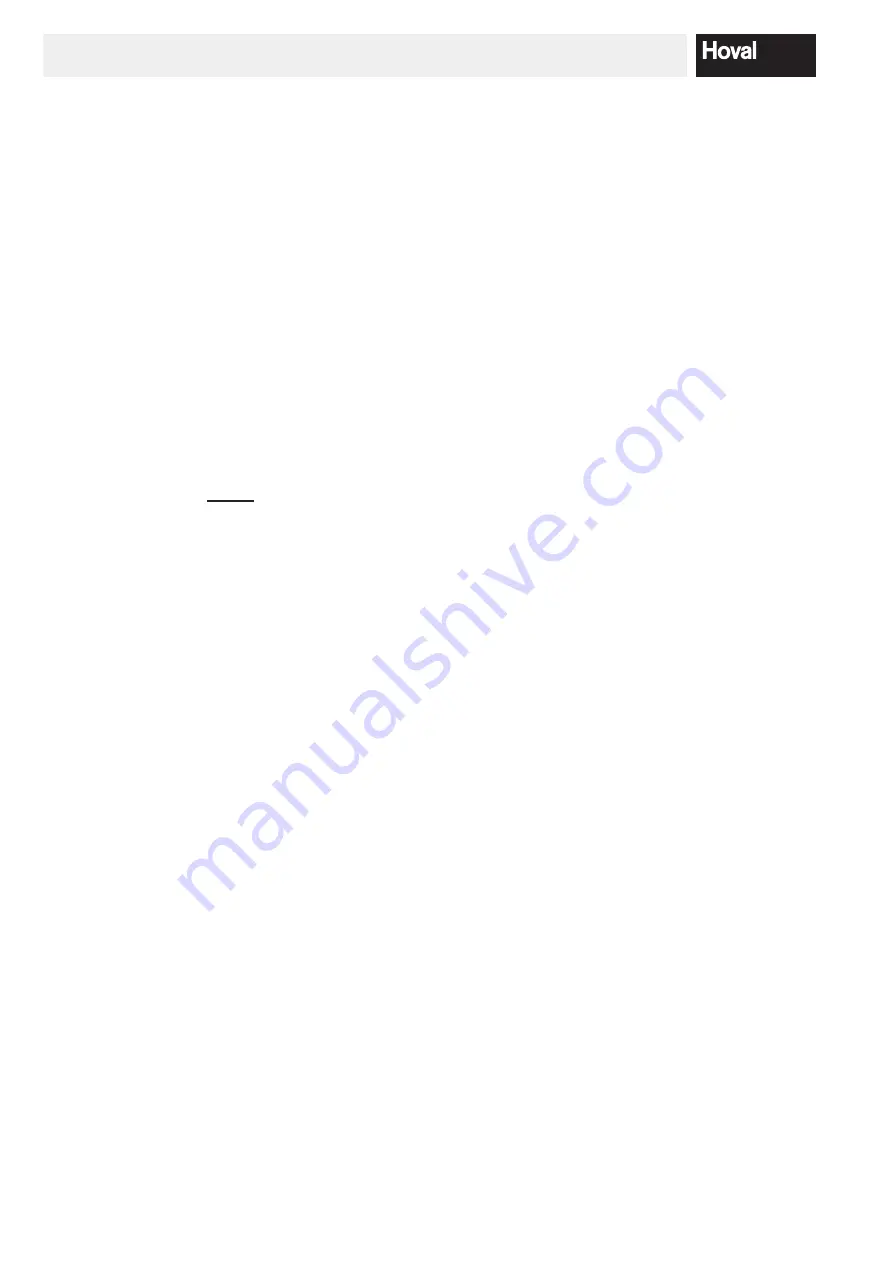
Repairing sealed components
•
During the reparation operations of sealed compo-
nents, disconnect all the equipment before removing
sealed casings etc. If, during operations, it is absolutely
necessary for the equipment to remain connected, a
leak detection device must be placed in the most criti
-
cal point so as to report any potentially-dangerous sit
-
uation.
