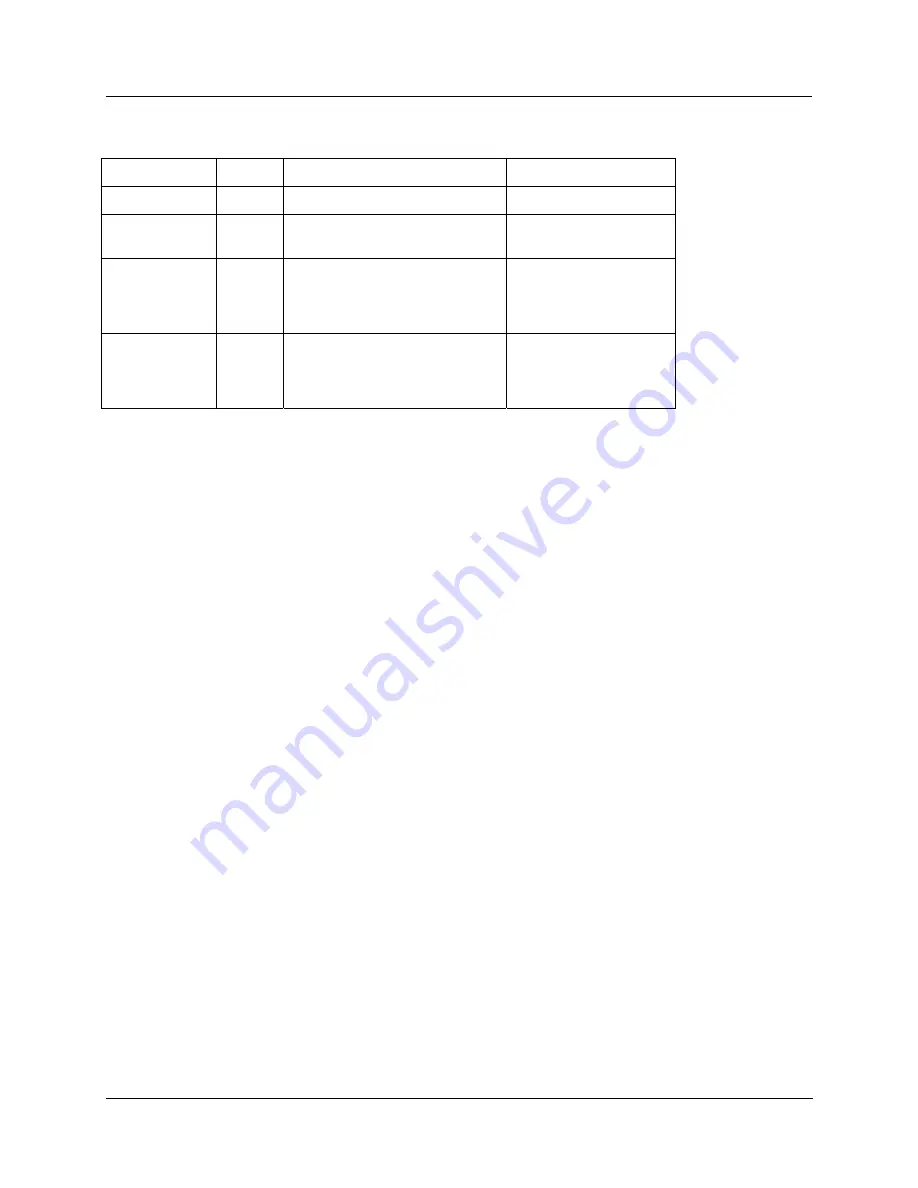
Function Blocks
SEQ Sequencer Function Block
Revision 11
HC900 Hybrid Control Designer Function Block Reference Guide
337
2/07
States
tab
Parameter
Index #
Parameter Description
Value or Selection
State Name
0
Name of State
12 characters maximum
Digital
Outputs
Digital Output States 1 to 16
Select from dropdown
menu ON(1) or OFF(0)
Event Signal 1
Event Signal #1 Tag
Select from drop-down
menu
Analog Signal Tags
Output Tags
Event Signal 2
Event Signal #2 Tag
Select from drop-down
menu
Analog Signal Tags
Output Tags
Example
The process controlled in this example is representative of many sequential batch operations.
See
H
Figure 92
.
The Sequencer function block’s digital outputs are connected to the controller digital output function blocks
to control the operation of the various field devices such as pumps, valves, solenoids and other equipment
needed to execute the batch process function. The digital outputs may also be connected to other function
blocks in the control strategy as needed.
In the example the auxiliary analog output (AUX) is connected to an analog output block to set the speed of
an external device such as a variable speed drive.
The Sequencer function block can be started, held, advanced or reset from a Honeywell operator Interface or
from digital signals as indicated in the example. The status of the Sequencer block may be monitored using
block outputs such as current state number, current step number and mode from signals available on the
block, or from the Honeywell operator interface.
The actual sequence to be executed is made up of two data sets. The first data set defines which digital
outputs will be ON or OFF for each State of the function block,
See
H
Figure 93
. Up to 50 States may be
defined for the block. Each state also has a 12 character state label that is used by the Honeywell operator
interface to indicate the active state. This data set also provides input fields to define two digital signals that
may be used to cause the sequencer to exit the current state. The Tag names in the columns for Event Signal
#1 and Event Signal #2 represent the digital signals of the control strategy that will be used to exit the
associated state.
The second data set needed to execute a sequential control strategy is the actual sequence,
See
H
Figure 94
.
This data set has a series of steps, 1 through 64. Each step is setup to activate a specific State (set of digital
outputs) from the function block. The sequencer will remain in the Step until a user specified time has
elapsed or until either of the events for the specific State transitions from OFF to ON, causing the step to
advance.
The next step in the sequence can be different depending on the action that causes the sequencer to exit the
step. Time, event 1, event 2 and advance step each allow the user to specify a unique next step value.
Depending on the item that occurs first, elapsed time, event 1, event 2, or advance, the sequencer will
advance to the specified next step. This provides the flexibility to take alternate action if the expected action
does not occur on schedule.
Sequences can be stored in the controller (data specified in
H
Figure 94) and be selected as part of a recipe or
manually through a Honeywell operator interface.