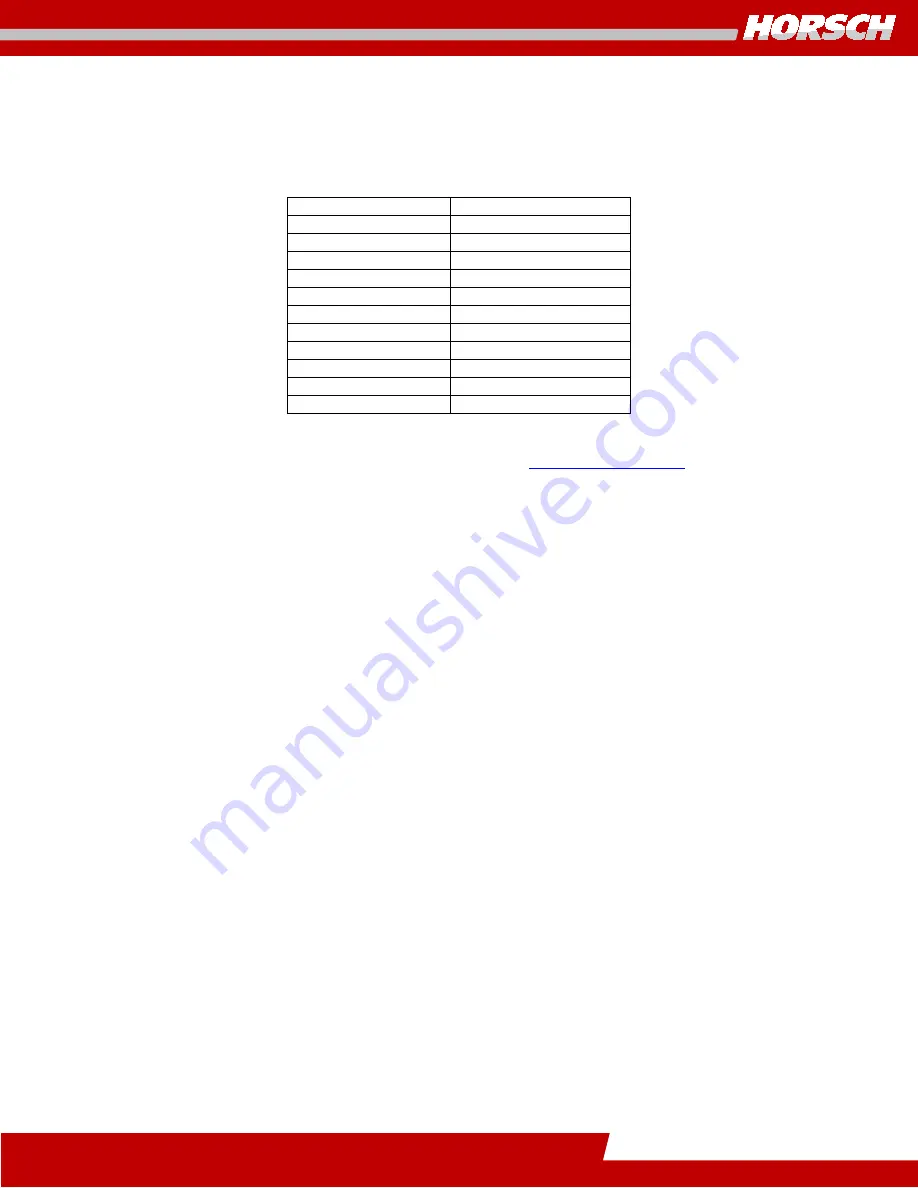
SW600 Owner’s Manual – Version 1.2 07/2018
47
www.horsch.com
Undercarriage & Track System Specifications
Trailed Track System (SW600)
Model
36” x 236”
Capacity
35 Ton
Width
36”
Length
103.5”
Surface Area
2425 in
2
per track
Total Idlers/Track
4
Idler Diameter
36”
Total Bogie/Track
4
Bogie Diameter
16”
Approx. Weight
9,000 lbs. (4090 kg)
Pressure Required
1500 PSI
Ground Pressure
12 PSI
*For further information on the track system see
Trailed Track System
in this manual.
Summary of Contents for SW 600
Page 2: ...2 SW600 Owner s Manual Version 1 2 07 2018 www horsch com...
Page 3: ...SW600 Owner s Manual Version 1 2 07 2018 3 www horsch com...
Page 10: ...10 SW600 Owner s Manual Version 1 2 07 2018 www horsch com...
Page 12: ...12 SW600 Owner s Manual Version 1 2 07 2018 www horsch com...
Page 14: ...14 SW600 Owner s Manual Version 1 2 07 2018 www horsch com...
Page 16: ...16 SW600 Owner s Manual Version 1 2 07 2018 www horsch com...
Page 18: ...18 SW600 Owner s Manual Version 1 2 07 2018 www horsch com...
Page 95: ...SW600 Owner s Manual Version 1 2 07 2018 95 www horsch com Metering System...
Page 98: ...98 SW600 Owner s Manual Version 1 2 07 2018 www horsch com Notes...