•
Pay particular attention to what follows to guarantee
that, while intervening on electrical components, the
housing is not altered in a way so as to affect the level
of protection. This includes damage to cables, an ex
-
cessive number of connections, terminals not compli-
ance with the original specifications, damage to gas-
kets, an unsuitable installation of gaskets, etc.
•
Make sure the device is installed safely.
•
Check that the seals or sealing materials are not al-
tered in such a way that they no longer the impede the
entry of flammable environments. Spare parts must
comply with manufacturer specifications.
NOTE:
-
Using silicone sealants may inhibit the effectiveness of
a few types of leak detection equipment. It is not nec-
essary to isolate intrinsically safe components before
performing operations on them.
Reparation of intrinsically safe components
Do not apply permanent inductive or capacitive loads to
the circuit without making sure that they do not exceed
the admissible voltage and current allowed for equipment
in use.
Intrinsically safe components are the only component
type on which operations can be performed in a flamma
-
ble atmosphere. The testing device must show a correct
value. Replace components only with the parts specified
by the manufacturer.
Following a leak, other parts could lead to the combustion
of the refrigerant in the atmosphere.
Wires
Make sure wires are not subjected to wear, corrosion, ex
-
cessive pressure or vibration, that there are no sharp
edges and that they do not produce other negative effects
on the environment. The inspection must also keep into
consideration the effects of tine or the continuous vibra-
tion caused e.g. by compressors or fans.
Detection of flammable refrigerants
When searching for refrigerant leaks or if one is detected,
never use potential ignition sources (e.g. halogen search
lamp or other implement with an open flame).
Leak detection methods
The following leak detection methods are considered ac-
ceptable for systems containing flammable refrigerants.
Electric leak detectors must always be used to identify
flammable refrigerants, although they do not present a
suitable sensitivity level or require recalibration (detection
equipment must be calibrated in an area free from refrig-
erants).
Check that the detector is not a possible source of igni-
tion and that it is suitable for the refrigerant. Leak detec-
tion equipment must always be set to an LFL percentage
and calibrated depending on the refrigerant used, so the
correct gas percentage (25 % max) must be verified.
Leak detection fluids are suitable for most refrigerants,
although using detergents containing chlorine should be
avoided as this substance may react with the refrigerant
and corrode copper pipes.
If a leak is suspected, all open flames must be removed
or switched off.
If a refrigerant leak is detected that requires brazing,
all refrigerant must be extracted from the system. Oxy
-
gen-Free-Nitrogen (OFN) is then purged through the sys
-
tem both before and during the brazing procedure.
Removal and evacuation
When intervening on the cooling circuit to perform repair
work or any other type of work, always follow the normal
procedure. However, considering the risk of flammability,
we recommend following the best practices. Comply with
the following procedure:
•
Extract the refrigerant;
•
purge the circuit with inert gas;
•
evacuate;
•
Purge again with inert gas;
•
Interrupt the circuit with interruption or brazing.
The refrigerant charge must be directed to the correct re
-
cycling bottles. To make the unit safe, flushing with Ox
-
ygen-free -Nitrogen must be performed. This procedure
may have to be repeated multiple times. Do not use com
-
pressed air or oxygen for this operation.
For flushing, break the vacuum in the system with oxy
-
gen-free nitrogen and continue filling until the operating
pressure is reached. Then release into the atmosphere
and re-establish the vacuum. This process must be re
-
peated until there is no trace of refrigerant in the system.
When using the final OFN charge, the system must be
vented to the atmospheric pressure to allow the interven
-
tion. This step is essential to perform brazing operations
on the pipes.
Make sure that the vacuum pump intake is not near igni-
tion sources and that there is suitable ventilation.
Charging operations
In addition to conventional charging operations, the
following requirements must be complied with:
•
When using charging equipment, make sure that the
various refrigerants are not contaminated. Flexible
tubes or conduits must be as short as possible to re
-
duce to the minimum the quantity of refrigerant con-
tained.
•
Bottles must be positioned upright.
•
Before loading the system with refrigerant, check that
the cooling system is earthed.
46
4 221 546 / 00
SafETy InSTRUCTIonS - R32