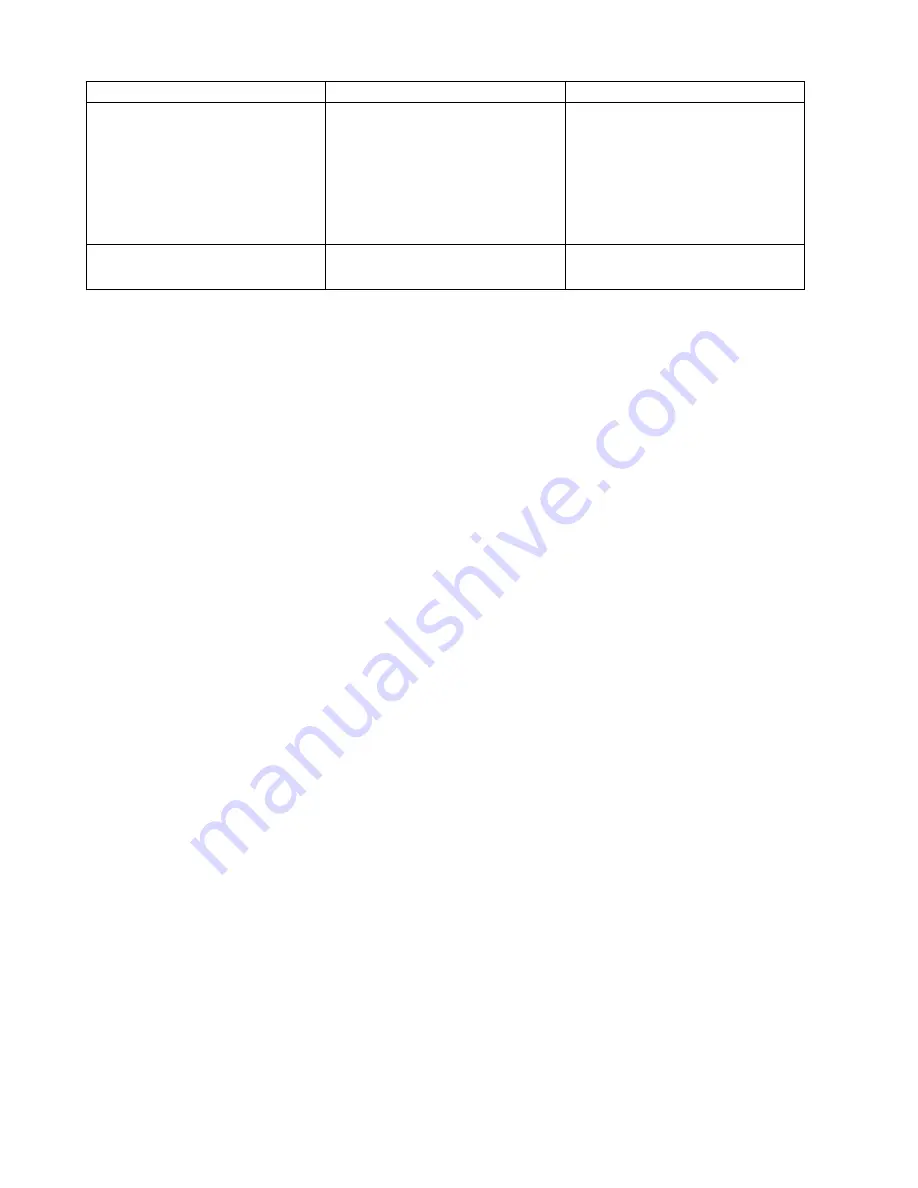
13
SYMPTOM
PROBABLE CAUSE
SOLUTION
Waste valve is stuck open.
With the extractor idle, fill a disk
holder with water and verify that
the fluid level does not decrease.
If it does, examine the Waste
vessels to determine which valve
is stuck open and replace that
valve.
Keypad lights have dimmed or
gone out.
LEDs in Keypad are burned out.
Replace Keypad.
Summary of Contents for SPE-DEX 4790
Page 1: ...SPE DEX 4790 Solid Phase Extraction System Service Manual ...
Page 6: ...5 Notes ...
Page 39: ...38 ...
Page 47: ...46 ...
Page 59: ...58 8 Schematics 8 1 Nitrogen and Solvent Delivery System ...