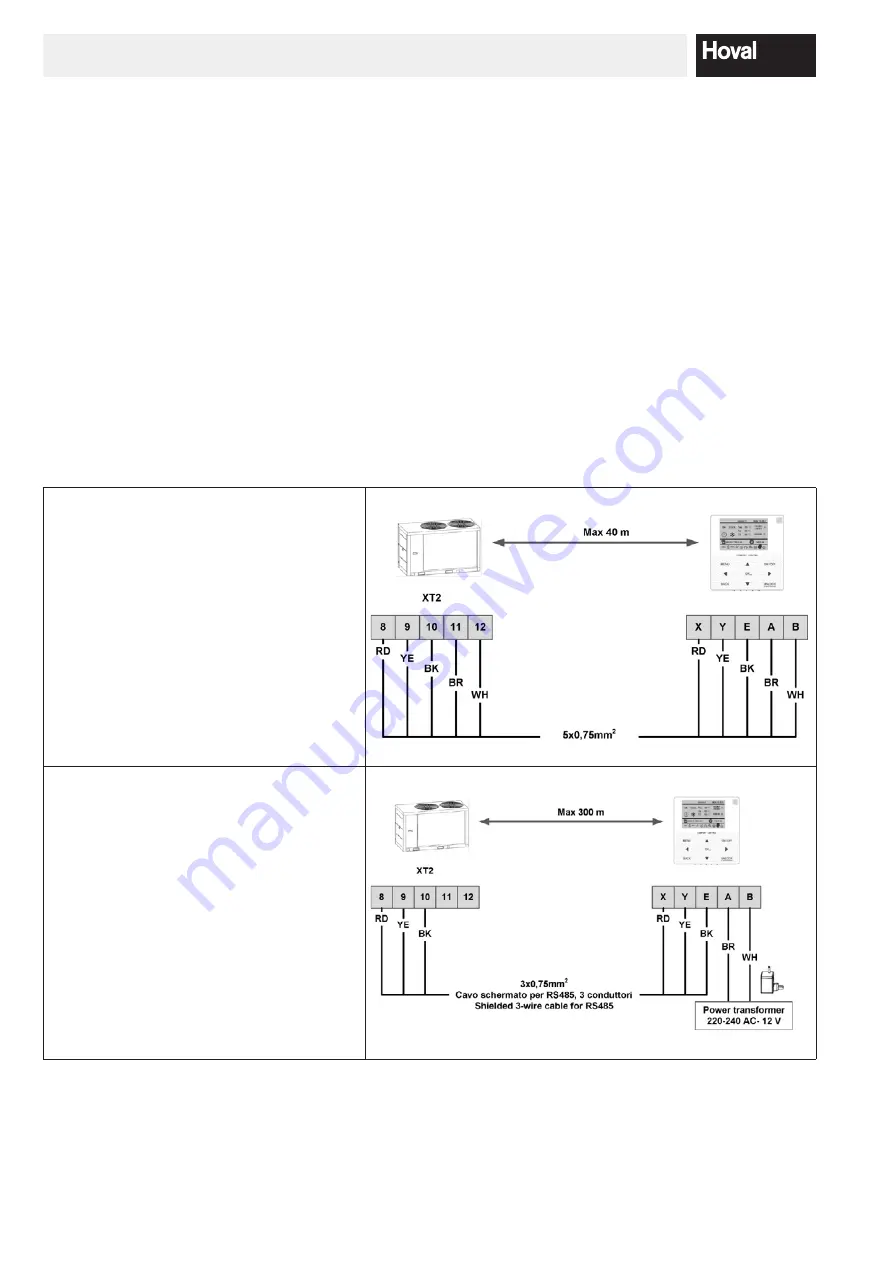
TW Probe
The sensor for checking the water temperature in the flow of the plant is installed on the flow line in the heat pump.
If units have been configured in cascade, the TW sensor of the master unit must be installed at the greatest possible
distance in the common flow of the plant.
Use the additional sensor holder in the control panel.
Do not remove the sensor from the terminals in the control panel. Only remove the sensor from the mounted sensor
holder in the flow and place it in the common flow of the plant.
Taf 1 Probe
The frost protection sensor for domestic hot water is located in the control panel in a plastic bag with a 10 m cable.
To remotely control the Taf1 sensor, electrically disconnect the sensor in the control panel (only 3 meters long) and
connect the sensor included in the bag with the Taf1 label to the same connector.
T5 Probe
The temperature sensor for switching the hot water system is located in the control panel in a plastic bag with a 10 m
cable. Connect it to the free connection “T5” in the control panel.
Installing the control module in a different location
The control module is connected to the unit with a cable.
The control module can be installed in a remote location.
Maximum distance 40 m.
Power supplied by the unit.
Maximum distance 300 m.
Separate power supply Power supply
provided with the unit.
20
4 221 546 / 00
ElECTRICal ConnECTIonS